Control Points in Investment Casting
Effective Process Control in Investment Casting requires vigilant monitoring at multiple stages to ensure consistent quality and performance of final components. According to industry data, foundries implementing comprehensive process controls see defect rates drop by 40-60% compared to those relying on end-product inspection alone.
Raw Material Control and Verification
Ensuring the quality and consistency of raw materials is fundamental to the investment casting process. A 2023 industry study by the Investment Casting Institute found that 32% of casting defects originate from material inconsistencies.
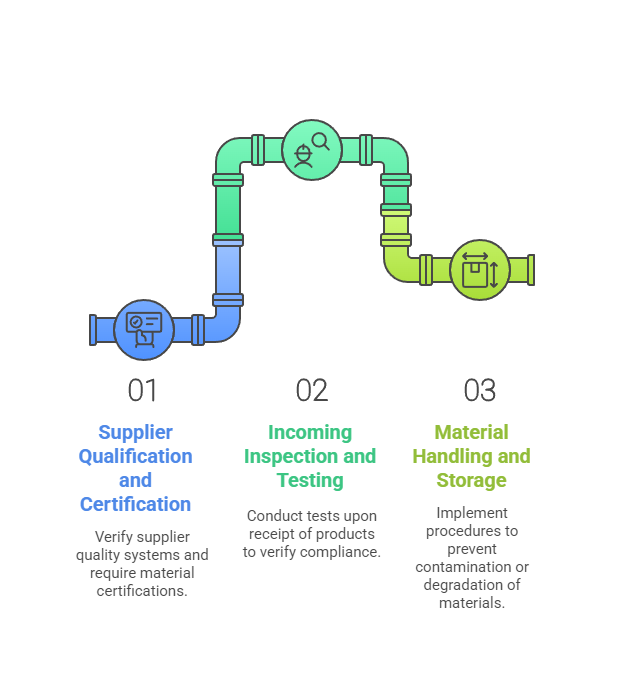
- Supplier qualification and certification: Verify supplier quality systems and require material certifications. Establish formal supplier quality agreements that define specifications, testing requirements, and non-conformance protocols.
- Incoming inspection and testing: Conduct tests upon receipt of products to verify compliance. This includes chemical analysis using spectrometry to confirm alloy composition meets standards (ASTM, AMS, SAE), examining wax properties (hardness, ash content, melting point), and verifying ceramic material characteristics (particle size distribution, refractoriness).
- Material handling and storage: Implement appropriate procedures to prevent contamination or degradation of materials before use. Maintain controlled temperature and humidity conditions for wax storage, segregate alloys to prevent cross-contamination, and protect ceramic materials from moisture.
Wax Pattern Quality Assurance
Wax patterns form the foundation for the final casting’s geometry.
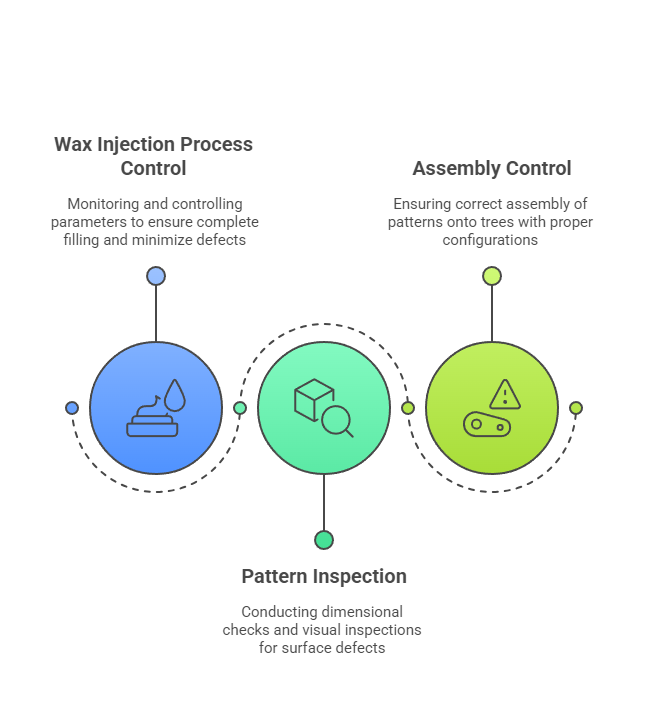
- Wax injection process control: Monitor and control parameters such as wax temperature, injection pressure, and cycle time to ensure complete filling and minimize defects.
- Pattern inspection: Conduct dimensional checks against drawings and specifications using Coordinate Measuring Machines (CMM), laser scanners, and precision gauges. Perform 100% visual inspection for surface defects including cracks, bubbles, unfilled areas, and handling damage.
- Assembly control: Ensure patterns are correctly assembled onto trees with appropriate gating and runner configurations. This requires verification of alignment and joint integrity, with special attention to critical areas that could impact metal flow during casting.
Ceramic Slurry and Shell Building Control
The ceramic shell must withstand thermal shock and metal static pressure during casting while precisely replicating pattern details.
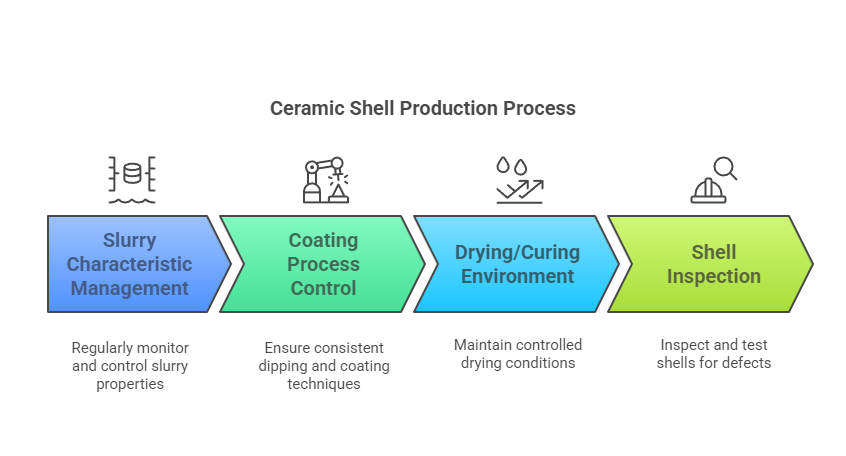
- Slurry characteristic management: Regularly monitor and control key slurry characteristics including viscosity, pH, temperature, specific gravity, binder concentration (%SiO2), and gel time. Viscosity directly affects layer thickness and uniformity, with deviations potentially causing weak points or poor surface finish.
- Coating process control: Ensure consistent dipping, draining, and stuccoing techniques to achieve uniform layer thickness and complete coverage. This often requires standardized dipping times, controlled withdrawal rates, and consistent stucco application methods, especially for complex geometries with internal passages.
- Drying/curing environment: Maintain strictly controlled temperature, humidity, and airflow during inter-layer drying cycles. Environmental monitoring systems should record conditions continuously, with deviations triggering immediate corrective actions to prevent shell defects.
- Shell inspection: Visually inspect shells for cracks or damage before proceeding to the next process stage. Advanced foundries implement non-destructive testing methods such as X-ray or ultrasonic testing to check for internal shell defects, while modulus of rupture (MOR) testing verifies shell strength.
Dewaxing and Firing Process Monitoring
These critical steps prepare the shell to receive molten metal and significantly impact casting quality.
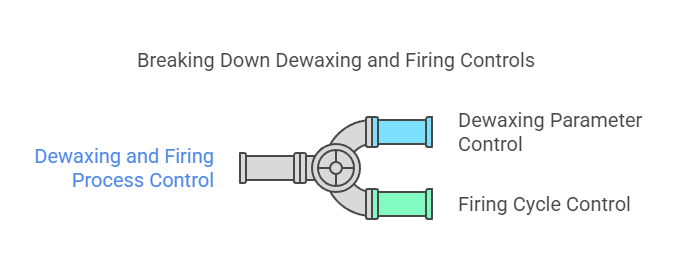
- Dewaxing parameter control: Monitor and control temperature, pressure, and time in steam autoclaves or furnace burnout cycles. Incomplete wax removal can lead to ash or carbon residue that contaminates the casting, while excessive thermal shock can damage the shell structure.
- Firing cycle control: Precisely control furnace temperature profiles and atmosphere during shell firing. This includes tightly managed heating rates, hold times, peak temperatures, and cooling rates to achieve optimal strength, remove all organic residuals, and reach the correct casting preheat temperature.
Metal Melting and Pouring Parameter Control
The melting and pouring phase largely determines the metallurgical integrity of the final casting.
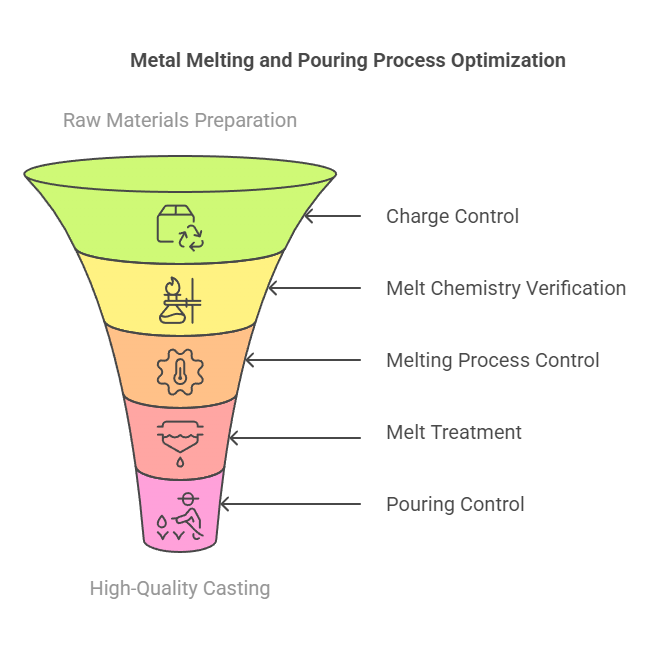
- Charge control: Use clean, correctly identified, and segregated scrap and virgin materials. Implement material tracking systems to ensure complete traceability from raw material receipt through final casting.
- Melt chemistry verification: Sample each melt for chemical analysis before pouring to verify proper alloy composition. Modern foundries employ spectrometry to provide rapid analysis, allowing for real-time adjustments if necessary.
- Melting process control: Control furnace temperature, melting time, and atmosphere to prevent excessive gas absorption or alloy degradation. Different alloys require specific melting protocols to achieve optimal properties.
- Melt treatment: Execute necessary degassing, deoxidation, and dross removal procedures to ensure metal cleanliness. These treatments directly impact the mechanical properties and integrity of the final casting.
- Pouring control: Maintain consistent and correct pouring temperature and control pouring rate/speed.
Post-Casting and Final Inspection Protocols
This final stage verifies that finished castings meet all requirements before delivery to customers.
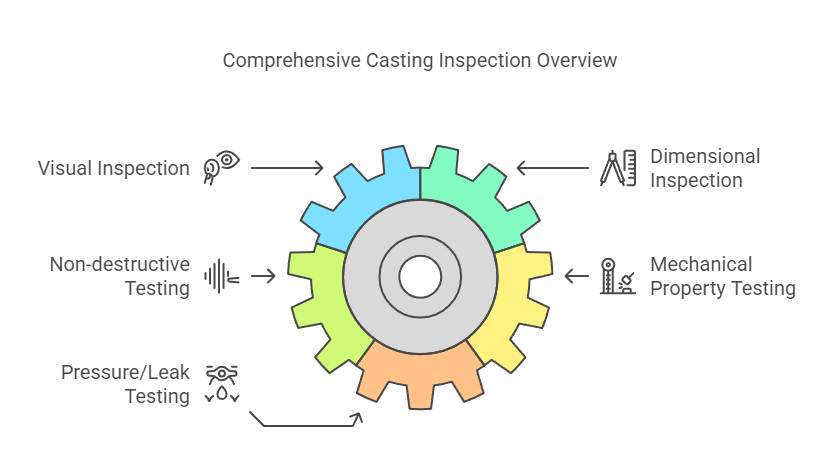
- 100% visual inspection: Examine each casting for surface defects such as cracks, porosity, unfilled areas, inclusions, distortion, scale, or sand holes.
- Dimensional inspection: Verify critical dimensions and tolerances using CMM, scanners, gauges, or fixtures. Digital measurement data can be automatically compared to CAD models to quickly identify deviations.
- Non-destructive testing (NDT): Perform specified NDT according to part criticality and customer requirements. Common methods include liquid penetrant inspection, magnetic particle inspection, radiographic testing, and ultrasonic testing.
- Mechanical property testing: Conduct destructive testing on representative samples or test bars if required by specifications. Tests typically include tensile strength, yield strength, elongation, and hardness measurements.
- Pressure/leak testing: For components designed to withstand pressure, specialized testing confirms integrity and identifies potential leakage points.
Quality Control Techniques and Tools
Dimensional Verification Methods
Ensuring castings conform to precise geometric dimensions and tolerances is critical, especially for components requiring assembly or specific functional fits.
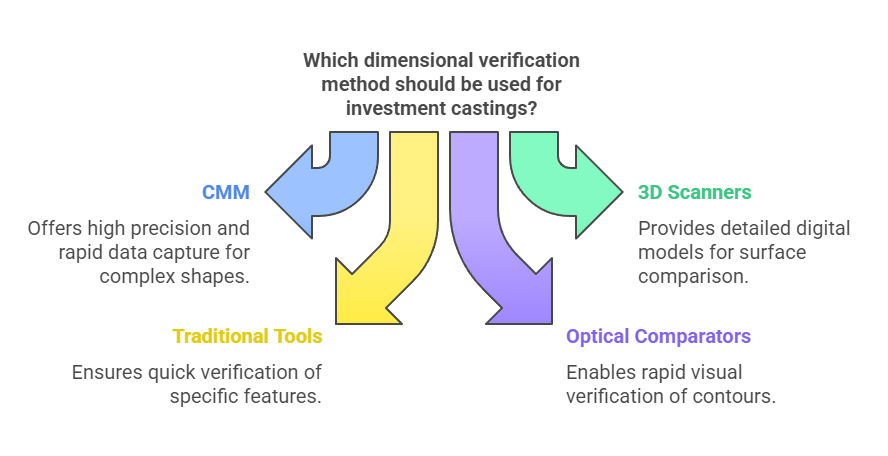
- Coordinate Measuring Machines (CMM): These automated machines use probes to measure three-dimensional geometric shapes with high precision. Modern CMMs can rapidly capture thousands of data points to verify complex forms and tight tolerances common in investment castings.
- 3D Scanners (Laser/Optical): These tools capture dense point clouds of casting surfaces, creating digital 3D models for comparison to original CAD design data. The resulting deviation analysis provides comprehensive dimensional verification, particularly valuable for complex free-form surfaces.
- Traditional Metrology Tools: Standard measuring instruments such as calipers, micrometers, height gauges, thread gauges, and custom functional gauges remain essential for routine inspections. These tools offer quick verification of specific features without requiring complex setup.
- Optical Comparators/Shadowgraphs: These systems project an enlarged profile of components onto a screen for comparison with overlays. They provide rapid visual verification of contours and specific features that might be difficult to measure with contact methods.
Non-Destructive Testing (NDT) Suite
NDT methods evaluate casting integrity internally and at the surface without damage, allowing complete inspection of critical components.
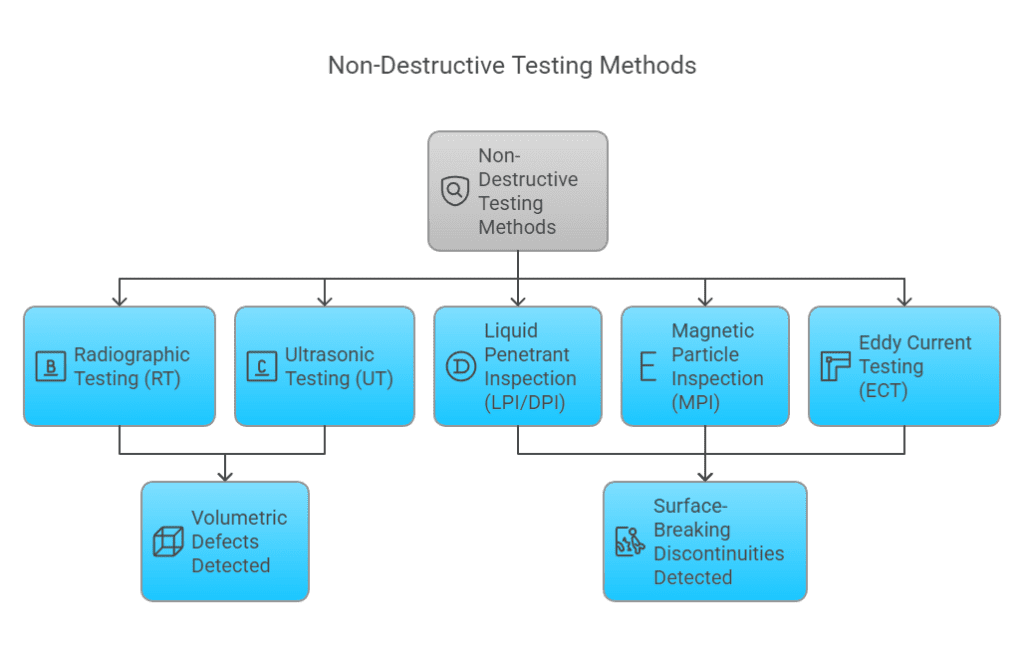
- Radiographic Testing (RT): Uses X-rays or gamma rays to create images of internal casting structures, revealing volumetric defects like porosity, shrinkage, inclusions, and internal cracks. Advanced computed tomography (CT) provides detailed 3D visualization of internal geometries.
- Ultrasonic Testing (UT): Transmits high-frequency sound waves into castings and analyzes reflected echoes to detect internal defects. This method is particularly effective for thicker sections and can be automated for production environments.
- Liquid Penetrant Inspection (LPI/DPI): A surface testing method using colored or fluorescent liquid penetrants that seep into surface-breaking discontinuities. The developer then draws out the penetrant to make defects visible. Fluorescent penetrant inspection (FPI) provides enhanced sensitivity under ultraviolet light.
- Magnetic Particle Inspection (MPI): Used for ferromagnetic materials, this method involves magnetizing parts and applying fine magnetic particles. These particles concentrate at defect locations where magnetic field leakage occurs, forming visible indications of surface and near-surface flaws.
- Eddy Current Testing (ECT): Induces electrical currents in conductive materials, with defects disrupting these currents and being detected by sensors. This method offers rapid, automated inspection capability for surface and near-surface defects.
Material Analysis and Verification
Verifying that cast materials meet specified chemical composition and possess required mechanical and metallurgical properties ensures functional performance.
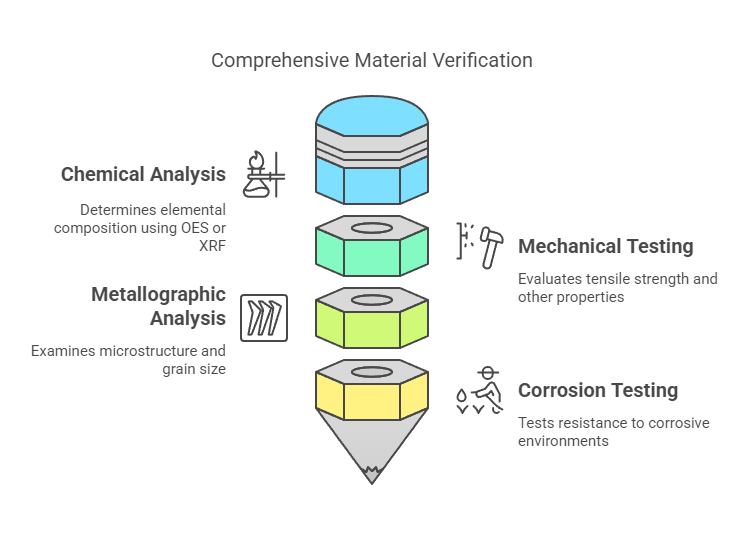
- Chemical Analysis: Primarily using Optical Emission Spectrometry (OES) or X-ray Fluorescence (XRF) to determine elemental composition. Modern systems provide results in minutes, allowing for verification before casting or certification of final components.
- Mechanical Testing: Evaluating properties such as tensile strength, yield strength, elongation, hardness, and impact toughness. These destructive tests are typically performed on separately cast test bars or specimens machined from production castings.
- Metallographic Analysis: Preparing and examining polished and etched cross-sections under microscopes to evaluate microstructure, grain size, and phase distribution. This analysis reveals material quality aspects invisible to other inspection methods.
- Corrosion Testing: Evaluating material resistance to specific corrosive environments through standardized testing protocols that simulate service conditions. This verification is particularly important for components used in aggressive environments.
Statistical Process Control (SPC)
In investment casting, Statistical Process Control applies monitoring techniques to identify trends and variations before they result in defects.
SPC relies on monitoring Key Input Variables (KIVs)—controllable process parameters such as wax temperature, slurry viscosity, firing temperature, and pouring speed—and Key Output Variables (KOVs)—measurable characteristics like pattern dimensions, shell thickness, casting hardness, and defect rates.