Heat treatment is a critical post-casting step to refine the microstructure and mechanical properties of metal components. By carefully heating a casting to specific temperatures, holding (soaking) for controlled times, and cooling in defined ways, foundries can tailor hardness, strength, ductility, toughness, wear resistance, and residual stress.
Typical heat treatments include annealing, normalizing, stress relief, quenching (hardening), tempering, martempering/austempering, solution treatment and aging (precipitation hardening), and surface hardening (carburizing/nitriding).
Annealing
Annealing heats metal to 1,550-1,850°F and then cools it slowly in the furnace. This process softens the metal and makes it easier to machine.
The slow cooling allows the metal’s crystal structure to reorganize. This removes internal stresses that build up during casting or cold working.
Annealing takes 4-12 hours depending on the metal type and thickness. Steel parts often need annealing before they can be machined or formed into final shapes.
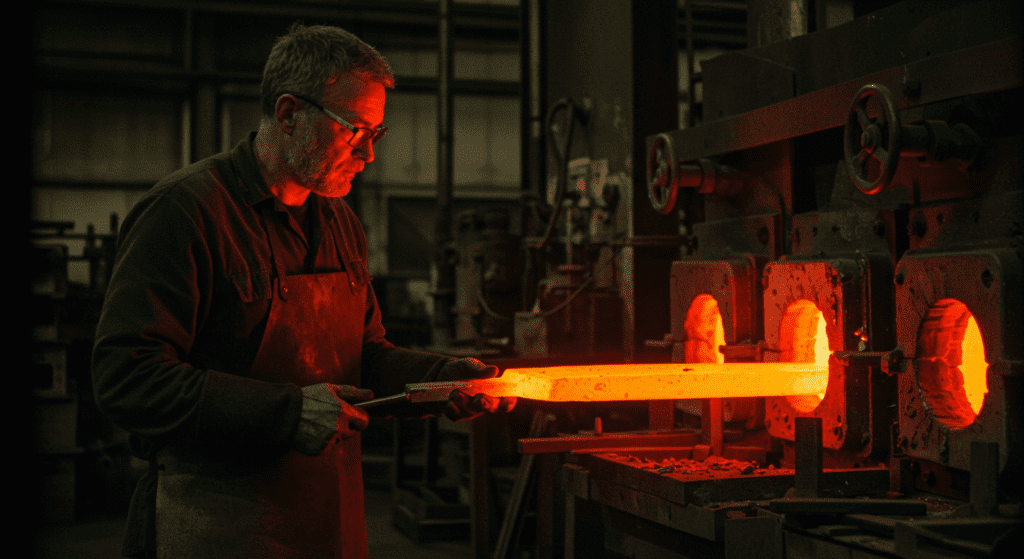
Stress-Relief Annealing
Stress-relief annealing heats metal to 1,000-1,200°F to remove internal stress without changing hardness. The temperature stays below the point where the metal’s structure changes.
This process prevents warping and cracking in finished parts. Welded structures and machined components often need stress relieving to stay dimensionally stable.
The metal heats for 1-2 hours per inch of thickness. Then it cools slowly in still air or in the furnace.
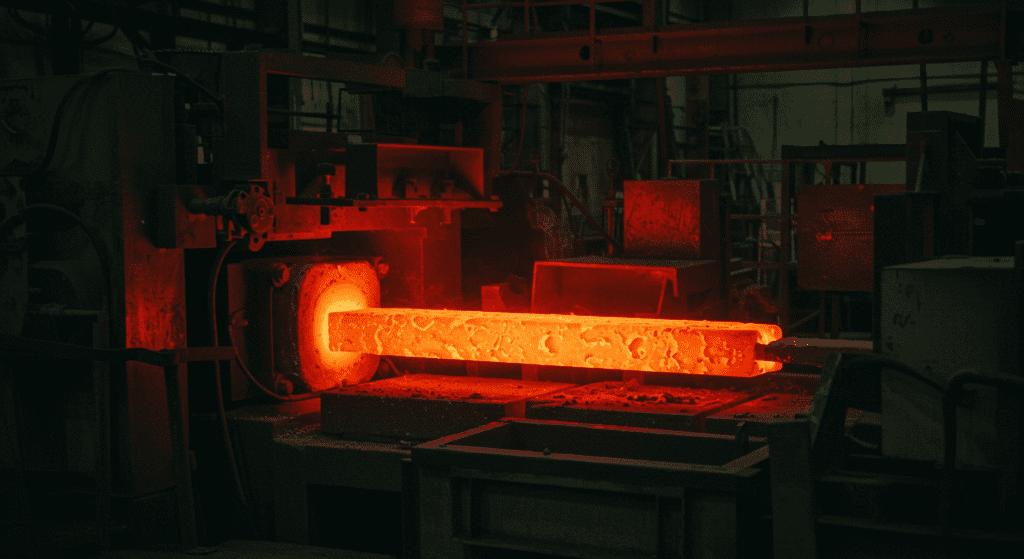
Normalizing
Normalizing heats steel above 1,600°F and then cools it in room temperature air. This creates a uniform grain structure throughout the metal.
The process takes 1-2 hours and produces parts that are 10-20% harder than annealed steel. Normalized steel machines better and has more consistent properties.
Castings and forgings often undergo normalizing to improve their structure. The air cooling creates a finer grain size than furnace cooling.
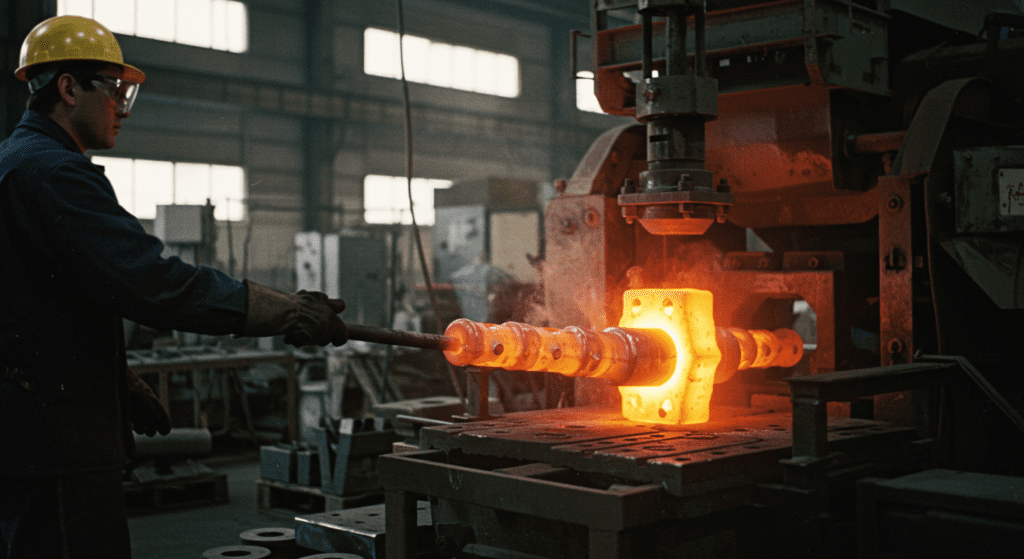
Quenching (Hardening)
Quenching rapidly cools heated metal in water, oil, or air to increase hardness. Steel must heat to 1,450-1,550°F before quenching to achieve maximum hardness.
Water quenching cools fastest and creates the hardest results. Oil quenching reduces the risk of cracking by cooling more slowly.
The rapid cooling traps carbon atoms in the steel’s crystal structure. This creates a hard but brittle material that usually needs tempering.
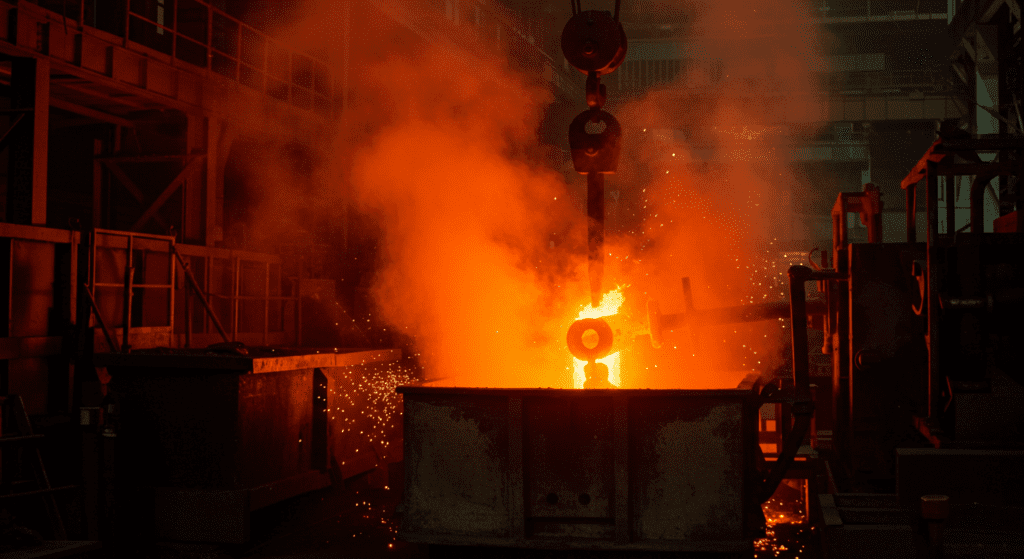
Tempering
Tempering reheats quenched steel to 300-1,200°F to reduce brittleness while maintaining hardness. Higher tempering temperatures create tougher but softer steel.
The process takes 1-4 hours depending on the desired properties. A drill bit might temper at 550°F for hardness, while a spring tempers at 800°F for flexibility.
Tempering transforms the brittle martensite structure into a tougher combination of ferrite and carbides. This balances hardness with toughness for practical use.
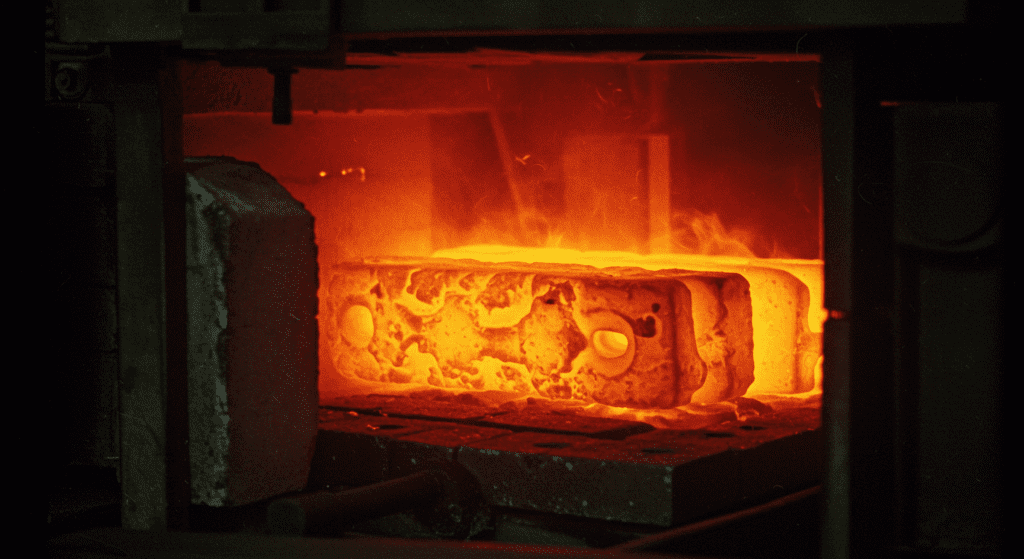
Isothermal Quenching
Martempering
Martempering quenches steel in a molten salt bath at 400-600°F before air cooling. This reduces distortion and cracking compared to regular quenching.
Austempering
Austempering holds the steel at 500-750°F for several hours to create bainite. This structure provides excellent toughness at high hardness levels.
Both processes produce less distortion than conventional quenching. Gears, springs, and precision parts often use these methods.
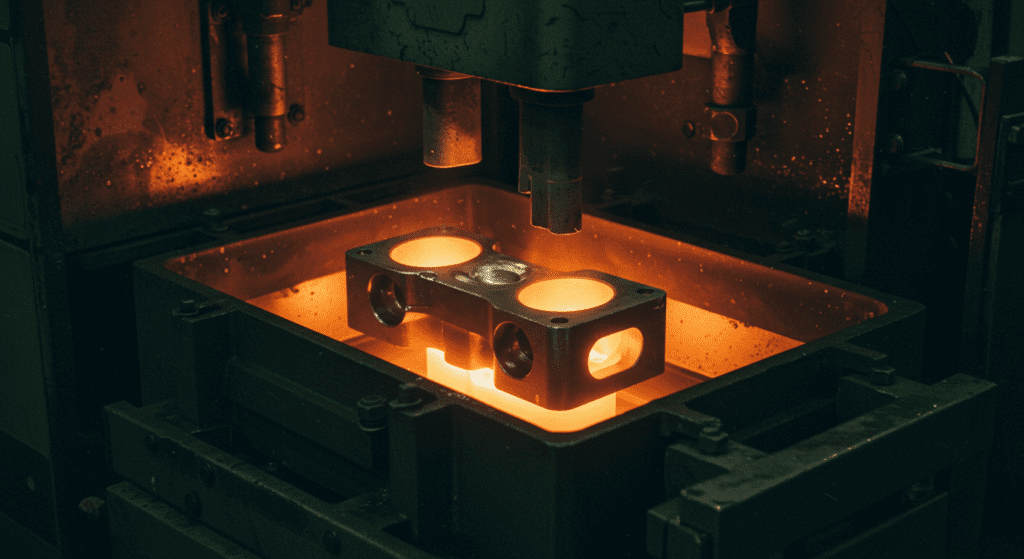
Precipitation Hardening
Solution heat treatment dissolves alloying elements at 900-1,000°F, followed by rapid cooling. This creates a supersaturated solid solution in aluminum and other non-ferrous alloys.
Aging then heats the metal to 250-500°F for 4-24 hours. Fine precipitates form throughout the structure, increasing strength by 50-100%.
Surface Hardening
Surface hardening creates wear-resistant surfaces while maintaining tough cores. These heat treatment methods modify only the outer layer of parts.
Carburizing
Carburizing adds carbon to steel surfaces by heating parts to 1,650-1,750°F in a carbon-rich atmosphere. The process takes 4-20 hours depending on the desired depth.
Gas carburizing uses methane or propane as the carbon source. Pack carburizing surrounds parts with carbon-rich powder.
The high-carbon surface can reach 60-63 HRC hardness after quenching. Gears, bearings, and camshafts commonly undergo carburizing.
Nitriding
Nitriding diffuses nitrogen into steel surfaces at 950-1,050°F using ammonia gas. The process creates an extremely hard surface layer of 65-70 HRC.
The lower temperature prevents distortion, making nitriding ideal for finished parts. The case depth reaches 0.001-0.020 inches after 10-80 hours.
Nitrided surfaces resist wear, corrosion, and fatigue better than carburized surfaces. Die-casting dies and extrusion screws benefit from nitriding.
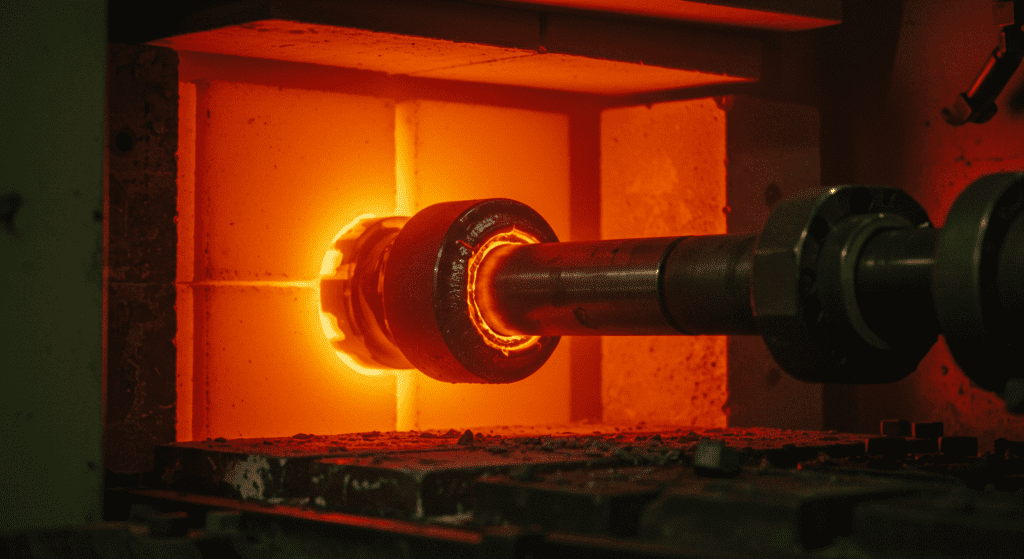
Other Processes
Induction and Flame Hardening
Induction hardening uses electromagnetic fields to heat steel surfaces to 1,550°F in seconds. Water spray immediately quenches the heated area.
Flame hardening uses oxy-acetylene torches for the same purpose. Both methods harden specific areas without affecting the entire part.
These processes work on medium-carbon steels with 0.40-0.50% carbon. Shafts, gears, and wear plates often receive localized hardening.
Cryogenic Treatment
Cryogenic treatment exposes metals to temperatures below -250°F using liquid nitrogen. The process completes martensitic transformation in quenched steels. Retained austenite converts to martensite during deep cooling.
Treatment takes 24-36 hours including controlled cooling and warming. Parts show improved wear resistance and dimensional stability. Tool steels and high-performance alloys benefit most from cryogenic processing.
Summary Comparison Table
Process | Temp/Cooling | Microstructure | Materials | Applications | Advantages | Disadvantages |
---|---|---|---|---|---|---|
Annealing | Heat to α↔γ region (~Ac1–Ac3), soak, very slow cool (furnace) | Coarse ferrite+pearlite or spheroidite; stress relief | Carbon & alloy steels; gray and malleable irons; Cu, Al alloys | Machinable castings, ductile parts, pre-forming | Softens metal, high ductility, reduced stress | Lowers strength, coarse grains, long cycle |
Stress Relief | 500–700 °C (steel) or ~500°C (cast iron), soak, slow air/furnace cool | Essentially unchanged (recovery of dislocations); small grain growth possible | Almost any casting alloy (steels, irons, Al) | Large/thick castings, welded or machined parts | Reduces distortion, improves stability and toughness | Minimal softening; extra step |
Normalizing | ~20–50°C above Ac3, soak, air cool | Fine, uniform ferrite+pearlite (refined grains) | Carbon & low-alloy steels | Structural castings (gears, shafts), pregrown steel | Refines grain, tougher/stronger than annealed | Harder than annealed, some quench stress |
Quenching | Above Ac3, soak, quench in water/oil/polymer | Martensite (±bainite); very hard, brittle | Medium/high-carbon steels, tool steels, some irons | Wear parts, tools, gears, shafts | Maximizes hardness and strength | High brittleness, distortion/cracking |
Tempering | 150–600 °C (low temp relative), soak, cool | Tempered martensite (ferrite + dispersed carbides) | Quenched steels (carbon, alloy) | After hardening: springs, gears, tools | Increases toughness, reduces brittleness | Reduces hardness, extra processing |
Martempering | Quench to ~100–200 °C, hold, then air cool | Martensite (less stressed) | High-carbon/alloy steels | Thick/hardened parts (carburized gears) | Lower stresses than direct quench, uniform hardness | Complex control, limited cooling rate |
Austempering | Quench to ~260–400 °C, hold isothermal, then cool | Bainitic (ausferrite) structure | Medium-carbon steels; ductile iron (ADI) | ADI wear parts, high-strength castings | High toughness & wear resistance, less distortion | Requires salt bath, only some alloys suit |
Solution + Aging | Heat to solution temp (e.g. 500–1050 °C), quench, then age at 150–600 °C | Single-phase solid solution → fine precipitates (e.g. Al₂Cu, Ni₃Ti) | Al alloys (2xxx,6xxx,7xxx); PH stainless; Ni alloys | Aerospace components, hardened aluminum castings | Very high strength and corrosion resistance | Distortion, long process, strict temp control |
Carburizing | ~850–950 °C in C-rich bath/gas, soak, then quench | High-carbon martensitic surface; soft core | Low-C steels, ductile cast iron | Gears, cams, shafts, wear surfaces | Hard surface with ductile core; high fatigue strength | Distortion, long cycles, toxic media (liquid) |
Nitriding | ~480–550 °C in NH₃ gas, long soak, no quench | Hard nitride layer (Fe₄N etc.) on surface, unchanged core | Nitride-forming steels (Cr, Al steels) | Fuel pump parts, cutting edges, shafts | Very hard case; minimal distortion; oil-free process | Slow (hours), shallow case, limited alloy choice |