The burnout cycle is the heating process that transforms a wax-filled ceramic shell into a hollow mold ready for metal casting.
During this stage of the investment casting process, manufacturers carefully remove wax from ceramic shells through controlled heating. The success of your final casting depends entirely on executing this cycle correctly.
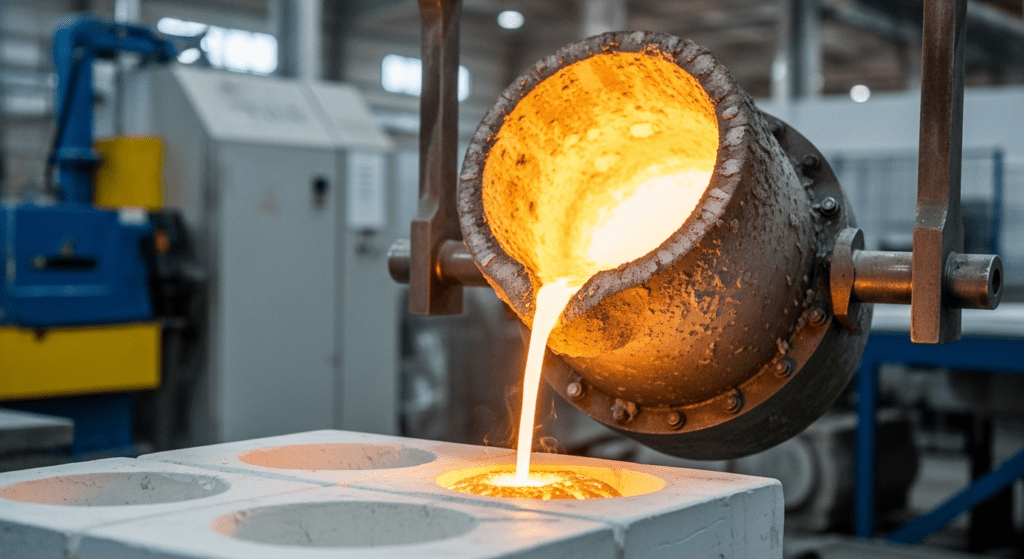
What is Burnout Cycle
The burnout cycle removes the wax pattern from inside the ceramic shell without damaging the mold.
Think of it like melting a candle inside a delicate vase. You need enough heat to melt the wax completely, but not so much that you crack the vase.
Different types of wax require different burnout temperatures and heating rates.
- Standard pattern waxes melt between 140-180°F.
- Filled waxes need higher temperatures.
- Water-soluble waxes require special handling to prevent shell damage from steam.
The burnout cycle serves three essential purposes. First, it removes all wax material from the shell cavity. Second, it strengthens the ceramic shell through high-temperature firing. Third, it preheats the mold for metal pouring.
Typical Burnout Cycle Stages
A complete burnout cycle follows four distinct stages.
Dewaxing
Dewaxing is the first and most critical stage. During this phase, molten wax drains from the shell as temperatures reach 200-400°F.
The key is rapid heating. Quick temperature rise prevents wax expansion that could crack your shell. Most foundries use steam autoclaves or flash fire furnaces for this stage.
Position shells with pour cups facing down. This allows gravity to pull molten wax out efficiently. Complete wax removal typically takes 10-20 minutes in an autoclave.
Drying and Low-Temperature Hold
After dewaxing, moisture must escape from the ceramic shell. This stage occurs at 400-600°F for 1-2 hours.
Slow, controlled heating prevents thermal shock. Rushing this stage causes micro-cracks that lead to casting defects.
The shell changes color during proper drying. Watch for uniform color change across the entire mold surface. Dark spots indicate trapped moisture that needs more drying time.
Ramp-Up Through Transition Zone
The transition zone spans 600-1200°F. This range burns out any remaining wax residue and organic binders.
Temperature increases should not exceed 100°F per hour. Faster heating rates risk shell cracking from thermal stress.
Carbon burnout occurs in this stage. Proper air circulation ensures complete combustion. Insufficient oxygen leaves carbon deposits that create surface defects on castings.
High-Temperature Burnout
The final stage reaches 1400-1800°F. These temperatures strengthen the ceramic shell and prepare it for metal pouring.
Hold time at peak temperature typically lasts 1-2 hours. Thicker shells need longer hold times for uniform heating.
The shell develops its final strength during this stage. Proper high-temperature burnout creates shells strong enough to withstand molten metal forces.
Troubleshooting Burnout Defects
Even experienced foundries encounter burnout problems. Here are the most common issues and their solutions.
Shell Cracking/Flashing
Shell cracks appear as raised lines on cast parts. These defects originate from thermal stress during burnout.
The most common cause is heating too quickly through the dewaxing stage. Wax expands faster than it can drain, creating internal pressure.
Prevention requires controlled heating rates. Limit temperature rise to 5°F per minute during initial dewaxing. Use thermocouples to monitor actual shell temperatures, not just furnace settings.
Incomplete Wax/Residue
Wax residue creates rough surface finishes and dimensional inaccuracies. This problem stems from insufficient burnout temperatures or times.
Check your wax supplier’s specifications. Some filled waxes need temperatures above 1500°F for complete removal.
Overloaded furnaces prevent proper heat circulation. Maintain adequate spacing between shells. Each mold needs exposure to hot air flow for complete wax removal.
Carbon buildup indicates incomplete organic burnout. Increase hold time in the 800-1200°F range. Ensure adequate oxygen supply for complete combustion.
Surface Defects
Surface defects include pitting, orange peel texture, and inclusions. These problems often trace back to burnout cycle issues.
Rapid temperature changes cause micro-cracking in shell surfaces. These tiny cracks fill with metal, creating rough textures.
Contamination during burnout also creates defects. Keep furnace interiors clean. Remove ash and debris between cycles.
Monitor furnace atmosphere carefully. Reducing conditions can react with shell materials. Maintain slight positive pressure with clean, dry air supply.