Titanium investment casting is a precision manufacturing process that creates complex metal parts by pouring molten titanium into ceramic molds. This method produces high-quality components with excellent dimensional accuracy and superior surface finishes.
The process combines the exceptional properties of titanium—including high strength, corrosion resistance, and low weight—with the design flexibility of investment casting. Industries from aerospace to medical devices rely on this technique to create critical components that would be difficult or impossible to manufacture using traditional methods.
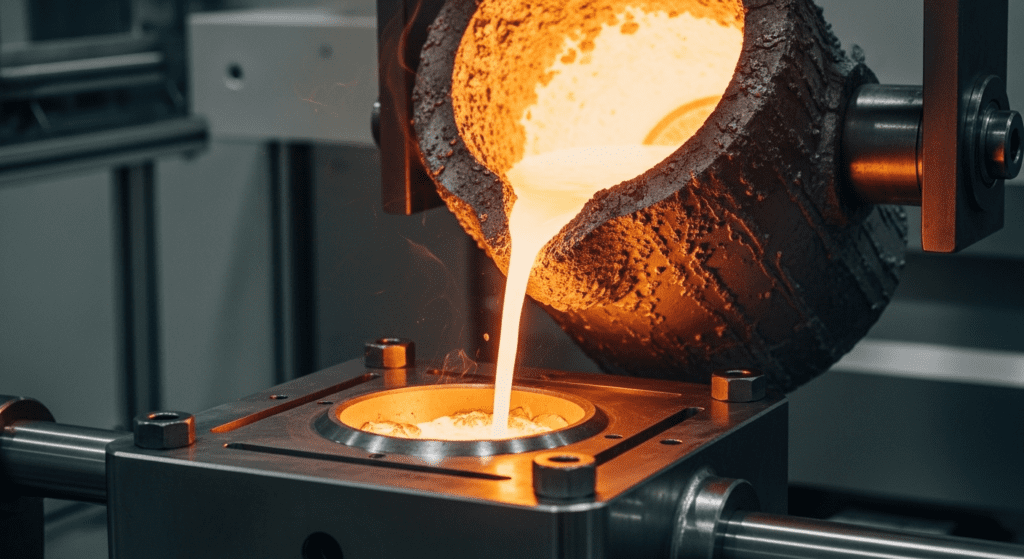
What is Titanium Investment Casting
Titanium investment casting is a precision manufacturing method that creates complex titanium parts. The process uses a wax pattern surrounded by ceramic material to form a mold.
Most importantly: This technique produces near-net-shape parts with excellent surface finish and dimensional accuracy. Unlike other methods, investment casting minimizes material waste and reduces machining time.
The process works especially well for titanium because it melts the metal in a vacuum environment. This prevents contamination and ensures the final part maintains titanium’s exceptional properties.
Titanium Investment Casting Process
Step 1: Pattern Creation
Engineers create a precise wax pattern matching the desired part dimensions. This pattern includes all details of the final titanium component.
Step 2: Assembly
Multiple wax patterns attach to a central wax sprue. This creates a tree-like structure that allows efficient casting of multiple parts.
Step 3: Shell Building
Workers dip the wax assembly into ceramic slurry repeatedly. Each layer dries before applying the next coat.
The ceramic shell typically requires 5-10 layers for adequate strength. This shell becomes the mold for the titanium.
Step 4: Wax Removal
Heat melts the wax out of the ceramic shell. This leaves a hollow cavity in the exact shape of the desired part.
Step 5: Preheating
The ceramic mold heats to extreme temperatures before receiving molten titanium. This prevents thermal shock and ensures proper metal flow.
Step 6: Melting and Pouring
Titanium melts in a vacuum furnace to prevent oxidation. The molten metal pours into the preheated ceramic mold.
Vacuum or inert gas environments protect the titanium from contamination.
Step 7: Cooling and Removal
The casting cools under controlled conditions. Workers then break away the ceramic shell to reveal the titanium part.
Step 8: Finishing
Final steps include removing excess material and surface treatments. Quality inspection ensures the part meets specifications.
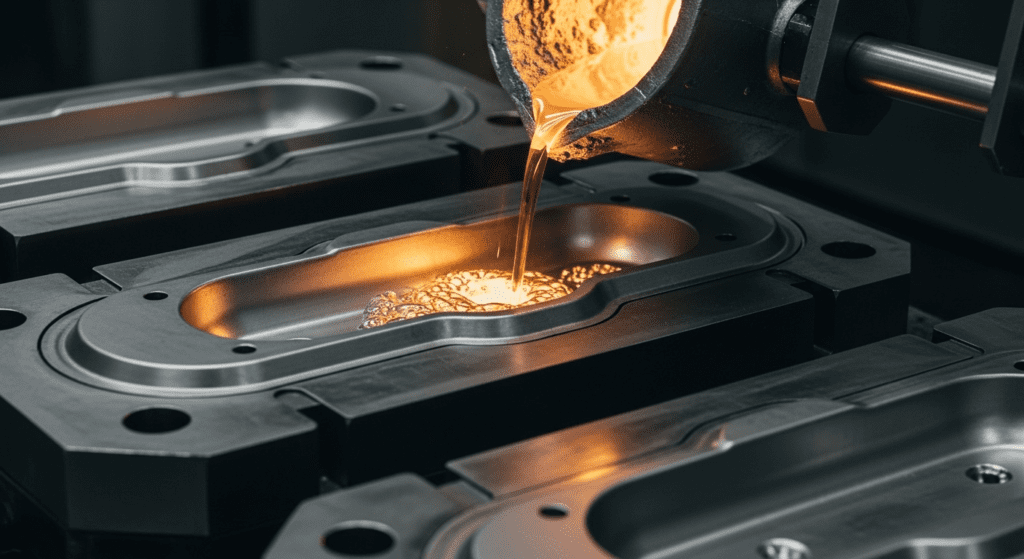
Types of Titanium Alloys
Investment casting works with various types of titanium alloys, each offering unique properties.
- Commercially Pure Titanium (Grades 1-4): Offers excellent corrosion resistance and formability. Used in chemical processing and marine applications.
- Ti-6Al-4V (Grade 5): The most common titanium alloy, containing 6% aluminum and 4% vanadium. Provides high strength-to-weight ratio for aerospace components.
- Ti-6Al-4V ELI (Grade 23): Extra low interstitial version of Grade 5. Preferred for medical implants due to superior fracture toughness.
- Ti-6Al-2Sn-4Zr-2Mo: Maintains strength at elevated temperatures up to 1000°F. Ideal for jet engine components.
- Ti-3Al-2.5V: Offers good weldability and moderate strength. Common in hydraulic tubing and sports equipment.
- Ti-15V-3Cr-3Sn-3Al (Ti-15-3-3-3): Heat-treatable beta alloy with excellent cold formability. Used in fasteners and springs.
Advantages of Titanium Investment Castings
Titanium investment castings deliver benefits impossible with other manufacturing methods.
- Complex Geometry: Creates intricate internal passages and thin walls that machining cannot achieve. Parts consolidate multiple components into single castings.
- Superior Surface Finish: Produces smooth surfaces requiring minimal post-processing. Typical surface roughness measures 125-250 RMS.
- Dimensional Accuracy: Maintains tolerances of ±0.005 inches per inch. Eliminates most secondary machining operations.
- Material Properties: Preserves titanium’s full strength and corrosion resistance. Vacuum melting prevents contamination.
- Cost Efficiency: Reduces material waste to near zero. Complex parts cost less than extensive machining from solid blocks.
- Weight Reduction: Enables hollow structures and optimized designs. Critical for aerospace fuel efficiency.
- Design Freedom: Allows undercuts, re-entrant angles, and variable wall thicknesses. Engineers optimize performance without manufacturing constraints.
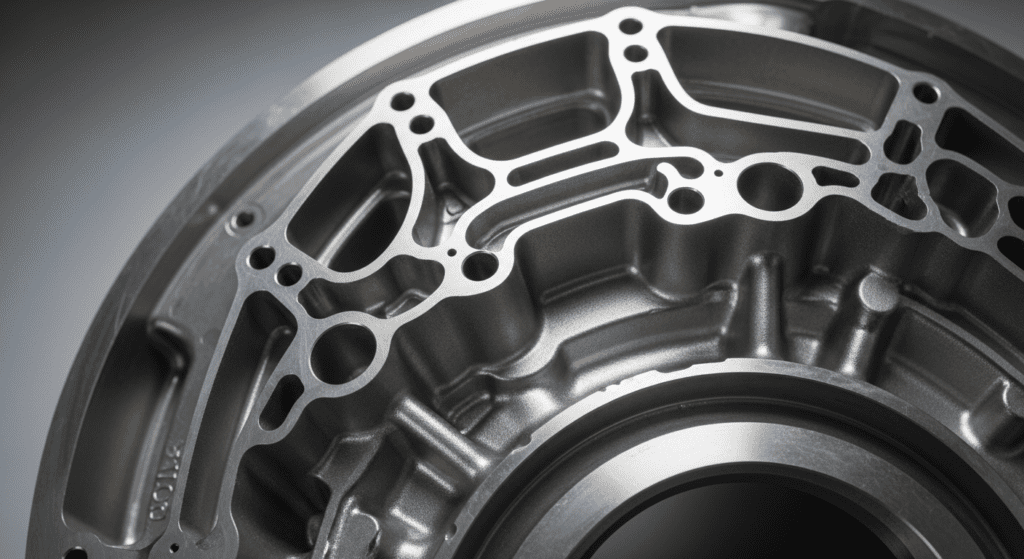
Applications of Titanium Investment Castings
- Aerospace: Turbine blades, compressor components, and structural brackets rely on titanium’s heat resistance. Aircraft benefit from weight savings without sacrificing strength.
- Medical: Surgical instruments, implants, and prosthetics use biocompatible titanium alloys. Investment casting creates complex geometries for anatomical fit.
- Marine: Propeller blades, pump components, and subsea equipment resist saltwater corrosion. Titanium outlasts other materials in harsh ocean environments.
- Chemical Processing: Valves, fittings, and reactor components handle corrosive chemicals safely. Titanium’s inert nature prevents contamination.
- Power Generation: Gas turbine parts and heat exchangers operate at extreme temperatures. Investment cast titanium maintains performance under stress.
- Automotive: High-performance engine components and exhaust systems benefit from titanium’s properties. Racing applications prioritize weight reduction.
- Defense: Military aircraft, naval vessels, and armor systems incorporate titanium castings. The material meets stringent performance requirements.