Non-expendable mold casting uses reusable molds that can produce hundreds or thousands of parts before wearing out. Unlike single-use molds, these durable molds save time and money in high-volume production.
What Is Non-expendable Mold Casting
Non-expendable mold casting is a metal casting process that uses reusable molds to create metal parts. Unlike other casting methods where you break the mold to get the part out, these molds can be used over and over again.
These molds are typically made from strong materials like steel, iron, or graphite. They can withstand temperatures up to 1,200°F (650°C) for aluminum casting and even higher for other metals.
Types of Non-expendable Mold Casting
There are several different types of non-expendable mold casting methods. Each one has its own strengths and works best for different kinds of parts.
Permanent (Gravity Die) Casting
Permanent mold casting uses gravity to fill the mold with molten metal. You simply pour the liquid metal into the top of the mold and let gravity do the work.
This method works great for parts that need smooth surfaces and accurate dimensions. The typical tolerance is about ±0.015 inches (±0.38 mm).
Common parts made this way include engine pistons, gear blanks, and kitchen cookware. The process works especially well with aluminum, copper, and magnesium alloys.
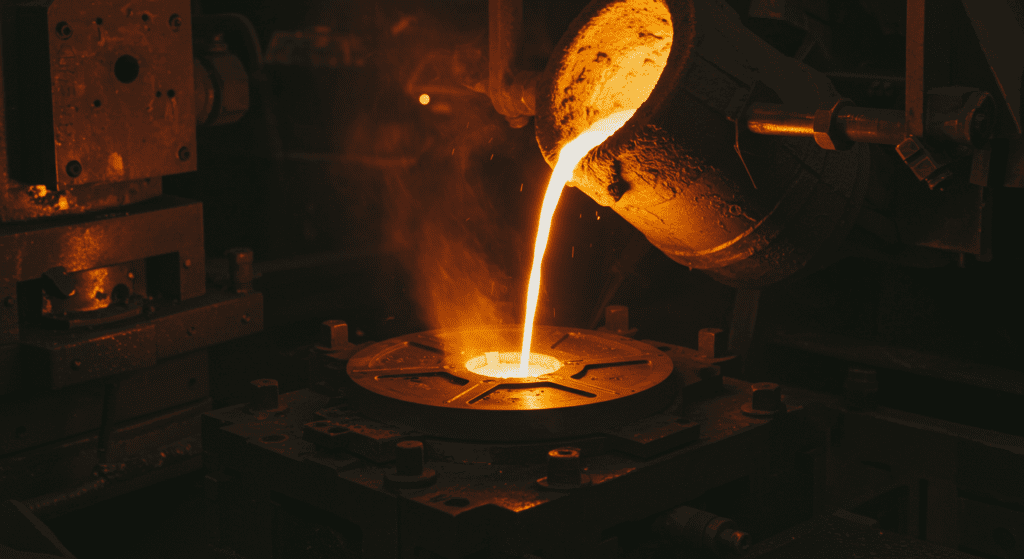
Die Casting
Die casting takes things up a notch by forcing molten metal into the mold under high pressure. This pressure ranges from 1,500 to 25,000 psi (10 to 175 MPa).
There are two main types: hot chamber and cold chamber die casting. Hot chamber works for metals with lower melting points like zinc and lead. Cold chamber handles metals with higher melting points like aluminum and copper.
Die casting creates incredibly detailed parts with wall thicknesses as thin as 0.040 inches (1 mm). It’s perfect for making complex shapes like car engine blocks, power tool housings, and toy cars.
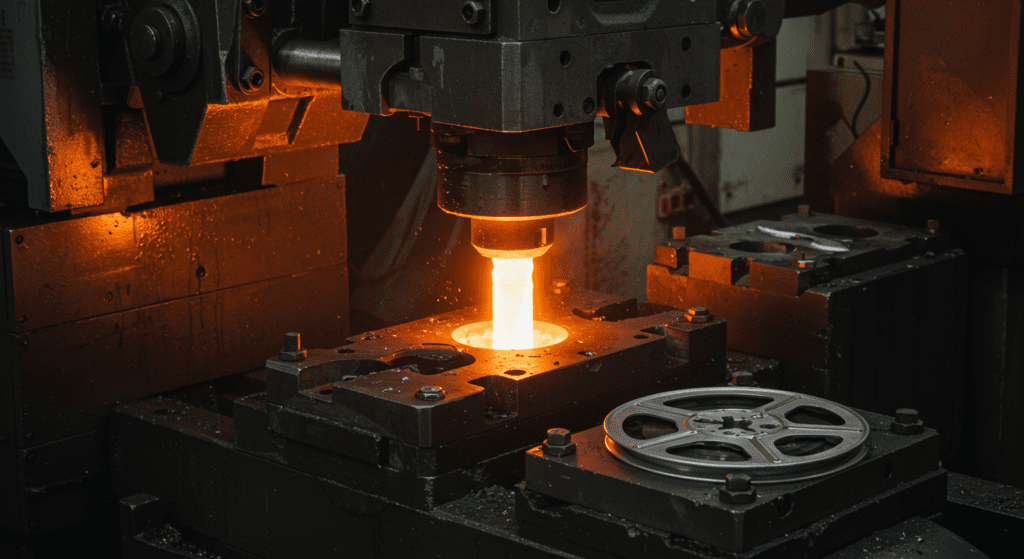
Centrifugal Casting
Centrifugal casting spins the mold while pouring in molten metal. The spinning force pushes the metal against the mold walls, creating hollow cylindrical parts.
This method is perfect for making pipes, tubes, and rings. The spinning action also helps push impurities toward the center, resulting in cleaner, stronger parts on the outside where it matters most.
Typical spinning speeds range from 300 to 3,000 rpm. The faster the spin, the denser and stronger the final part becomes.
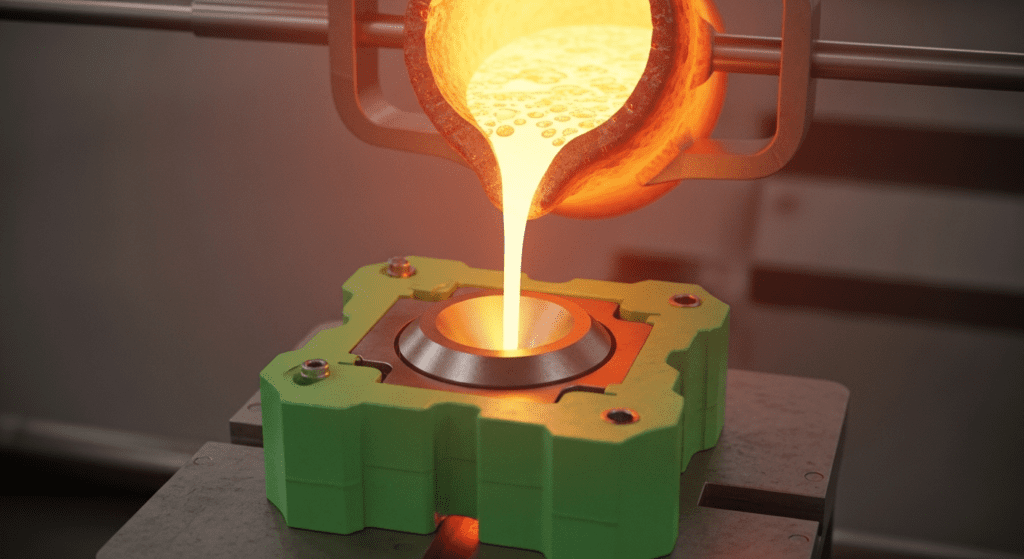
Semi-Solid Metal Casting
Semi-solid metal casting works with metal that’s partially melted, containing 30-65% solid particles. The material flows like thick honey but maintains some solid structure.
This unique state allows for lower forming pressures than die casting. Parts show less porosity and better mechanical properties than traditional castings.
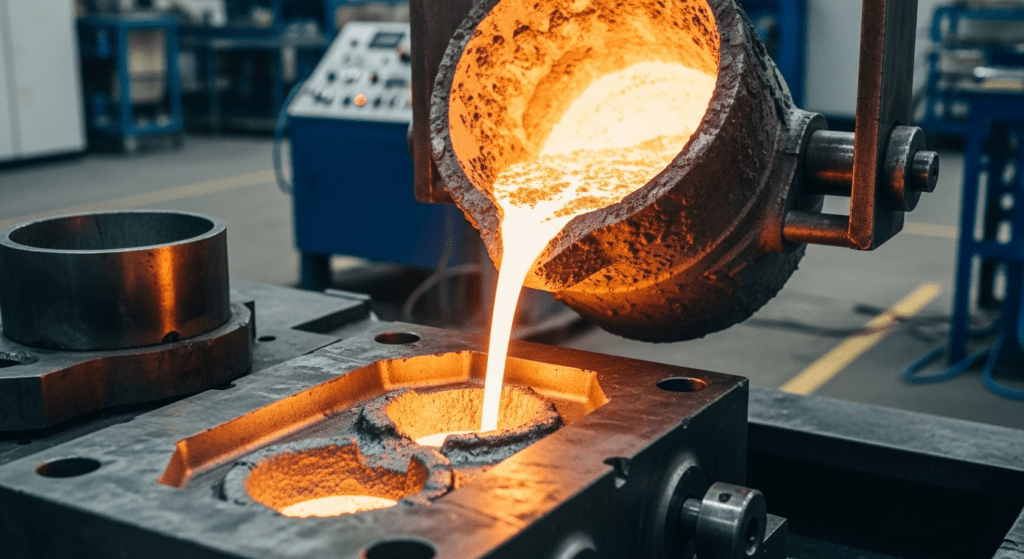
Continuous Casting
Continuous casting creates long products like bars, tubes, and sheets by continuously pouring metal through a mold. The solidified metal exits the bottom while fresh molten metal enters the top.
This process can run for days or even weeks without stopping. Steel mills use it to produce about 96% of the world’s steel – that’s over 1.6 billion tons per year!
The method saves energy and reduces waste compared to older batch processes. It also creates more uniform products with better surface quality.
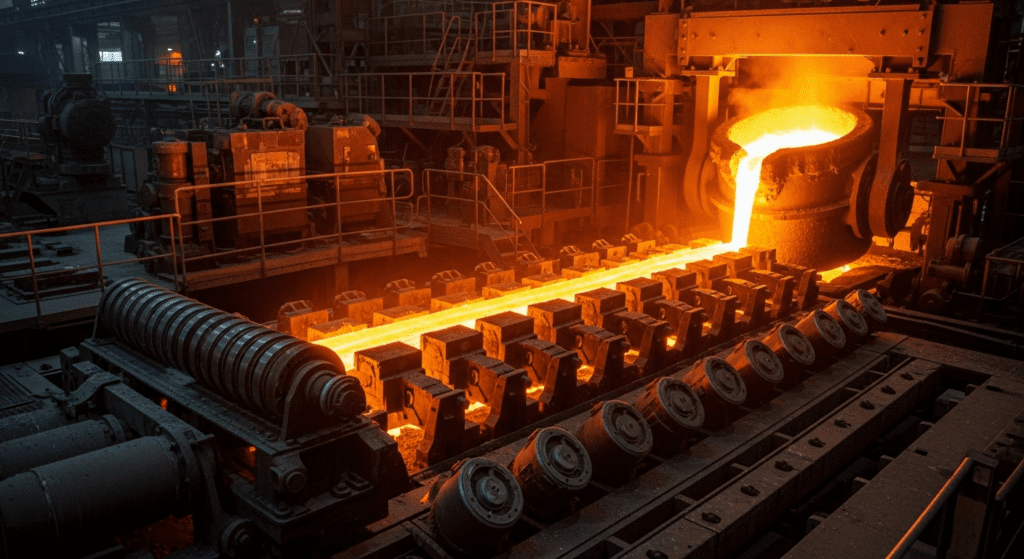
What Is the Difference Between Non-expendable Mold Casting and Expendable Mold Casting
The main difference is simple: non-expendable molds are reusable, while expendable molds are destroyed after each use. It’s like the difference between a silicone baking pan you use repeatedly and a paper cupcake liner you throw away.
Expendable mold casting includes sand casting, investment casting, and plaster casting. You have to break these molds to remove the finished part, so you need a new mold for every single piece.
Non-expendable molds cost more upfront – sometimes 10 to 100 times more than expendable molds. But they pay for themselves when making large quantities of parts.
The surface finish is another big difference. Parts from non-expendable molds typically have a surface roughness of 50-125 microinches. Expendable mold parts are rougher at 250-500 microinches.
Production speed also varies dramatically. A permanent mold can produce a part every 2-5 minutes. Sand casting the same part might take 30-60 minutes including mold preparation.
Non-expendable molds work best for simpler shapes with fewer undercuts. Expendable molds can handle more complex geometries since you’re breaking them anyway. Each method has its place depending on what you’re making and how many you need.