Investment casting costs are influenced by several key factors including materials, tooling, production volume, part design complexity, labor, post-processing requirements, and quality assurance measures. Material selection typically accounts for 15-30% of costs, while tooling represents a significant upfront investment that becomes less impactful with higher volumes. Understanding these cost drivers helps manufacturers optimize designs and production processes to achieve the best balance of quality and affordability for investment cast parts.
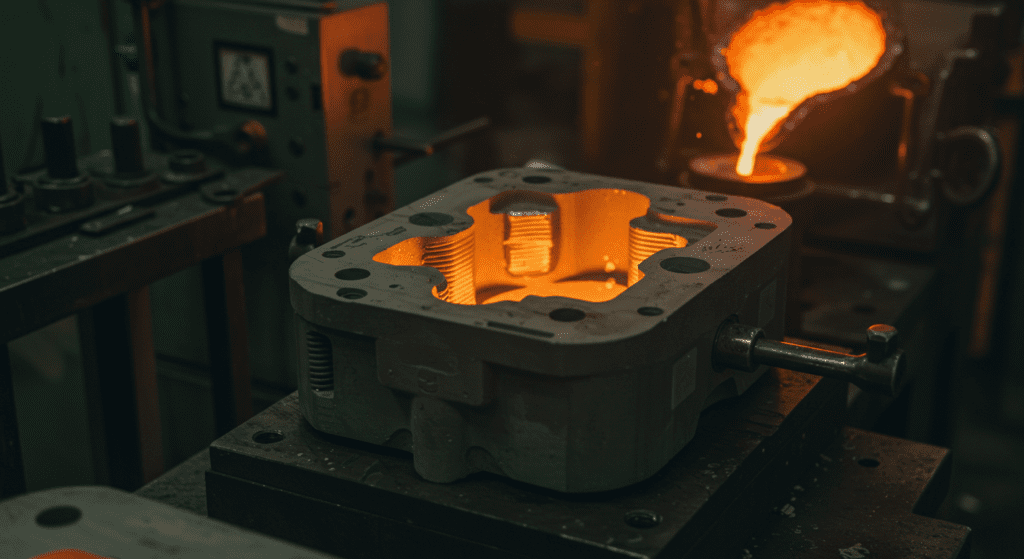
Influencers of Investment Casting Costs
1.Material Costs
Investment casting can accommodate a vast range of materials, from common carbon and stainless steels to specialized aluminum, nickel-based, cobalt-based, and titanium alloys. The cost varies widely among these options.
The amount of molten metal needed to produce a part is always greater than the volume of the finished component itself, due to material used in sprues, runners, gates, and potential scrap. Industry analyses suggest that direct material procurement can account for 30-40% of total production expenses.
2.Tooling Costs
Tooling, primarily the wax injection die used to create the wax patterns, represents a major upfront cost in investment casting. The cost of this tooling can range significantly, typically from $2,000 to over $20,000.
- Number of Cavities: More cavities in a die let you cast multiple parts at once, increasing upfront costs but lowering per-part costs for large production runs. Single cavity tools cost less initially but make each part more expensive.
- Cores: Complex internal features need cores that add to tooling costs.
- Die Material: Wax injection dies are commonly machined from aluminum.
3.Production Volume
How many parts you need greatly impacts the unit cost. Higher volumes spread fixed costs like tooling, setup, and programming across more parts, making each one cheaper. For very large orders, material and labor become the main cost factors.
Small production runs have higher per-part costs since tooling expenses can’t be distributed across many units. For less than 100 pieces, other manufacturing methods might be cheaper than investment casting.
4.Part Design and Complexity
The design characteristics of the component itself—its size, geometric complexity, specified tolerances, and required surface finish—are fundamental drivers of investment casting costs.
- Part Size: Bigger parts need more material and energy to cast, increasing costs accordingly.
- Part Complexity: More complex designs necessitate more sophisticated and expensive wax injection dies, potentially requiring multiple moving parts or intricate core arrangements. Complex geometries can also lead to more challenging wax pattern assembly, more delicate ceramic shell construction, and potentially lower casting yields due to difficulties in ensuring complete and defect-free metal flow.
- Tolerances: Demanding tighter tolerances than standardly achievable requires more precise tooling, meticulous process control at every stage (wax injection, shell building, metal pouring, cooling), and may necessitate additional inspection steps or even secondary machining operations, all of which add to the cost.
- Surface Finish: Better surface finishes require more processing time and post-casting processes like polishing or specialized blasting may be necessary, incurring further costs.
5.Labor and Operational Costs
Labor costs constitute a significant portion of the total expense in investment casting, often estimated at around 30% of the total cost , due to the multi-step and often manually intensive nature of the process. From wax pattern injection and assembly to ceramic shell building, de-waxing, metal pouring, shell removal, and finishing, many stages require skilled human intervention.
Energy consumption involves energy-intensive equipment such as furnaces for melting metal and preheating ceramic shells, autoclaves for de-waxing, and ovens or controlled environments for drying ceramic layers. The melting process alone can account for an average of 55% of the total energy consumed in an investment casting facility, with mold making and processing contributing around 20%, and post-casting processes another 7%.
6.Post-Casting Processes
After casting, additional operations are often needed to finish a part. These secondary operations can include:
- Gate and Riser Removal: This is a standard finishing step where the cast parts are separated from the gating system, typically by sawing or grinding.
- Grinding and Finishing: Minor imperfections, parting line witnesses (if any, though investment casting aims to minimize these), or surface irregularities may require grinding or other finishing techniques to meet cosmetic or functional specifications.
- Machining: Although investment casting significantly reduces the need for machining compared to other processes like sand casting , some machining may still be required if extremely tight tolerances (beyond as-cast capabilities), specific surface finishes, or features that cannot be directly cast (e.g., very small, deep holes or threaded features) are specified.
- Heat Treatment: Many investment castings undergo heat treatment processes such as annealing (to improve machinability), hardening (to increase strength and wear resistance), or stress relieving (to ensure dimensional stability).
- Surface Treatments and Coatings: Depending on the application, parts may require surface treatments like polishing, plating (e.g., for corrosion resistance or appearance), or painting, each incurring additional costs.
7.Quality Assurance
Quality control measures add necessary costs to ensure parts meet specifications. Standard inspections include visual checks, measuring dimensions, and basic non-destructive testing. These quality steps typically add 5-10% to casting costs but prevent costly failures in your application.
Stricter requirements like magnetic particle inspection (for ferrous materials), liquid penetrant inspection (to detect surface-breaking defects), and radiographic inspection (X-ray, to identify internal voids or inclusions) add significant expense.