The main difference between expendable mold casting and investment casting is that investment casting is a type of expendable mold casting that uses a ceramic shell built around a wax pattern. All investment casting is expendable, but not all expendable mold casting uses the same detailed, precise process.
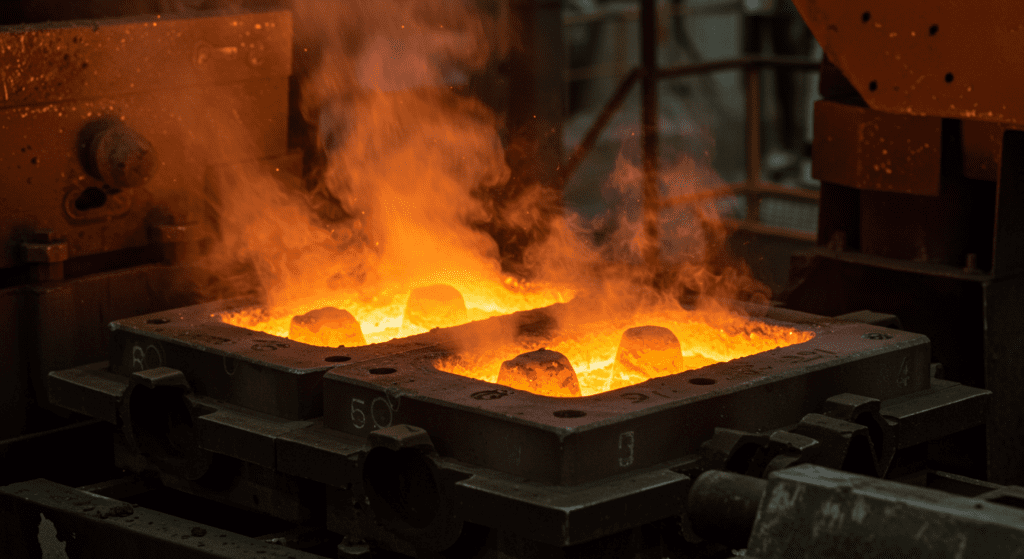
What is Expendable Mold Casting
Expendable mold casting refers to any metal casting process where the mold is destroyed after making each part. The mold gets broken apart to remove the solidified metal, making it impossible to reuse for another casting immediately.
The term “expendable” means the mold serves its purpose once and then becomes waste. After pouring molten metal and letting it cool, manufacturers must break the mold to retrieve the finished part.
How Investment Casting Fits Into Expendable Mold Casting
Investment casting is actually a type of expendable mold casting. The ceramic shell mold used in investment casting breaks away after the metal solidifies, placing it firmly in the expendable category.
The relationship is simple: expendable mold casting is the broad category, and investment casting is one specific method within that category.
Investment casting uses a ceramic mold created around a wax pattern. Once the metal cools, workers crack and remove the ceramic shell, destroying it in the process.
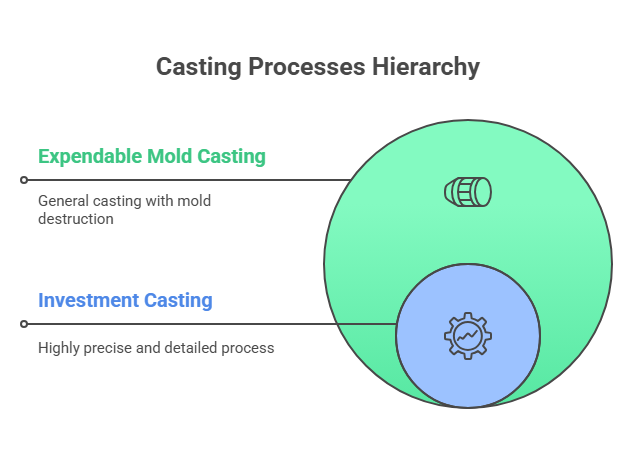
Types of Expendable Mold Casting Processes
There are 5 main types of expendable mold casting processes. Each uses different materials and techniques but shares the common trait of single-use molds.
- Sand Casting: Uses compacted sand mixed with binding agents like clay or polymers. This remains the most widely used casting method due to its low cost and versatility.
- Investment Casting: Creates ceramic molds around wax patterns. The process delivers exceptional detail and smooth surfaces, making it ideal for complex parts.
- Shell Mold Casting: Forms thin shells from resin-bonded sand. The shells provide better surface finish than regular sand casting while maintaining cost efficiency.
- Plaster Casting: Employs gypsum-based molds for non-ferrous metals. The smooth plaster surface creates parts with excellent finish quality.
- Lost Foam Casting: Replaces foam patterns with molten metal. The foam vaporizes on contact, leaving behind the cast part.
Key Differences Between Investment Casting and Other Expendable Methods
Aspect | Investment Casting | Sand Casting | Shell Mold Casting | Plaster Casting | Lost Foam Casting |
---|---|---|---|---|---|
Pattern Material | Wax or plastic (expendable) | Wood, metal, plastic (reusable) | Metal (reusable) | Wood, metal, plastic (reusable) | Polystyrene foam (expendable) |
Mold Material | Ceramic shell (silica, zircon) | Sand with clay binder | Sand with resin binder | Gypsum plaster | Sand (unbonded) |
Surface Finish | Excellent (32-125 μin Ra) | Poor to fair (250-1000 μin Ra) | Good (150-350 μin Ra) | Very good (60-125 μin Ra) | Fair to good (200-400 μin Ra) |
Dimensional Accuracy | ±0.003-0.005 in/in | ±0.010-0.030 in/in | ±0.005-0.010 in/in | ±0.005-0.008 in/in | ±0.008-0.015 in/in |
Part Complexity | Very complex, intricate details | Simple to moderate | Moderate complexity | Complex with fine details | Complex, hollow sections possible |
Wall Thickness | 0.025-0.25 in (very thin) | 0.125-1.0 in minimum | 0.125-0.5 in | 0.06-0.5 in | 0.25-1.0 in |
Size Range | Ounces to 200 lbs | Ounces to tons | 1 oz to 500 lbs | Up to 300 lbs | 1 lb to tons |
Suitable Metals | All metals, especially high-temp alloys | Most metals | Ferrous and non-ferrous | Non-ferrous only (Al, Cu, Mg) | Primarily Al, Fe, steel |
Production Volume | Low to medium | All volumes | Medium to high | Low to medium | Low to medium |
Tooling Cost | Low (wax dies) | Low to moderate | Moderate to high | Low to moderate | Very low |
Process Time | Long (days to weeks) | Short to moderate | Moderate | Moderate | Short |
Draft Requirements | None required | 1-3° required | 1-2° required | Minimal to none | None required |
Porosity Issues | Very low | Moderate to high | Low to moderate | Low | Can be high |
Material Reuse in Expendable Casting
Despite being “expendable,” some mold materials can be reclaimed for future use. Sand from broken molds can be recycled up to 90% after proper treatment.
The sand loses its molded shape during part removal but retains its basic properties. Foundries clean, re-bond, and reform the sand into new molds.
Investment casting offers less material recovery. The ceramic shell shatters during removal, and the fragments have limited reuse potential. However, the wax patterns can be melted and recycled repeatedly.