Metal casting is the cornerstone of manufacturing, where molten metal is introduced into a mold, solidifies within the mold to form a cavity, and can produce complex shapes. Among various metal casting processes, investment casting vs sand casting are two prominent methods widely used across industries. While they share the fundamental concept of pouring molten metal into prepared cavities, their processes, capabilities, and applications differ significantly.
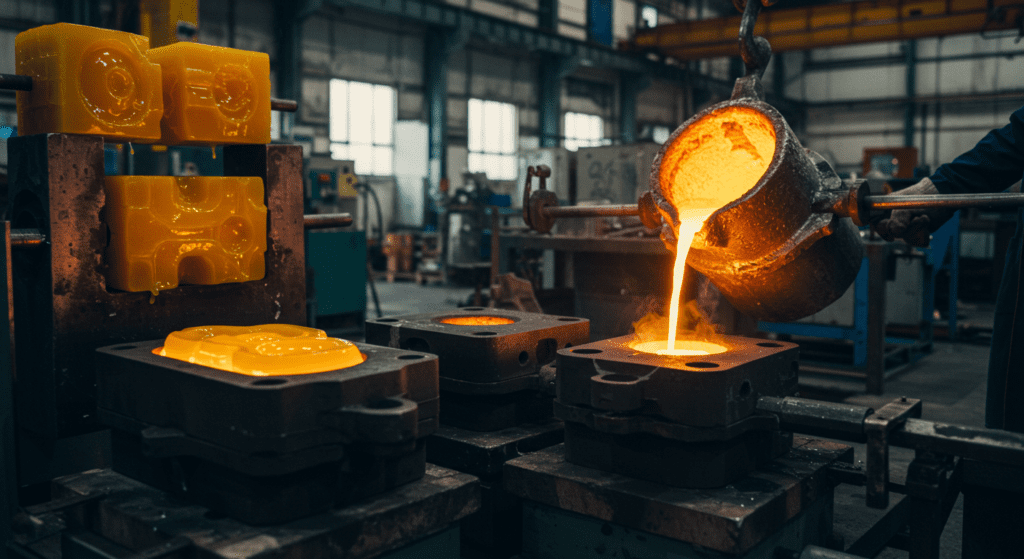
Investment Casting
Investment casting is commonly known as the lost wax method. This precision process begins with creating detailed wax patterns that exactly match the final desired components. Molten wax is injected into a mold to create these precise wax patterns, each representing the final casting. For smaller components, multiple wax patterns are typically connected to a prefabricated wax gating system, commonly referred to as a “tree” or cluster. This arrangement maximizes efficiency by allowing multiple parts to be cast simultaneously.
If internal cavities are required in the final component, cores made of soluble wax or ceramic can be incorporated into the wax pattern at this stage. These cores create the internal geometries that would otherwise be impossible to achieve in a single-piece mold.
The assembled wax tree is repeatedly dipped into ceramic slurry, then coated with a layer of refractory material, usually fine sand. This dipping and coating process is repeated six to eight times, with drying periods between each layer, to form a solid ceramic shell or “investment” around the wax pattern. Each layer serves to strengthen the mold and improve its ability to withstand the high temperatures of molten metal. The shell then undergoes a drying process, which may last 24 to 36 hours, ensuring complete solidification of the ceramic material.
Once the ceramic shell is sufficiently dry and hardened, the wax pattern must be removed. This is typically accomplished by placing the shell in an autoclave, where high-pressure steam and heat rapidly melt the wax, leaving an empty ceramic cavity shaped exactly like the desired component. This step gives the process its alternative name, “lost wax” casting, as the wax literally disappears from the mold.
Before pouring the molten metal, the ceramic mold needs to be preheated in a high-temperature furnace, typically around 1000-1100°C (1832-2012°F). This crucial step serves multiple purposes: it cures and strengthens the ceramic material, burns out any remaining wax residue, and prevents thermal shock when the molten metal is introduced. The molten metal of the specified alloy is then immediately poured into the cavity, typically using gravity or vacuum assistance to ensure complete filling and minimize porosity.
After the molten metal cools and solidifies within the ceramic mold, the fragile ceramic shell is carefully broken away to reveal the metal casting. This “knockout” process must be conducted with precision to avoid damaging the newly formed metal components.
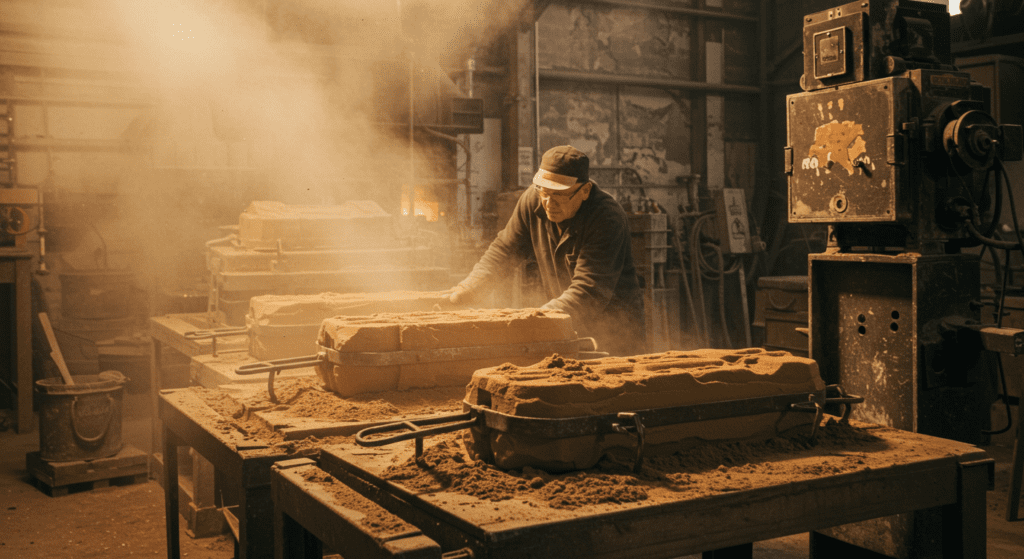
Sand Casting
Sand casting, also known as sand mold casting, is one of the oldest and most widely used casting processes in manufacturing. The process begins with creating a pattern, which is a replica of the desired object. The pattern is typically made of wood, metal, or plastic and includes allowances for shrinkage and machining.
The pattern is then placed in a molding box or flask consisting of two halves: the cope (top) and the drag (bottom). Molding sand, a mixture primarily composed of sand (usually silica), a binder (such as clay or resin), and moisture, is packed tightly around the pattern in both the cope and drag. The sand is rammed or vibrated to ensure it completely fills the mold and conforms closely to the pattern’s shape, creating a detailed negative impression.
With the sand mold prepared around the pattern, a gating system is installed. This system consists of channels including a pouring cup, sprue, runners, and gates designed to facilitate the flow of molten metal into the cavity. Risers may also be added to provide reservoirs of molten metal that feed the casting as it shrinks during solidification, preventing defects such as shrinkage cavities.
With the gating system in place, the pattern is carefully removed from the sand mold, leaving a cavity with the shape of the desired casting. If internal features or voids are required in the casting, cores (typically made of sand and formed separately) are inserted into the cavity before closing the mold. These cores create the internal geometries of the final casting and are typically removed during the cleanup process.
The two halves of the sand mold (cope and drag) are then carefully aligned and clamped firmly together to prevent separation during the casting process. Molten metal of the chosen alloy, which may include iron, steel, aluminum, or bronze, is poured into the pouring cup. From there, the molten metal flows through the sprue, runners, and gates into the mold cavity, filling the space left by the removed pattern and inserted cores.
After the molten metal has been introduced into the cavity, it is allowed to cool and solidify within the sand mold. The cooling rate can be controlled to influence the microstructure and properties of the final casting. Once the metal has solidified, the sand mold is broken apart or “knocked out” to retrieve the raw casting. The sand can often be reclaimed and reused for future castings, making the process economically efficient.
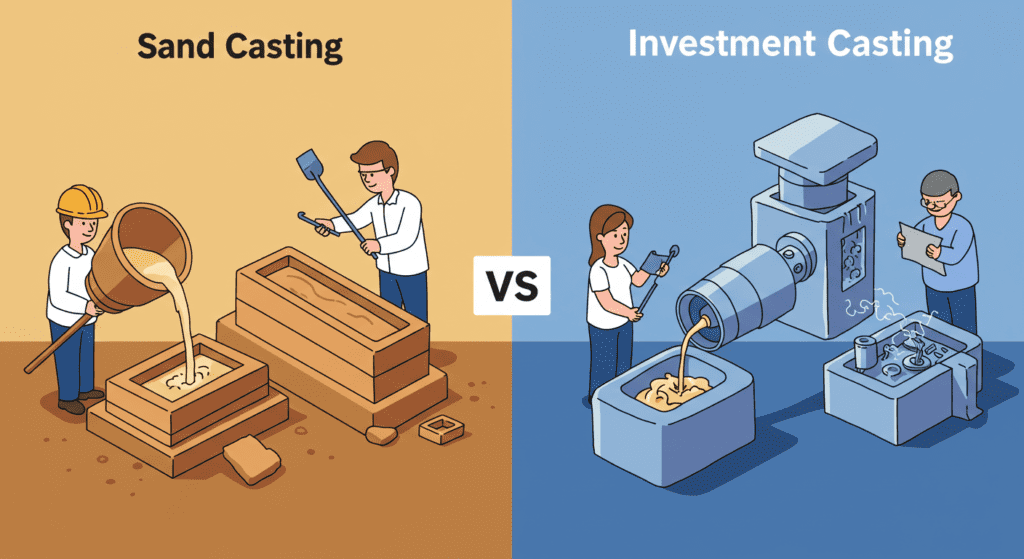
Difference Between Sand Casting and Investment Casting
Dimensional Accuracy
Investment casting excels in producing components with exceptional dimensional precision. This process can typically achieve accuracy that requires no additional machining operations for many applications. The process is capable of achieving tight tolerances of ±0.005 inches per inch.
Sand casting typically does not demand such strict tolerances, and parts produced through this method often require subsequent machining to achieve the desired precise dimensions. General dimensional accuracy ranges from ±0.01 to ±0.03 inches per inch, which is sufficient for many industrial applications.
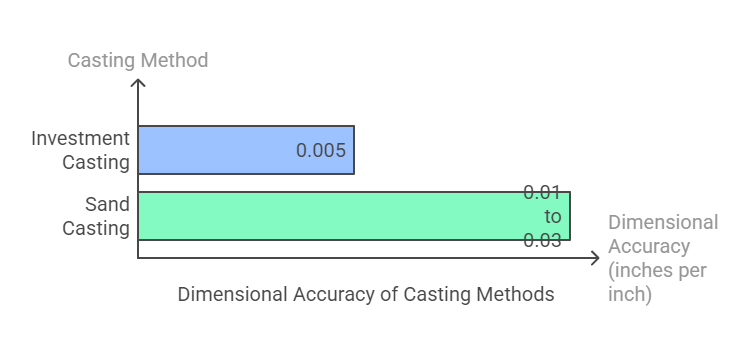
Surface Finish
Investment casting is characterized by smooth, high-quality surfaces that often minimize or even eliminate the need for extensive post-processing. The typical surface finish achieved through investment casting ranges from Ra 3.2 to 12.5 μm, approximately equivalent to 125 Ra as-cast.
Sand casting typically results in rougher, less uniform surface finishes, often necessitating additional post-processing steps to achieve smoother textures. The typical surface finish for sand casting ranges from 25 to 250 μm, or approximately 250 Ra as-cast.
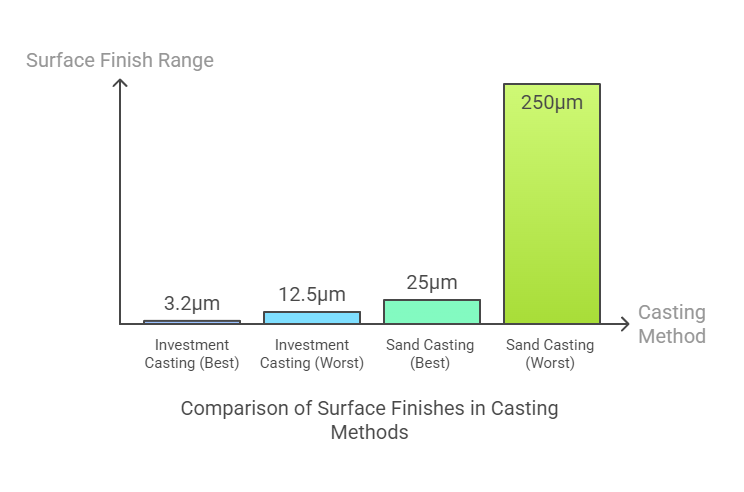
Cost
The typical per-piece cost for investment casting ranges from $10 to over $500, depending on complexity, material, and quantity. While the individual part cost may be higher than other methods, the reduction in machining requirements can offset these costs for complex components.
The typical per-piece cost for sand casting ranges between $5 to over $200, making it generally more economical for larger, less intricate parts. The tooling costs for sand casting are typically lower, with pattern creation being less expensive than the tooling required for investment casting. This makes sand casting particularly cost-effective for prototype runs or limited production quantities.

Material Compatibility
Investment casting is particularly renowned for its ability to handle specialized high-performance alloys, such as nickel and cobalt-based superalloys. These materials are often difficult to machine, making investment casting an ideal production method for components made from these materials. The process can also accommodate a wide range of other metals, including stainless steel, tool steel, aluminum, and bronze.
Sand casting is typically more suitable for lower melting point alloys, such as cast iron and bronze, though it can also be used with steel, aluminum, and other metals. The sand mold’s ability to withstand high temperatures can be a limiting factor for certain high-melting-point alloys, though specialized sand mixtures can extend this capability.
Process Complexity and Component Weight
The investment casting process is more complex with more steps, often resulting in longer production lead times. From creating wax patterns to shell building, dewaxing, firing, and final casting, each step requires precise control and specialized equipment.
In terms of component size, investment casting typically handles components weighing 100 pounds or 150 pounds or less, with most applications focusing on small to medium-sized parts with complex geometries. Sand casting, in contrast, can be used for components weighing up to several tons, making it suitable for large industrial components like engine blocks, machine bases, and structural elements.