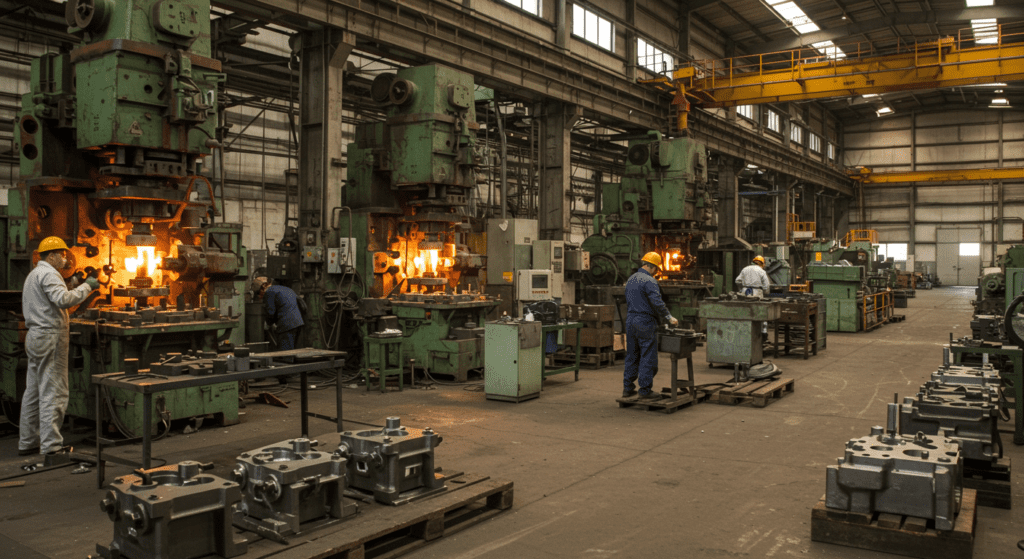
Advantages of Investment Casting
1. Design Flexibility
This flexibility allows for the creation of highly intricate and complex components that are often difficult, if not impossible, to produce economically or technically through other manufacturing methods.
- Intricate Geometries and Internal Features: The process excels at producing parts with complex internal cavities, tortuous passageways, undercuts, slots, and exceptionally fine surface details. Features such as logos, part numbers, or intricate textures can be directly incorporated into the casting, eliminating subsequent marking operations.
- Thin-Walled Sections: Investment casting is capable of reliably producing castings with significantly thinner walls compared to methods like sand casting. Minimum wall thicknesses can be as low as 1.00 mm.
- Part Consolidation: The ability to design and cast a single, complex component can effectively replaces an assembly previously made from multiple, simpler parts fabricated by other methods (e.g., machining, welding, brazing).
2. Material Versatility
Investment casting is compatible with a variety of Ferrous Alloys and Non-Ferrous Alloys materials.
Alloy Category | Specific Alloy Examples | Key Characteristics |
---|---|---|
Ferrous Alloys | ||
Stainless Steel | 304, 316, CF8M, 17-4 PH | Excellent corrosion resistance, good strength, hygienic, heat resistance |
Carbon Steel | Low, Medium, High Carbon | Good strength, machinability, weldability, cost-effective, heat treatable |
Low Alloy Steel | AISI 4140, 8620 | Higher strength than carbon steels, good toughness, wear resistance, heat treatable |
Tool Steel | A2, D2, H13 | High hardness, wear resistance, toughness, heat resistance (for hot work tools) |
Non-Ferrous Alloys | ||
Aluminum Alloys | A356, A380 | Lightweight, good corrosion resistance, high thermal/electrical conductivity |
Nickel-Based Superalloys | Inconel (718, 625), Hastelloy | Excellent high-temperature strength, creep resistance, superior corrosion resistance |
Cobalt-Based Superalloys | Stellite (Co-Cr alloys) | High wear resistance, corrosion resistance, biocompatibility, high-temp strength |
Copper Alloys | Bronze, Brass, BeCu | Good electrical/thermal conductivity, corrosion resistance, bearing properties |
Titanium Alloys | Ti-6Al-4V | High strength-to-weight ratio, excellent corrosion resistance, biocompatibility |
3. Superior Surface Finish
Reduced Need for Secondary Finishing: The smooth as-cast surface often minimizes or, in many cases, entirely eliminates the necessity for costly and time-consuming secondary finishing operations such as grinding, machining, or extensive polishing to achieve the desired surface texture.
4. High Dimensional Accuracy & Surface Finish
A typical surface finish for investment castings made from high-temperature alloys such as steel, stainless steel, or tool steel is in the range of 125μin Ra (Root Mean Square) or approximately 3.2μm Ra.
This contrasts sharply with sand castings, which typically exhibit much rougher surfaces, often in the range of 500 to 1000μin Ra.
5. Reduced Need for Secondary Finishing
The smooth as-cast surface often minimizes or, in many cases, entirely eliminates the necessity for costly and time-consuming secondary finishing operations such as grinding, machining, or extensive polishing to achieve the desired surface texture.
6. Absence of Parting Lines
Unlike components produced in multi-part molds (e.g., sand casting, die casting), investment castings are formed in a monolithic, seamless ceramic shell. Consequently, they typically exhibit no or only minimal, easily removable parting lines.
7. No Draft Required
In general, investment casting designs do not require the addition of draft angles to vertical surfaces, which are often necessary in other casting processes to facilitate pattern removal from the mold or part ejection from a die.
8. Tight Tolerances
The achievable dimensional tolerances in investment casting are significantly tighter than those typically associated with sand casting and can be competitive with, or in some cases exceed, those of die casting, especially for complex geometries.
General linear tolerances are often cited in the range of ±0.005 to ±0.015 inches per inch (±0.13 to ±0.38 mm per mm), or as a percentage, ±0.1% to ±0.5% of the linear dimension.
Feature/Dimension | Dimension Range (mm) | Typical Tolerance (± mm) |
---|---|---|
Linear Dimension | 0 – 10 | 0.15 |
10 – 25 | 0.20 | |
25 – 50 | 0.25 | |
50 – 75 | 0.30 | |
75 – 100 | 0.35 | |
Flatness (as % of nominal dimension) | N/A | 0.30% |
Straightness (as % of overall length) | N/A | 0.30% – 0.50% |
Roundness (as % of diameter) | N/A | 0.3% – 0.5% |
Perpendicularity (as % of dimension) | N/A | 0.3% |
Angular Tolerance | N/A | ± 0.5° |
Wall Thickness | < 6 mm | 0.30 |
> 6 mm | 0.50 | |
General (as ± in/in) | N/A | 0.005 |
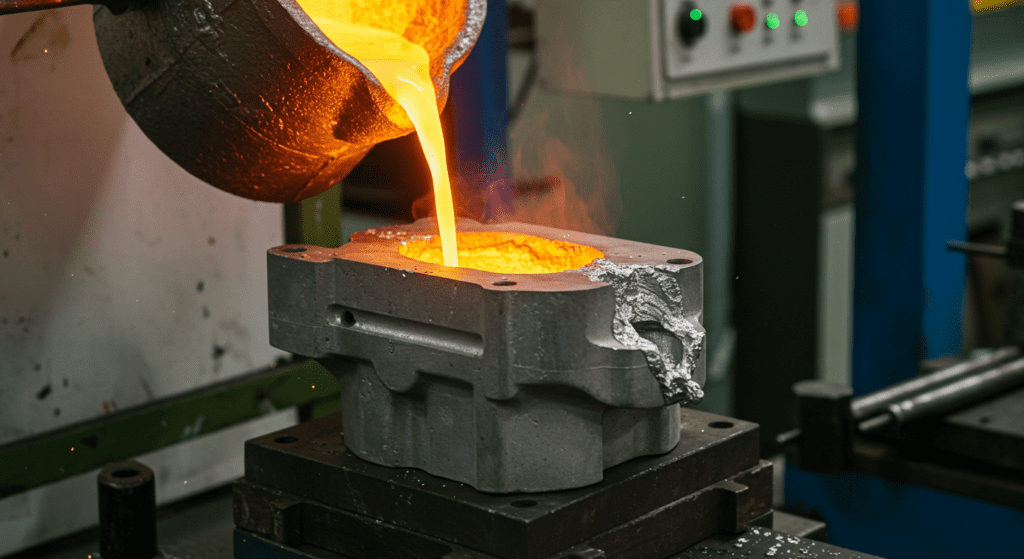
Disadvantages of Investment Casting
1. High Tooling and Production Costs
Due to the significant tooling costs and the inherently multi-stage, often labor-intensive nature of the investment casting process, the cost per part can be relatively high for small production runs or for prototypes if traditional hard tooling is employed.
2. Longer Lead Times
Each stage in the investment casting workflow requires a specific amount of time to complete correctly. The cumulative effect of these sequential operations results in significantly longer overall production lead times and casting cycles when compared to some other casting methods, such as die casting or even shell moulding.
3. Potential for Casting Defects
As a multi-stage and inherently complex manufacturing process, investment casting is susceptible to a variety of casting defects if not meticulously controlled at every step. The successful production of defect-free castings relies on a deep understanding of metallurgy, fluid dynamics, heat transfer, and materials science, coupled with rigorous process discipline.