custom sand casting service
With precision engineering and decades of expertise, we transform molten metal into flawless sand castings, delivering durable, high-quality components that exceed industry standards and customer expectations.
Why work with a sand casting company like us
Customized solutions
24/7 customer service
Product Inspection
Fast delivery
what is sand casting
Sand casting is one of the oldest and most versatile metal forming processes used in manufacturing. It involves creating a mold from sand and then pouring molten metal into this cavity to form a part.
The basic process begins with creating a pattern (a replica of the desired object) around which sand is packed to form a mold. The pattern is removed, leaving a cavity in the sand. Molten metal is then poured into this cavity and allowed to cool and solidify. Once solidified, the sand mold is broken away to reveal the cast part.
This method can be used with various metals including iron, steel, aluminum, bronze, and brass. It’s particularly valuable for producing complex shapes that would be difficult or expensive to make using other manufacturing methods.
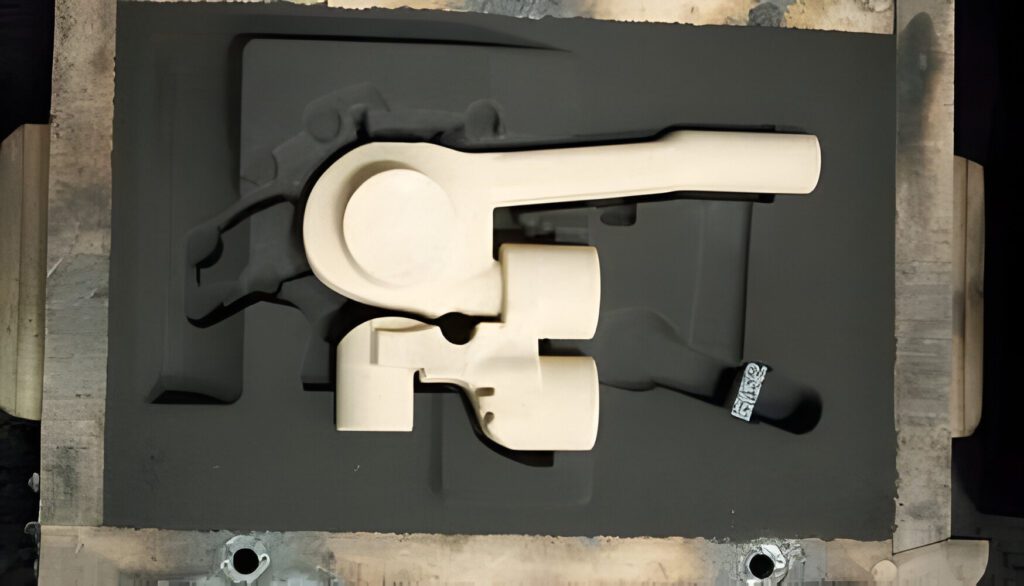
Our Sand Casting Capabilities
Capability | Specification | Notes |
---|---|---|
Materials | ||
Ferrous Alloys | Cast Iron, Carbon Steel, Stainless Steel, Alloy Steel | Heat treatment available |
Non-Ferrous Alloys | Aluminum, Copper, Bronze, Brass, Zinc | Various grades available |
Size & Weight | ||
Maximum Dimensions | 60″ × 48″ × 36″ (L×W×H) | Larger sizes possible with sectional molding |
Maximum Weight | 2,000 lbs | Single-piece casting |
Minimum Wall Thickness | 0.125″ | Dependent on material and design |
Tolerances & Finish | ||
Standard Dimensional Tolerance | ±0.03″ | For first 6″ + 0.005″ for each additional inch |
Surface Finish | 125-500 RMS | Surface treatments available |
Production Capabilities | ||
Low Volume | 1-50 pieces | Prototype and short runs |
Medium Volume | 51-500 pieces | Production runs |
High Volume | 501+ pieces | Full-scale production |
Mold & Core Technology | ||
Mold Types | Green Sand, No-Bake, Shell | Selected based on part requirements |
Core Making | Cold Box, Hot Box, Shell | Multiple core assembly available |
Pattern Equipment | Wood, Plastic, Aluminum, 3D Printed | Pattern storage and maintenance |
Quality Assurance | ||
Inspection Methods | CMM, X-Ray, Magnetic Particle, Dye Penetrant | ISO 9001:2015 certified |
Material Testing | Spectrographic Analysis, Mechanical Testing | Full certification available |
Secondary Operations | ||
Heat Treatment | Annealing, Normalizing, Quenching, Tempering | In-house capabilities |
Machining | CNC Milling, Turning, Drilling, Grinding | Finish machining available |
Surface Treatment | Shot Blasting, Painting, Powder Coating | Customizable finishes |
Lead Times | ||
Pattern Production | 2-4 weeks | Dependent on complexity |
Sample Parts | 3-5 weeks | After pattern approval |
Production Runs | 4-8 weeks | Based on quantity and complexity |
Our sand casting equipment
Sand Mixer/Muller: Thoroughly blends sand with binders and additives to create consistent molding material with proper strength and permeability
Molding Machine: Compacts sand around patterns to create molds with uniform density and surface finish
Pattern Equipment: Includes pattern plates, match plates, and cope-and-drag boxes that form the cavity shape for the molten metal
Pouring Equipment: Specialized ladles and crucibles designed to safely transport and pour molten metal into prepared molds
Shakeout Equipment: Vibrating tables or rotary drums that separate castings from the sand after solidification
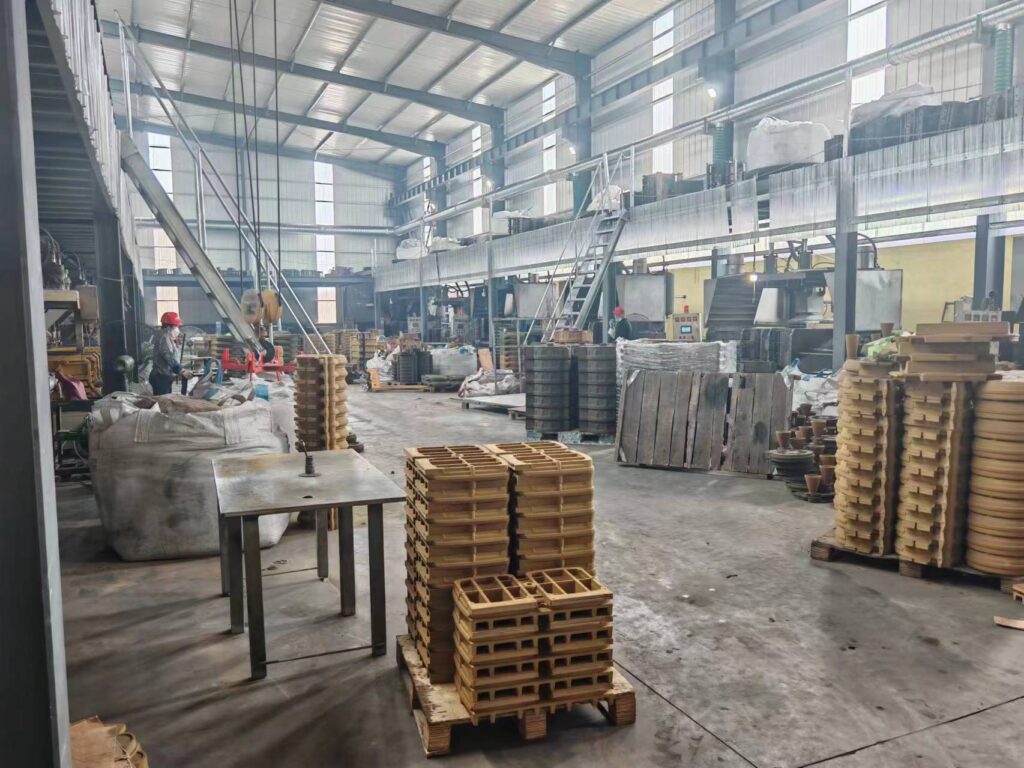
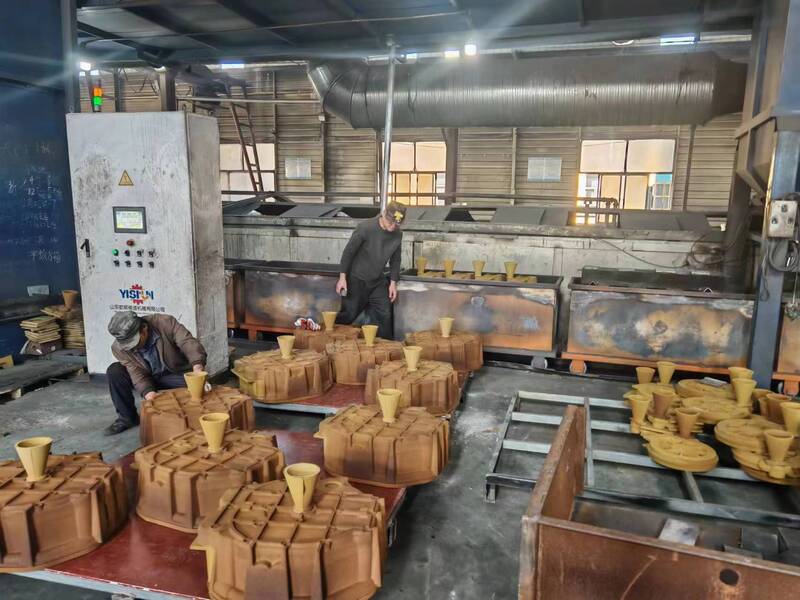
Our Sand Casting Process
Green Sand Casting: Uses a mixture of sand, clay, and water to create molds that can be reused after breaking them apart to remove the casting
Sodium Silicate/CO2 Process: Utilizes sodium silicate binder hardened by carbon dioxide gas to create stronger, more accurate molds than traditional green sand
No-Bake Sand Casting: Employs chemical binders that harden at room temperature, eliminating the need for baking while providing excellent dimensional accuracy
Shell Molding: Creates thin, hard shells using sand coated with thermosetting resin that’s applied to heated metal patterns, resulting in smooth castings with tight tolerances
Lost Foam Casting: Uses evaporative foam patterns embedded in sand that vaporize when molten metal is poured, creating complex shapes with minimal draft angles
Our sand casting materials
Aluminum alloys: These are among the most popular for sand casting due to their low melting point (around 660°C/1220°F), good fluidity, and excellent corrosion resistance.
Copper alloys: Including brass and bronze, these offer good corrosion resistance and electrical conductivity. Bronze is particularly notable for its wear resistance and low friction properties.
Cast iron: Available in several forms including gray iron, ductile iron, and white iron. Cast iron has excellent wear resistance, good machinability, and vibration damping properties.
Steel: Carbon steel and various alloy steels can be sand cast for applications requiring high strength. However, they require higher casting temperatures (around 1370-1430°C/2500-2600°F).
Zinc alloys: These have very low melting points (around 385°C/725°F) and excellent fluidity, making them ideal for detailed castings with thin sections.
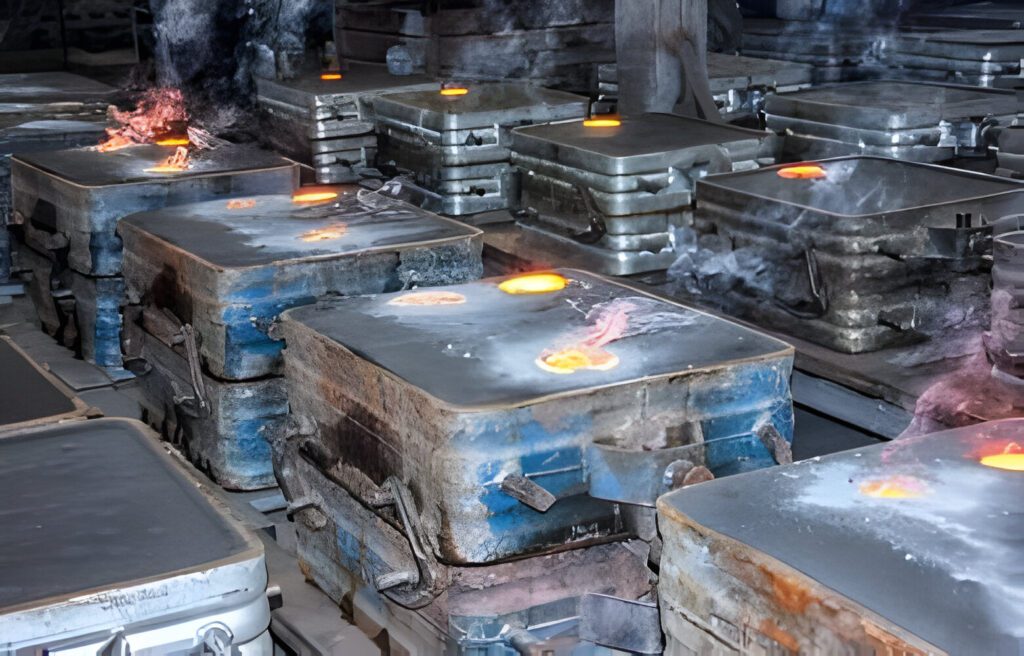
Sand Casting Process
Step 1: Pattern Making
A pattern is created, typically from wood, plastic, or metal, which is a replica of the final casting but slightly larger to account for metal shrinkage during cooling. The pattern may be split into multiple pieces to facilitate removal from the sand mold.
Step 2: Core Making
If the casting requires hollow sections or internal cavities, cores are made from specially treated sand that can withstand the high temperatures of molten metal. These cores are positioned inside the mold to create these internal spaces.
Step 3: Mold Preparation
The pattern is placed in a box called a flask, and special sand mixed with bonding agents is packed tightly around it. The sand is then compacted using pressure or vibration to ensure it holds its shape. Once compacted, the pattern is carefully removed, leaving a cavity in the sand that matches the shape of the desired part.
Step 4: Melting the Metal
The chosen metal (such as iron, steel, aluminum, or bronze) is heated in a furnace until it reaches its melting point and becomes completely liquid. The temperature must be carefully controlled to ensure proper flow characteristics.
Step 5: Pouring
The molten metal is transferred from the furnace to a ladle and then carefully poured into the mold cavity through channels called gates and runners. Proper pouring technique is critical to avoid turbulence and gas entrapment.
Step 6: Cooling and Solidification
After pouring, the metal is allowed to cool and solidify within the mold. The cooling rate affects the microstructure and properties of the final casting, so this step may be controlled through various techniques.
Step 7: Shakeout
Once the metal has completely solidified, the sand mold is broken away from the casting in a process called “shakeout” or “knockout.” The sand can often be reclaimed, reconditioned, and reused for future castings.
Step 8: Finishing
The raw casting undergoes cleaning and finishing operations, including removal of gates and runners, sand blasting, grinding, and machining to achieve the final dimensions and surface finish. Quality inspection is performed to ensure the casting meets all specifications.
Sand Casting benefits
Cost-effectiveness – Sand casting offers economical production, especially for low to medium volume manufacturing, with minimal initial investment compared to other casting methods.
Size versatility – This process can accommodate both very small parts and extremely large components weighing several tons, with virtually no size limitations.
Material flexibility – Nearly any metal alloy can be sand cast, including iron, steel, bronze, aluminum, and brass, making it suitable for diverse applications.
Complex geometry capability – Sand molds can create intricate shapes and internal cavities that would be difficult or impossible with other manufacturing methods.
Rapid prototyping potential – The relatively simple tooling and quick mold creation process makes sand casting ideal for prototyping and iterative design development.
Sand Casting applications
Engine Blocks – Automotive engine blocks are commonly manufactured using sand casting due to their complex internal geometries and cooling passages. Cast iron and aluminum engine blocks both rely on sand casting techniques.
Manhole Covers – These durable street fixtures are typically sand cast from gray iron, which provides excellent wear resistance and compressive strength for withstanding heavy traffic loads.
Large Bronze Sculptures – Artists use sand casting to create monumental bronze sculptures and statues, where the process can capture intricate details while handling the large scale required.
Pump Housings – Industrial pump components benefit from sand casting’s ability to create complex internal fluid passages and chambers that would be difficult to machine otherwise.
Bell Manufacturing – Traditional bells for churches and monuments are sand cast from bronze alloys, as the process helps achieve the specific shape and material properties needed for the desired acoustics.