The main difference between investment casting and injection molding is that investment casting creates metal parts using a wax pattern and molten metal, while injection molding forms plastic parts by injecting molten plastic into a mold. Investment casting suits complex metal components; injection molding excels in high-volume plastic production.
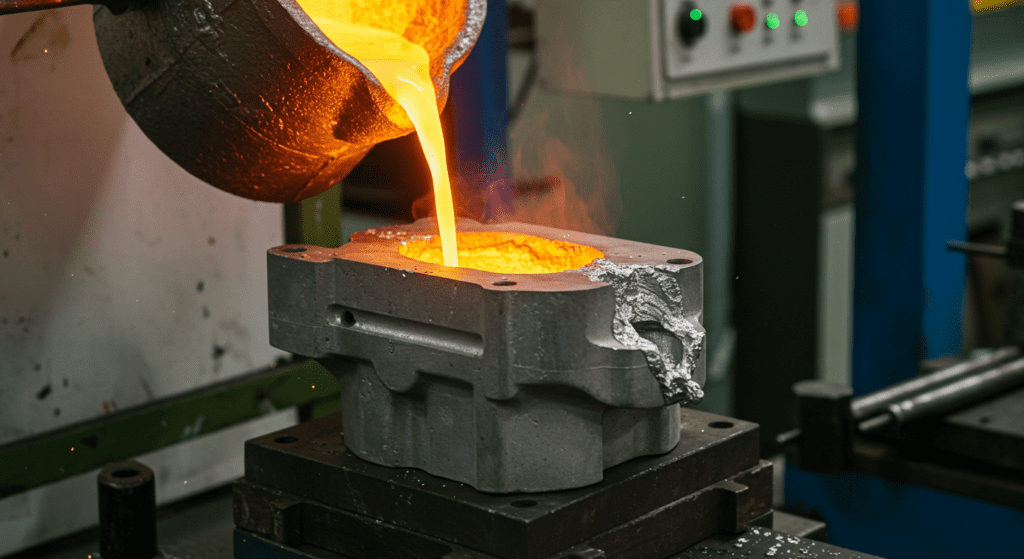
Investment Casting
Investment casting is a metal forming process that creates precise metal parts by pouring molten metal into ceramic molds. The process uses a wax pattern covered in ceramic material to form the mold. Manufacturers use this method to produce complex shapes with excellent surface finishes and tight tolerances.
Step-by-Step Investment Casting Process
- Create the wax pattern: Workers inject wax into a metal die to form an exact replica of the desired part. Multiple patterns attach to a central wax sprue to create a tree-like assembly.
- Build the ceramic shell: The wax assembly gets dipped into ceramic slurry, then coated with sand particles. This coating process repeats 5-10 times until the shell reaches the required thickness.
- Remove the wax: The ceramic shell goes into an autoclave or furnace at 200-375°F. The heat melts out the wax, leaving a hollow ceramic mold.
- Fire the mold: The empty ceramic shell heats to 1,800-2,000°F. This step removes any remaining wax residue and strengthens the ceramic.
- Pour the metal: Workers melt the chosen metal and pour it into the hot ceramic mold. Gravity or vacuum assistance helps the metal fill all cavity details.
- Break out the casting: After cooling, workers break away the ceramic shell using hammers or water jets. The metal parts separate from the sprue system.
- Finish the part: Final operations include grinding, machining, and heat treating to meet specifications.
Injection Molding
Injection molding forces molten material into a steel mold under high pressure. The process creates identical parts at speeds of 15-120 seconds per cycle. Two main types exist: plastic injection molding and metal injection molding (MIM).
- Plastic injection molding produces parts from thermoplastic and thermoset polymers.
- Metal injection molding combines fine metal powders with plastic binders to create a feedstock.
Step-by-Step Injection Molding Process
Plastic Injection Molding
- Load plastic pellets – Fill the hopper with plastic resin pellets. Automated systems feed 50-500 pounds per hour into the machine.
- Melt the plastic – The screw rotates and pushes pellets through a heated barrel at 300-600°F. Complete melting takes 10-30 seconds.
- Inject into mold – Ram the molten plastic into the closed steel mold at 10,000-20,000 psi. Injection fills the mold in 1-5 seconds.
- Cool the part – Circulate coolant through mold channels at 50-150°F. Cooling takes 10-60 seconds depending on wall thickness.
- Open and eject – Separate the mold halves and push out the finished part with ejector pins. The cycle then repeats.
Metal Injection Molding
- Mix feedstock – Blend metal powder (2-20 microns) with polymer binders at a 60:40 ratio. Mix for 2-4 hours at 300-400°F.
- Inject the feedstock – Load feedstock pellets and inject into the mold at 200-400°F. Pressure reaches 15,000-25,000 psi.
- Remove from mold – Cool for 20-40 seconds and eject the “green” part containing metal and binder.
- Debind the part – Dissolve or burn out 90% of the binder using solvents or heat. This creates a porous “brown” part over 12-48 hours.
- Sinter the metal – Heat to 2,000-2,500°F in a controlled atmosphere furnace. Metal particles fuse together, shrinking the part by 15-20% over 8-24 hours.
- Finish as needed – Perform secondary operations like machining, plating, or heat treating to meet specifications.
Investment Casting Vs Injection Molding
Characteristic | Investment Casting | Plastic Injection Molding | Metal Injection Molding (MIM) |
---|---|---|---|
Core Principle | Expendable (single-use) ceramic mold created from a wax pattern. | Reusable, high-precision steel or aluminum mold. | Reusable steel mold with post-molding debinding and sintering steps. |
Primary Materials | Ferrous and non-ferrous alloys: stainless steel, aluminum, carbon steel, superalloys. | Thermoplastics (ABS, PC, PP, PE, Nylon), thermosets, elastomers. | Powdered metal feedstock: stainless steel, tool steel, titanium, cobalt alloys. |
Typical Production Volume | Low to Medium: 10s to 10,000s of parts. | High to Very High: 10,000s to millions of parts. | Medium to High: 10,000s to millions of parts. |
Tooling Cost | Low to Medium: Master die for wax patterns is less expensive. | Very High: Hardened steel molds can cost over $100,000. | High: Precision steel molds required, but smaller than many plastic molds. |
Per-Unit Cost | High to Medium: Driven by labor and long cycle times. | Very Low: Benefits from automation, fast cycles, and cheap materials. | Low: Higher material cost than casting, but automated for high volume. |
Geometric Complexity | Very High: Can produce intricate internal cavities with cores; no parting lines. | High: Undercuts and complex features require expensive mold actions (sliders, lifters). | Very High: Excels at producing thin walls, sharp features, and intricate details. |
Typical Tolerances | Good: Typically ±0.5 mm, can be improved with secondary operations. | Excellent: Highly repeatable; specific tolerance depends on material and part design. | Excellent: Often ±0.05 mm or tighter, superior to investment casting. |
Surface Finish (Ra) | Very Good: Typically around 3.2 µm (125 Ra microinches). | Excellent: Can be cosmetic/optical grade directly from a polished mold. | Excellent: Typically around 1 µm, often requires no secondary finishing. |
Key Advantage | Unmatched material integrity and design freedom for complex metal parts. | Unbeatable scalability and low unit cost for polymer parts. | High-precision, high-volume production of small, complex metal parts. |