Manufacturing professionals face the critical challenge of selecting between sand casting and die casting processes for metal forming projects. Making the wrong choice can result in excessive costs, quality compromises, and missed production targets—severely impacting competitive advantage.
By understanding the fundamental differences in materials, costs, precision, volume capabilities, and production speed, manufacturers can optimize their casting selection for maximum efficiency and product quality.
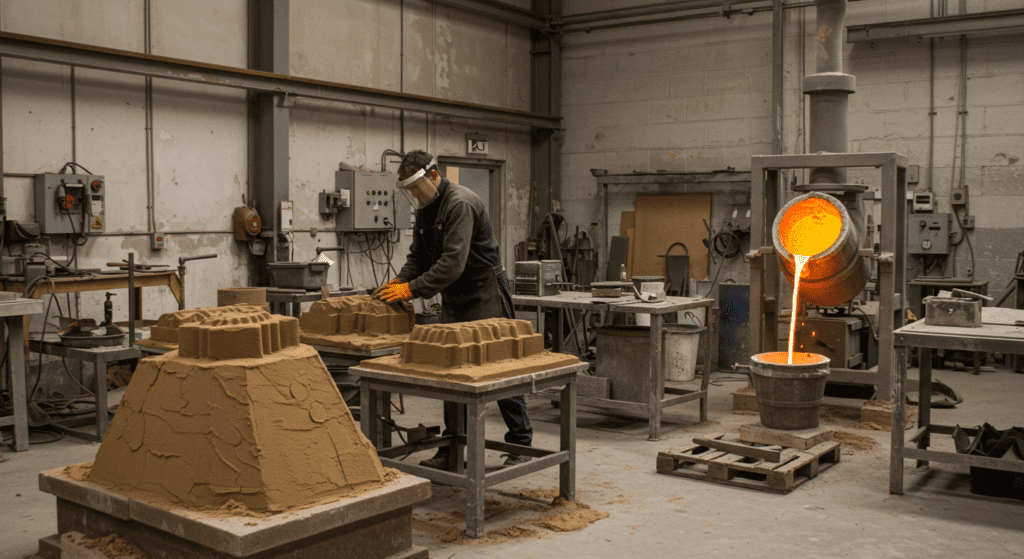
Sand Casting
Sand casting is a versatile metal forming process that has been utilized for centuries across various industries. This traditional method uses sand as the primary material for creating molds into which molten metal is poured to form parts.
The process begins with pattern making, where a replica of the desired part (typically made from wood, metal, or plastic) serves as the template. This pattern is placed in a molding box called a flask, which consists of two halves: the cope (top) and the drag (bottom). Molding sand—primarily silica sand mixed with clay and water (known as “green sand” because of its moisture content rather than its color)—is firmly packed around the pattern to create a negative impression of the desired part.
After removing the pattern, a gating system is created within the mold—think of it as the plumbing system through which molten metal will flow. For parts that need hollow sections, additional sand shapes called cores are positioned within the cavity. The molten metal, heated to specific temperatures, is then poured into the mold where it cools and solidifies. Once solidified, the sand mold is broken apart to retrieve the casting, which is then finished through various cleaning and machining operations.
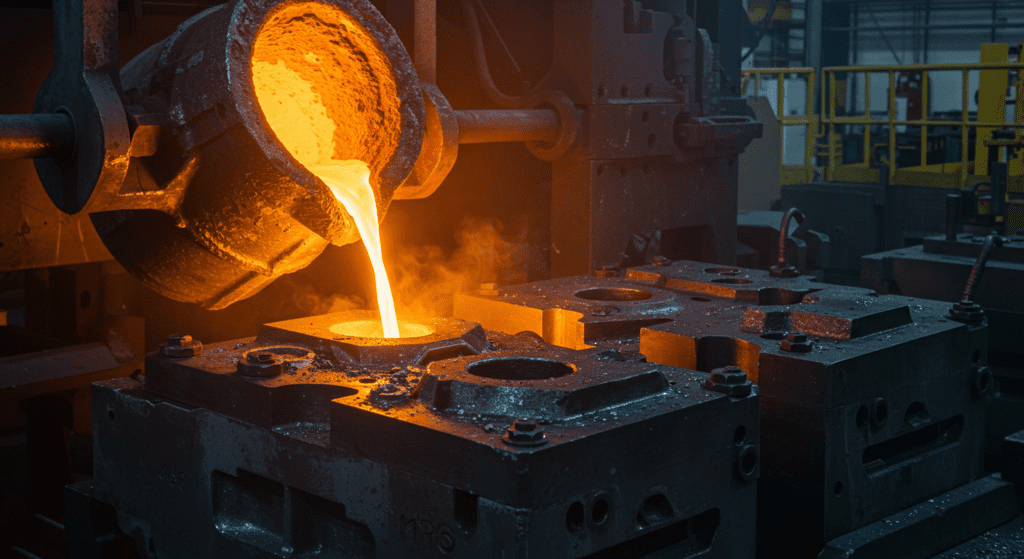
Die Casting
Die casting represents a more mechanized approach to metal forming, characterized by the injection of molten metal into reusable steel molds (dies) under significant pressure.
The process begins with mold preparation, where reusable steel dies consisting of two halves are sprayed with a lubricant to ensure clean part ejection and temperature control. These dies are then securely clamped together in a die casting machine. The molten metal, maintained at precise temperatures, is rapidly injected into the cavity under pressures that commonly reach 1,000 to 20,000 pounds per square inch—roughly equivalent to the pressure experienced more than 13,000 feet underwater. This extreme pressure ensures the metal fills even the most intricate details of the mold.
After solidification, which happens remarkably quickly due to the cooling effect of the metal dies, the die opens and ejector pins push the newly formed casting out.
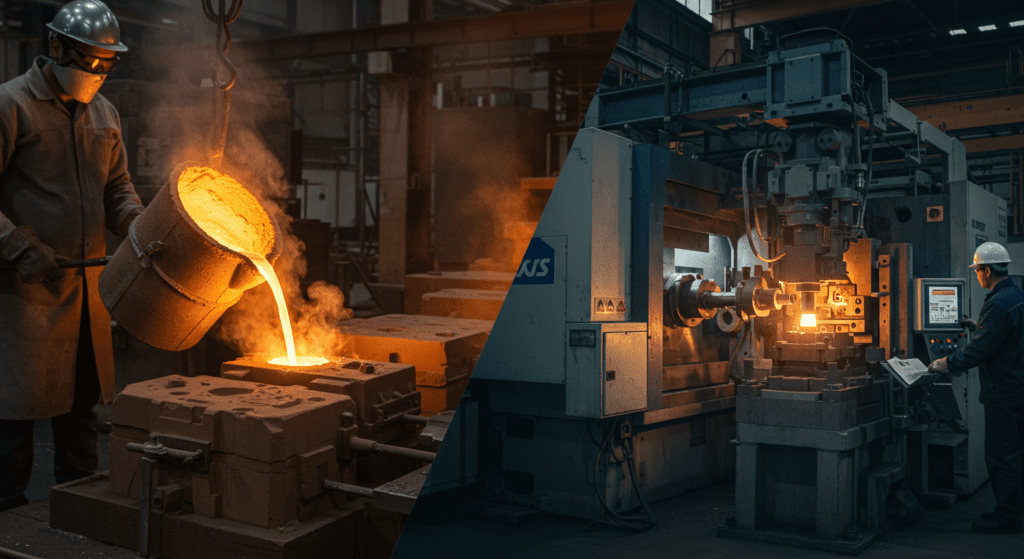
Differences Between Sand Casting and Die Casting
Materials
While die casting primarily works with non-ferrous metals like aluminum, zinc, magnesium, and copper alloys, sand casting can handle virtually any metal that can be melted. This includes high-temperature ferrous alloys that would quickly damage die casting equipment. For instance, a large iron engine block for industrial machinery would be a natural candidate for sand casting, while the aluminum transmission housing that connects to it might be die cast.
Die casting’s limitation with ferrous metals isn’t merely a preference but a practical constraint. The high melting temperatures of iron and steel (approximately 2,800°F compared to aluminum’s 1,220°F) would rapidly deteriorate the steel dies through thermal fatigue and erosion. Additionally, the molten metal would partially weld to the die surface during solidification, making part ejection extremely difficult.
Cost
Sand casting features lower initial tooling investments, with pattern and flask expenses typically ranging from $500 to $20,000. This makes sand casting particularly attractive for prototyping, low-volume production, or situations requiring frequent design changes.
Die casting requires substantial upfront investment in precision-machined steel dies, with tooling costs often between $3,000 and $500,000 or more for complex, multi-cavity dies. However, the per-unit cost decreases dramatically as production volume increases. Industry experience suggests the crossover point where die casting becomes more economical than sand casting typically occurs around 5,000 to 10,000 units.
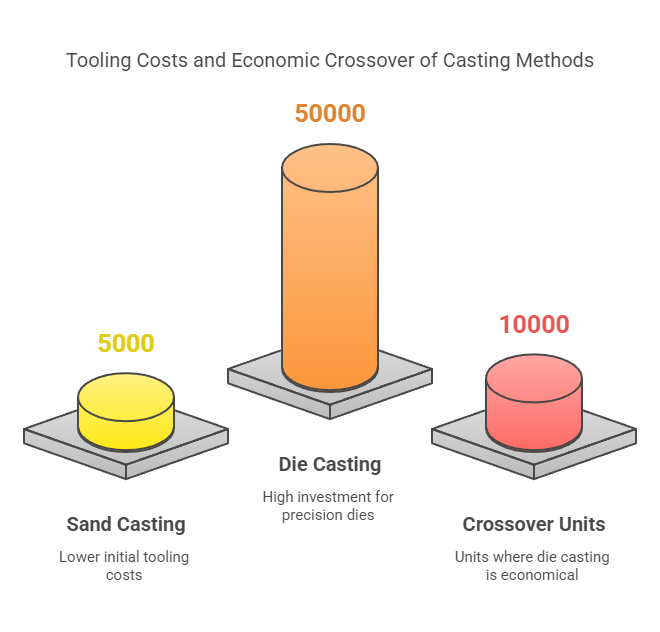
Dimensional Accuracy and Surface Finish
Die casting delivers superior dimensional precision with tolerances of approximately ±0.002 inches per inch of dimension. In practical terms, this means a 5-inch die cast part would typically maintain accuracy within ±0.010 inches—precision that’s often visible as tight, consistent seams on consumer products like electronic device housings. The process also produces excellent surface finishes with roughness values (Ra) typically between 1 and 2.5 micrometers, creating surfaces smooth enough that little to no additional finishing is required.
Sand casting offers more modest dimensional control, with typical tolerances around ±0.08 inches for components up to 0.4 inches in dimension. Surface finish is considerably rougher, with Ra values generally between 12.5 and 50 micrometers—a difference you can feel by running your finger across the surface, which would detect the characteristic granular texture left by sand particles. This rougher finish often necessitates additional machining operations to achieve final specifications, particularly for mating surfaces or parts with aesthetic requirements.
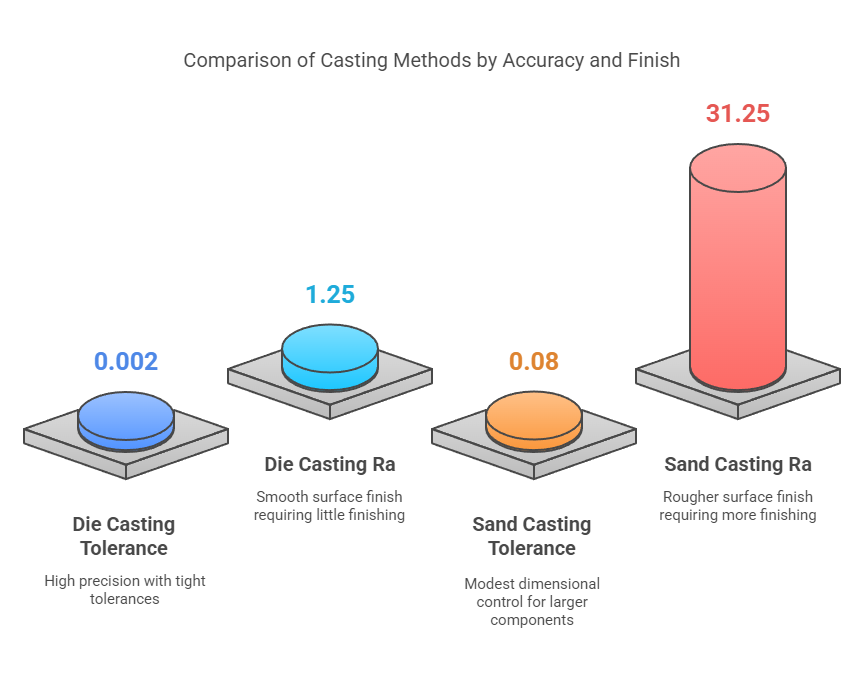
Production Volume and Speed
Sand casting excels in low to medium production scenarios, from one-off prototypes to a few thousand units. Each casting typically requires a new sand mold, resulting in production cycles measured in hours rather than minutes. However, multiple patterns can be used simultaneously to increase throughput when needed.
The initial setup of die casting may take weeks or months to design and manufacture the dies, but once production begins, parts can be produced continuously at rates that make sand casting seem glacial by comparison. Once the die is mounted in the machine, cycle times typically range from 20 seconds to 2 minutes per part. This remarkable speed comes at the cost of flexibility—any design change requires extensive die modifications or completely new tooling.
Design Complexity and Size Limitations
Sand casting accommodates remarkable design complexity and size flexibility that die casting simply cannot match. The process can produce extremely large components weighing several tons—imagine massive pump housings for municipal water systems or intricate engine blocks for ships. Complex internal passages are readily created through the use of sand cores, allowing designers to incorporate internal cooling channels, oil galleries, or structural reinforcements without concern for part removal from the mold.
Die casting, while capable of producing parts with thin walls (down to 0.5mm) and intricate external features, is typically limited to components weighing less than 75 pounds due to practical constraints of machine clamping force and metal solidification dynamics. Within these constraints, die casting excels at producing complex shapes with consistent quality and excellent surface finish. The process is particularly well-suited for parts with numerous thin-walled sections like electronic enclosures or complex automotive components that require high dimensional stability.