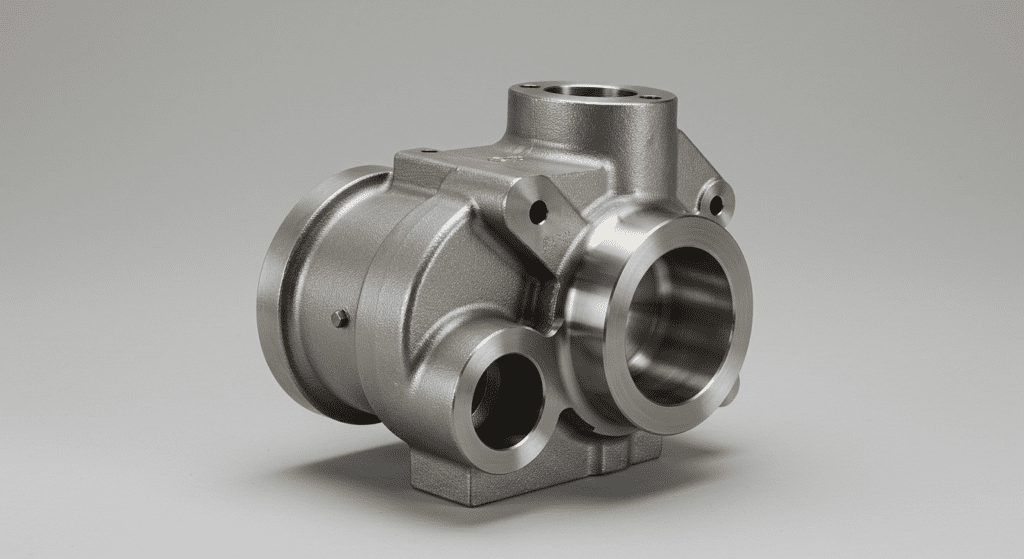
TL;DR
Investment casting produces precise stainless steel parts with excellent surface finish by creating a wax pattern, coating it with ceramic, melting out the wax, and pouring in molten steel. The five main types used in this process are austenitic (corrosion-resistant), ferritic (moderate cost), martensitic (hardenable), duplex (combined properties), and precipitation-hardened (strength plus corrosion resistance), each containing different proportions of elements like chromium, nickel, and molybdenum to suit specific applications.
What Is Stainless Steel Investment Cast
Investment cast stainless steel refers to stainless steel parts made through the investment casting process. This method involves creating a wax pattern of the desired part, coating it with ceramic material, melting out the wax, and then pouring molten stainless steel into the resulting cavity. Once the metal cools and solidifies, the ceramic shell is broken away to reveal the final part.
Types of Stainless Steel in Investment Cast
There are five main types of stainless steel used in investment casting.
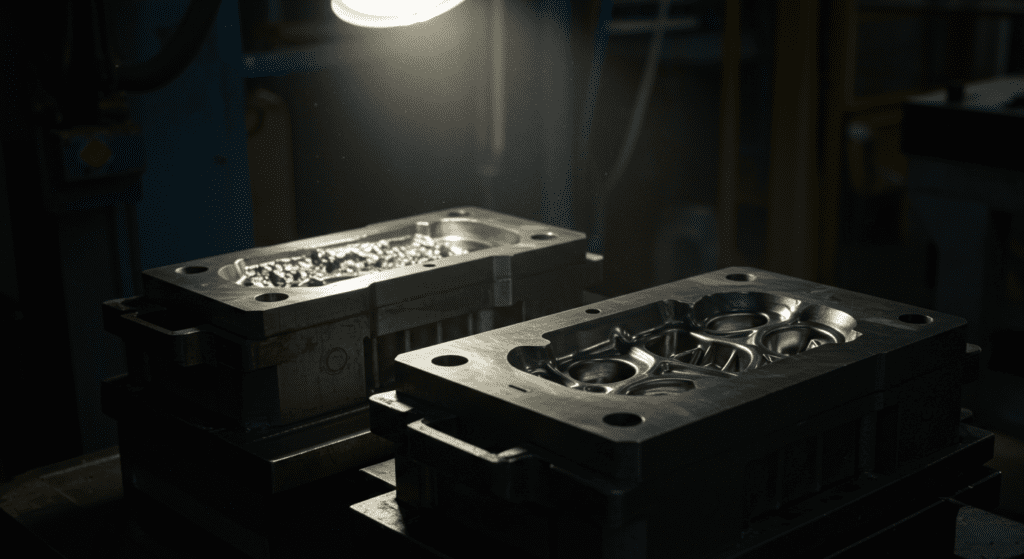
Austenitic Stainless Steels
These steels, including the 200-series and the widely used 300-series (e.g., 304, 316), possess a face-centered cubic (FCC) crystal structure. They are generally non-magnetic in the annealed condition, though some may become slightly magnetic after cold working.
Austenitic grades are renowned for their excellent corrosion resistance, good formability and weldability, and commendable strength at both ambient and elevated temperatures.
Ferritic Stainless Steels
Characterized by a body-centered cubic (BCC) crystal structure, these steels (e.g., 400-series like 409, 430) are magnetic. They offer good corrosion resistance, particularly against stress corrosion cracking, and moderate strength. However, their formability and weldability are generally inferior to austenitic grades.
Martensitic Stainless Steels
These grades (e.g., 400-series like 410, 420) can achieve high strength and hardness through heat treatment (quenching and tempering), which transforms their microstructure to body-centered tetragonal (BCT). They are magnetic and offer moderate corrosion resistance, which is typically lower than that of austenitic or ferritic grades.
Duplex Stainless Steels
As their name suggests, these steels (e.g., 2205, 2507) have a mixed microstructure of austenite and ferrite, typically in roughly equal proportions. This combination results in higher strength than common austenitic grades and excellent resistance to pitting, crevice corrosion, and stress corrosion cracking, particularly in chloride-rich environments.
Precipitation-Hardened (PH) Stainless Steels
These alloys (e.g., 17-4 PH, 15-5 PH) can be strengthened by a precipitation hardening heat treatment, achieving very high tensile and yield strengths while maintaining good corrosion resistance, superior to that of martensitic grades.
Alloying Elements and Their Impact
- Chromium (Cr): Provides basic corrosion resistance by forming a protective oxide layer. Stainless steels must contain at least 10.5% chromium to be considered “stainless.”
- Nickel (Ni): Improves formability and helps create the austenitic structure. It enhances resistance to acids and alkaline solutions. It is a key constituent in austenitic (e.g., 300-series) and duplex stainless steels.
- Molybdenum (Mo): Boosts resistance to pitting and crevice corrosion, especially in chloride-containing environments like seawater. It is a critical addition in grades like 316/CF8M and many duplex stainless steels.
- Carbon (C): Increases hardness and strength but can reduce corrosion resistance if present in high amounts.
- Nitrogen (N): Acts like nickel in stabilizing austenite while also improving strength and pitting resistance.
- Manganese (Mn) and Silicon (Si): These elements are primarily used as deoxidizers during melting and can influence the fluidity of the molten metal. Manganese can also substitute for some nickel in certain austenitic grades (e.g., 200-series) to stabilize austenite and increase strength.
Common Stainless Steel Grades Used in Investment Casting
Cast Grade | Wrought Equivalent | Key Alloying Elements (Typical %) | Min. Tensile Strength (ksi/MPa) | Min. Yield Strength (ksi/MPa) | Min. Elongation (%) | Hardness (HB, typical) | Key Characteristics/Applications | ASTM Spec. (Typical) |
---|---|---|---|---|---|---|---|---|
CF8 | 304 | Cr: 18-21, Ni: 8-11, C: 0.08 | 70 / 485 | 30 / 205 | 35 | 163 | General corrosion resistance, good castability; pumps, valves, food processing. | A351, A743 |
CF3 | 304L | Cr: 17-21, Ni: 8-12, C: 0.03 | 70 / 485 | 30 / 205 | 35 | ~160 | Low carbon for weldability, resists sensitization; welded components, corrosive environments. | A351, A743 |
CF8M | 316 | Cr: 18-21, Ni: 9-12, Mo: 2-3, C: 0.08 | 70 / 485 | 30 / 205 | 30 | 179 | Enhanced pitting/crevice corrosion resistance (Mo); marine, chemical, pharmaceutical. | A351, A743 |
CF3M | 316L | Cr: 17-21, Ni: 9-13, Mo: 2-3, C: 0.03 | 70 / 485 | 30 / 205 | 30 | ~170 | Low carbon version of CF8M for weldability; severe corrosive environments, welded parts. | A351, A743 |
CN7M | Alloy 20 | Cr: 19-22, Ni: 27.5-30.5, Mo: 2-3, Cu: 3-4, C: 0.07 | 62 / 425 | 28 / 195 | 35 | ~150 | Excellent resistance to hot sulfuric acid and other aggressive media; chemical processing. | A351, A743 |
CB7Cu-1 | 17-4 PH | Cr: 15.5-17.5, Ni: 3-5, Cu: 3-5, C: 0.07 | 100-180 / 690-1240 (Heat Treated) | 75-170 / 515-1170 (Heat Treated) | 6-16 (Heat Treated) | ~300-400 (Heat Treated) | High strength, good corrosion resistance; aerospace, nuclear, marine components. | A747 |
CD3MN | 2205 Duplex | Cr: 21-23.5, Ni: 4.5-6.5, Mo: 2.5-3.5, N: 0.1-0.3, C: 0.03 | 90 / 620 | 60 / 415 | 25 | ~230 | High strength, excellent resistance to SCC, pitting, and crevice corrosion; offshore, desalination. | A890 |
Austenitic Grades
- CF8 (Similar to 304): The workhorse of austenitic grades with 18-20% chromium and 8-11% nickel.
- CF3 (Similar to 304L): A low-carbon version of CF8 that reduces the risk of carbide precipitation and improves weldability.
- CF8M (Similar to 316): Contains molybdenum for better corrosion resistance, especially against chlorides.
- CF3M (Similar to 316L): Low-carbon version of CF8M with improved weldability and resistance to intergranular corrosion.
- CN7M (Alloy 20): Highly alloyed austenitic grade with exceptional resistance to sulfuric acid.
- CK20 (Similar to 310): High-chromium, high-nickel content for excellent heat and oxidation resistance at temperatures up to 2100°F.
Precipitation-Hardened (PH) Grades
- CB7Cu-1 (Similar to 17-4 PH): Contains copper precipitates that form during aging heat treatment. Offers high strength with good corrosion resistance.
Duplex Grades
- CD3MN (Similar to 2205): The most common duplex grade with roughly 22% chromium, 5% nickel, and 3% molybdenum. Provides excellent resistance to stress corrosion cracking and pitting.