custom Aluminum Investment Casting service
Premier Aluminum Investment Casting specialists delivering precision-engineered components with superior surface finish, tight tolerances, and exceptional metallurgical integrity since 2003. ISO 9001 certified excellence.
Why work with a Aluminum Investment casting company like us
Customized solutions
24/7 customer service
Product Inspection
Fast delivery
what is Aluminum Investment Casting
Aluminum investment casting (also known as lost-wax casting) is a precision manufacturing process used to create complex metal components with excellent dimensional accuracy, smooth surfaces, and intricate details. This process is particularly valuable for producing aluminum parts that would be difficult or impossible to manufacture using other methods.
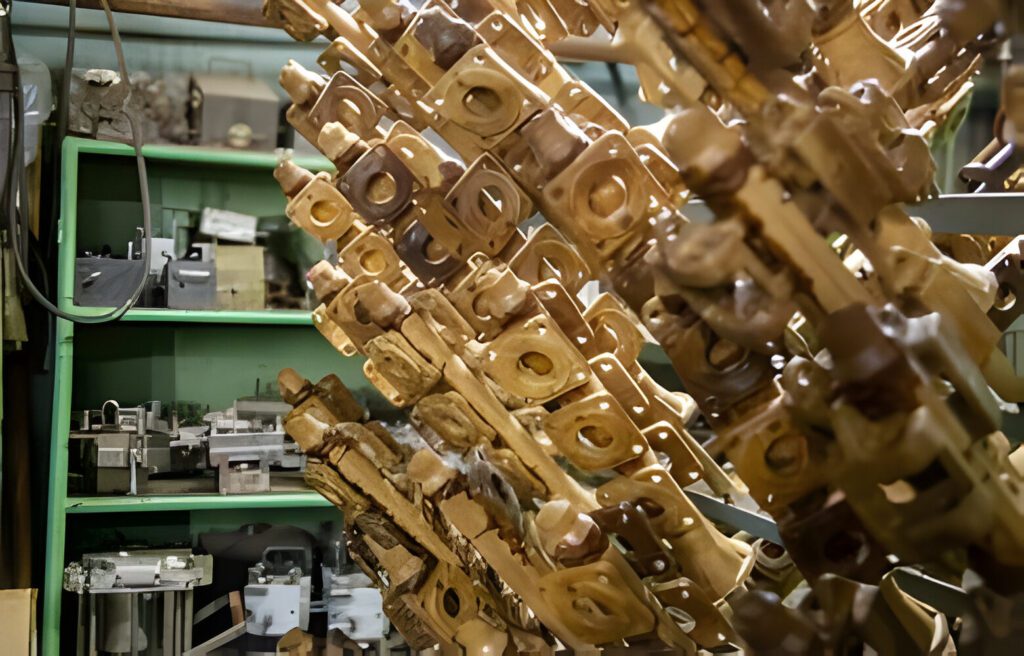
Our Aluminum Investment Casting Capabilities
Capability Category | Specifications | Details |
---|---|---|
Size Range | Minimum Size | 0.5 oz (14g) parts |
Maximum Size | Up to 25 lbs (11.3 kg) single pieces | |
Wall Thickness | Minimum 0.060″ (1.5mm) | |
Dimensional Tolerances | Standard | ±0.005″ for first inch, ±0.002″ for each additional inch |
Precision Grade | ±0.003″ for first inch, ±0.001″ for each additional inch | |
Aluminum Alloys | A356 (AlSi7Mg) | Excellent fluidity, good strength, heat treatable |
A357 (AlSi7Mg0.6) | Higher strength than A356, aerospace applications | |
319 (AlSi5Cu3) | Good mechanical properties at elevated temperatures | |
355 (AlSi5Cu1Mg) | Excellent pressure tightness, high strength | |
713 (AlZn8Cu) | High strength, good machinability | |
Surface Finish | As-Cast | 125-150 RMS |
After Finishing | Down to 63 RMS | |
Heat Treatment | T6 | Solution heat treatment plus artificial aging |
T4 | Solution heat treated and naturally aged | |
T5 | Artificially aged only | |
Manufacturing Capacity | Annual Production | 500,000+ castings per year |
Batch Sizes | 25 to 10,000+ units | |
Lead Time | 4-6 weeks for new projects, 2-3 weeks for repeat orders | |
Quality Assurance | Inspection Methods | CMM, X-ray, Dye Penetrant, Metallurgical Analysis |
Documentation | First Article Inspection Reports, Material Certifications | |
Testing | Tensile Testing, Hardness Testing, Chemical Analysis | |
Certifications | Quality | ISO 9001:2015 |
Industry Specific | AS9100D (Aerospace), IATF 16949 (Automotive) | |
Environmental | ISO 14001 | |
Secondary Operations | In-House | CNC Machining, Surface Finishing, Heat Treatment |
Finishing Options | Anodizing, Powder Coating, Painting, Polishing |
Our Aluminum Investment Casting Heat Treatments
T2 Heat Treatment: A process that involves cooling from an elevated temperature shaping process and artificially aging. Creates good balance of strength and ductility in aluminum castings.
T4 Heat Treatment: Solution heat treatment followed by natural aging to a substantially stable condition. Provides increased strength without artificial aging.
T5 Heat Treatment: Cooling from an elevated temperature shaping process then artificial aging. Improves dimensional stability and mechanical properties.
T6 Heat Treatment: Solution heat treatment followed by artificial aging. Produces maximum strength and hardness properties in aluminum castings.
T51 Heat Treatment: Stress relief by stretching. Reduces internal stresses with minimal precipitation hardening.
T61 Heat Treatment: Solution heat treated and artificially aged by special process. Used for components requiring maximum strength with good ductility.
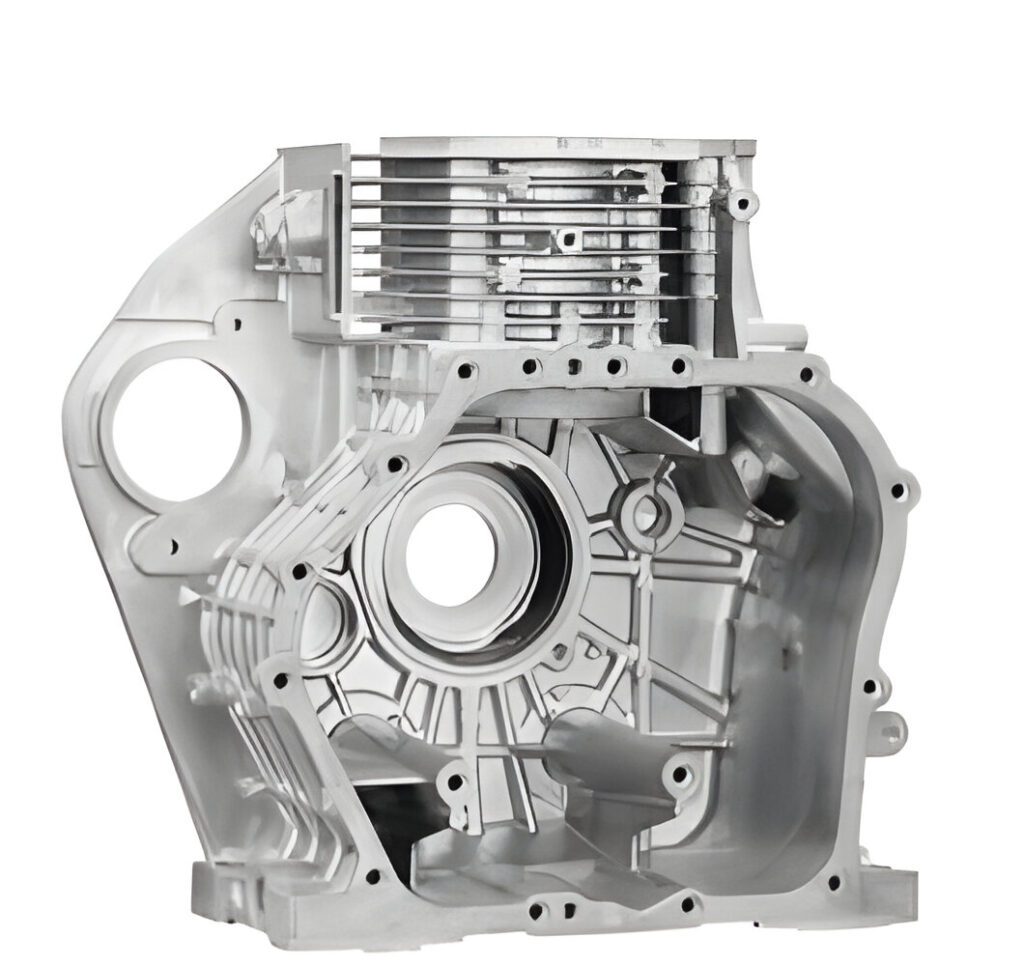
Aluminum Investment Casting Alloys Specifications
Alloy | Composition (%) | Tensile Strength (MPa) | Yield Strength (MPa) | Elongation (%) | Density (g/cm³) | Melting Range (°C) | Common Applications |
---|---|---|---|---|---|---|---|
A356 | Si: 6.5-7.5, Mg: 0.3-0.45, Fe: <0.2 | 230-280 | 160-185 | 3-5 | 2.68 | 557-613 | Aerospace components, automotive parts |
A357 | Si: 6.5-7.5, Mg: 0.5-0.7, Fe: <0.15 | 275-320 | 205-240 | 3-5 | 2.68 | 557-613 | High-strength aerospace, military applications |
713 | Cu: 7.5-8.5, Fe: <1.0, Zn: <0.4 | 275-295 | 185-205 | 3-4 | 2.81 | 548-646 | Pump housings, impellers, valve bodies |
355 | Si: 4.5-5.5, Cu: 1.0-1.5, Mg: 0.4-0.6 | 241-275 | 165-193 | 2-4 | 2.71 | 577-632 | Aircraft fittings, gears, engine components |
C355 | Si: 4.5-5.5, Cu: 1.0-1.5, Mg: 0.4-0.6 | 262-290 | 179-207 | 3-5 | 2.71 | 577-632 | Premium industrial applications, critical parts |
201 | Cu: 4.0-5.0, Ag: 0.4-0.8, Mg: 0.15-0.55 | 435-480 | 380-415 | 5-7 | 2.80 | 548-635 | High-performance aerospace, racing components |
206 | Cu: 4.0-5.0, Mg: 0.15-0.35, Mn: 0.2-0.5 | 400-427 | 310-345 | 5-7 | 2.80 | 548-640 | Aircraft components, military hardware |
238 | Cu: 3.5-4.5, Mg: 0.7-1.3, Si: <0.25 | 310-350 | 205-240 | 5-8 | 2.78 | 543-630 | High-temperature applications, pistons |
319 | Si: 5.5-6.5, Cu: 3.0-4.0, Fe: <1.0 | 185-250 | 125-165 | 2-3 | 2.79 | 532-621 | General purpose castings, engine blocks |
B390 | Si: 16-18, Cu: 4.0-5.0, Mg: 0.5-0.7 | 280-310 | 240-275 | <1 | 2.73 | 510-585 | Wear-resistant applications, engine components |
Aluminum Investment Casting Processing Parameters
Parameter | Range | Notes |
---|---|---|
Pouring Temperature | 675-775°C | Varies by alloy and part complexity |
Mold Temperature | 150-500°C | Higher for thin sections |
Shell Thickness | 5-10 mm | Thicker for larger parts |
Dewaxing Temperature | 150-180°C | Autoclave pressure: 550-700 kPa |
Burnout Temperature | 900-1100°C | Complete ceramic sintering |
Typical Tolerances | ±0.13 mm for first 25 mm | Add ±0.04 mm per additional 25 mm |