Titanium investment casting uses seven main alloy types, each designed for specific applications. The most common is Ti-6Al-4V (Grade 5), which accounts for over 50% of all titanium casting applications. These alloys range from commercially pure titanium for corrosion resistance to complex beta alloys for extreme strength requirements.
Investment casting allows manufacturers to create complex titanium parts with thin walls and precise details. The process works well with these specific alloys because they maintain good flowability when molten and solidify with minimal defects.
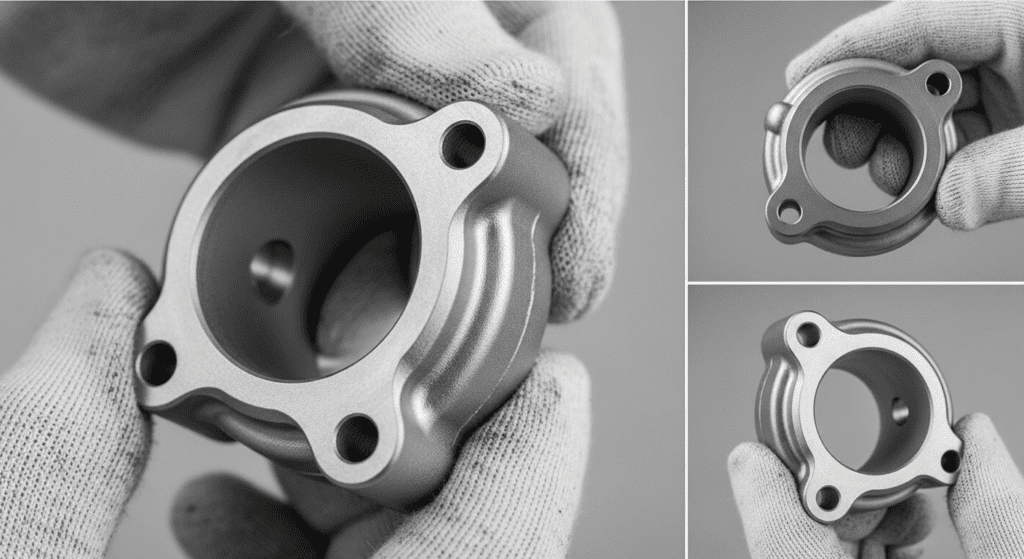
Alloy | Key Composition | UTS (MPa) | YS (MPa) | Elongation (%) | Hardness (HB) |
---|---|---|---|---|---|
CP Ti (Grade 2) | Ti ≥ 99.2% (C≤0.08%, N≤0.03%, O≤0.25%, H≤0.015%, Fe≤0.30%) | ≈345 | ≈275 | ≈20 | ~160 (≈46 HRC) |
Ti-6Al-4V (Grade 5) | Al 5.5–6.5%, V 3.5–4.5%; C≤0.08%, Fe≤0.25%, N≤0.05%, O≤0.2% | 900–1000 | 828–910 | 10–18 | ≈36 HRC |
Ti-6Al-4V ELI (Grade 23) | Same as Grade 5 but with lower O (≤0.13%) for toughness | ≈895–1000 | ≈828–910 | 12–18 | ≈36 HRC |
Ti-6Al-7Nb (ASTM F1295) | Al 5.5–6.5%, Nb 6.5–7.5%; C≤0.08%, Fe≤0.25%, O≤0.20%, N≤0.05% | ≈900 (≥900) | ≥800 | ≥10 | – |
Ti-6Al-2Sn-4Zr-2Mo | Al 5.5–6.5%, Sn 1.8–2.2%, Zr 3.6–4.4%, Mo 1.8–2.2%; Fe≤0.25%, O≤0.15% | 1110 | 1050 | 13 | 318 HB (34 HRC) |
Ti-5Al-2.5Sn (Grade 6) | Al 4–6%, Sn 2–3%; Fe≤0.50%, O≤0.20%, N≤0.03% | ≈830 | ≈795 | ≈10 | 320 HB (36 HRC) |
Beta (15-3-3-3) | V 15%, Cr 3%, Al 3%, Sn 3%; balance Ti | 790 | 770 | 22 | HRB 95 |
CP Ti (Grade 2)
Commercially Pure Titanium Grade 2 contains 99.2% titanium with small amounts of oxygen, nitrogen, and carbon. This alloy offers the best corrosion resistance among all titanium grades.
CP Ti Grade 2 excels in chemical processing equipment and marine applications. Its lower strength compared to other grades makes it ideal when ductility and formability matter more than mechanical properties.
The casting temperature for Grade 2 runs between 1,670°C and 1,720°C. Investment casters must use special ceramic molds that can withstand these extreme temperatures without reacting with the titanium.
Ti-6Al-4V (Grade 5)
Ti-6Al-4V stands as the workhorse of titanium alloys. It contains 6% aluminum and 4% vanadium, creating an excellent balance of strength, weight, and corrosion resistance.
This alpha-beta alloy maintains its strength up to 400°C. Aerospace manufacturers use it for turbine blades, structural components, and landing gear parts.
The alloy’s versatility extends beyond aerospace. Medical device companies cast hip implants and dental components from Grade 5. Its biocompatibility and fatigue resistance make it perfect for long-term implantation.
Investment casting Grade 5 requires precise temperature control. The pouring temperature typically ranges from 1,700°C to 1,750°C. Proper mold design prevents hot tearing during solidification.
Ti-6Al-4V ELI (Grade 23)
Extra Low Interstitial (ELI) Grade 23 offers improved ductility and fracture toughness compared to standard Grade 5. The reduced oxygen content (0.13% maximum versus 0.20%) creates these enhanced properties.
Medical applications dominate Grade 23 usage. Spinal fusion cages, bone screws, and cardiovascular devices benefit from its superior fatigue performance in body fluids.
The casting process for Grade 23 demands stricter controls. Foundries must minimize contamination from oxygen and nitrogen during melting and pouring. Vacuum or argon atmospheres protect the molten metal.
Ti-6Al-7Nb (ASTM F1295)
Ti-6Al-7Nb replaces vanadium with niobium to eliminate concerns about vanadium ion release in the human body. This alloy matches Grade 5’s mechanical properties while offering superior biocompatibility.
European medical device manufacturers prefer this alloy for permanent implants. Its corrosion resistance in physiological solutions exceeds that of Ti-6Al-4V.
Investment casting Ti-6Al-7Nb requires similar parameters to Grade 5. The niobium addition slightly increases the melting point, requiring temperatures around 1,720°C to 1,770°C for optimal flow.
Ti-6Al-2Sn-4Zr-2Mo
This near-alpha alloy maintains strength at temperatures up to 500°C. The tin and zirconium additions provide solid solution strengthening, while molybdenum improves high-temperature creep resistance.
Jet engine manufacturers specify this alloy for compressor discs and blades. Its superior creep resistance allows thinner sections, reducing component weight.
The complex chemistry demands precise alloying control during melting. Investment casters typically use vacuum arc remelting to ensure chemical homogeneity. Pouring temperatures range from 1,750°C to 1,800°C.
Ti-5Al-2.5Sn (Grade 6)
Grade 6 offers intermediate strength between CP titanium and Ti-6Al-4V. The tin addition provides solid solution strengthening without forming brittle phases.
This alloy excels at cryogenic temperatures. Aerospace companies use it for liquid fuel tanks and cryogenic piping systems. Its weldability surpasses that of higher-strength titanium alloys.
Investment casting Grade 6 proves less challenging than more complex alloys. The absence of beta-stabilizing elements reduces segregation during solidification. Typical pouring temperatures range from 1,680°C to 1,730°C.
Beta (15-3-3-3)
Ti-15V-3Cr-3Al-3Sn represents a metastable beta alloy with exceptional cold formability. After solution treatment and aging, it achieves strengths exceeding 1,400 MPa.
This alloy finds use in springs, fasteners, and sheet metal components. Investment casting allows production of complex spring housings and specialized fasteners impossible to machine.
Beta titanium alloys present unique casting challenges. Their high beta-stabilizer content promotes segregation during solidification. Casters must use rapid solidification techniques and subsequent heat treatment to achieve uniform properties.
The pouring temperature for 15-3-3-3 typically ranges from 1,650°C to 1,700°C, lower than alpha-beta alloys due to the beta stabilizers’ effect on melting point.