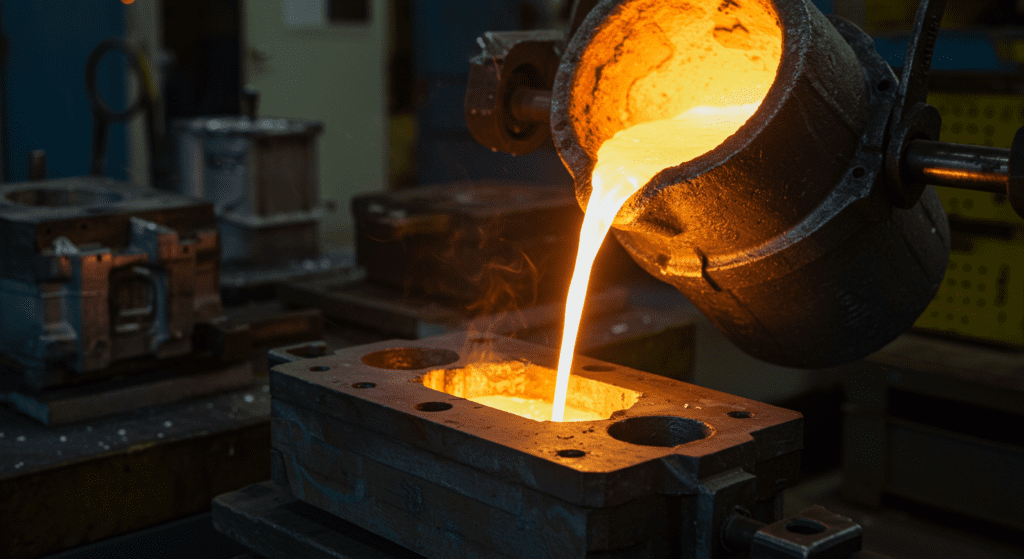
TLDR Overview
Investment casting wax is foundational to producing precise metal components through the lost wax process. This article explores the four main categories: pattern waxes (unfilled, filled, and emulsified) that form the actual part geometry; runner waxes that create the feeding system; soluble waxes that enable complex internal features; and accessory waxes used for assembly and repairs. Each type offers specific advantages in flow characteristics, dimensional stability, strength, and processing requirements that foundries must consider when selecting the optimal wax for different casting applications.
Category | Sub-Type / Example | Primary Function | Key Distinguishing Feature(s) |
---|---|---|---|
Pattern Wax | Unfilled (Straight) | Create primary replica of the final part | Minimal/no inert filler; prone to shrinkage; high recyclability |
Filled (e.g., XLPS-filled) | Create primary replica of the final part | Contains significant inert filler; high dimensional stability | |
Emulsified | Create primary replica of the final part | Contains water emulsion; reduced cavitation vs. unfilled | |
Runner Wax | Gating Wax | Form sprue/runner system for wax/metal flow | Often lower melt point/viscosity than pattern wax; good strength |
Soluble Wax | Core Wax (Fiber/Fiber-Free) | Create complex internal cavities/cores | Dissolves in water or mild acid solution |
Accessory Wax | Sticky (Adhesive) Wax | Assemble patterns to runner; minor pattern repair | Strong adhesive properties; low melting point |
Patching/Utility Wax | Repair defects on patterns/assemblies | Soft, pliable; fills voids/scratches | |
Dipping/Sealing Wax | Coat wax assembly for surface smoothing/adhesion | Low viscosity/melt point; forms thin outer layer |
Pattern Waxes
Pattern waxes are the foundation of investment casting because they determine the geometric shape and surface quality of the final product. The quality of the investment casting wax selected for pattern creation directly impacts dimensional accuracy, surface finish, and overall casting success.
Unfilled (Non-Filled / Straight) Waxes
Unfilled pattern waxes are complex mixtures, primarily composed of petroleum-derived waxes (such as paraffin and microcrystalline wax) blended with various natural and synthetic resins. They are characterized by the deliberate absence or extremely low content of inert fillers.
A key characteristic of unfilled waxes is their typically excellent flow behavior, generally exhibiting lower viscosity compared to filled waxes. This allows the molten wax to easily fill complex details and intricate sections of injection molds.
However, a significant disadvantage compared to filled waxes is their higher tendency for volumetric contraction (shrinkage) during cooling and solidification. This shrinkage, combined with potentially slower or uneven solidification rates, makes them susceptible to surface defects such as cavitation (internal voids) and sink marks (surface depressions), particularly in thicker sections of the pattern. To mitigate these dimensional issues, foundries may need to employ strategies such as using metal “chills” placed within the cavity to accelerate cooling in specific areas, or adopt paste injection techniques where wax is injected in a semi-solid state.
Filled Waxes
These waxes contain significant amounts of fine powdered inert fillers mixed into the wax/resin matrix. The fillers are typically organic to ensure clean burnout and may include materials such as cross-linked polystyrene (XLPS), terephthalic acid (PTA), or bisphenol A (BPA). Modern filled waxes typically contain between 20-40% filler content by weight, carefully balanced to achieve optimal properties without compromising injectability.
The significant advantage of filled waxes is their substantially enhanced dimensional stability compared to unfilled waxes. The filler particles physically restrict the shrinkage of the wax matrix during cooling, resulting in greatly reduced thermal expansion and significantly less shrinkage and cavitation, even in thick or heavy sections of patterns. This typically eliminates the need for wax chills.
Filled waxes can typically be successfully injected across a wider range of temperatures and injection conditions, from fully liquid to semi-solid pastes. In the solid state, filled waxes typically have lower thermal conductivity than unfilled waxes. However, the presence of fillers impedes the dewaxing process; burnout may take longer, and filler residues are more likely to remain inside the ceramic shell if burnout is incomplete.
Emulsified Waxes
Emulsified pattern waxes have a similar base formulation to unfilled waxes (a mixture of waxes and resins), but are distinguished by the addition of water through an emulsification process, typically with water content between 7-12%. In this system, the finely dispersed water droplets act as temporary partial fillers within the wax matrix. These microscopic water droplets remain stably suspended through the use of specialized emulsifying agents that prevent separation.
Feature | Unfilled (Straight) Wax | Filled Wax | Emulsified Wax |
---|---|---|---|
Composition Basis | Wax/resin blend | Wax/resin blend + inert organic filler (e.g., XLPS, PTA) | Wax/resin blend + Water emulsion (7-12%) |
Filler Content | Minimal / None | Significant (e.g., 5-45%) | Water acts as partial filler |
Dimensional Stability | Lower | Highest | Moderate (better than unfilled) |
Shrinkage/Cavitation Tendency | High, esp. in thick sections | Lowest | Reduced compared to unfilled |
Typical Surface Finish | Excellent, smooth, glossy | Good to excellent, depends on filler size/type | Excellent, very smooth |
Flow Properties (Viscosity) | Excellent (Low Viscosity) | Generally higher viscosity | Good flow |
Recyclability | High / Easy | Difficult / Costly | High / Relatively Easy (water removal needed) |
Processing Considerations | May need chills, paste injection, precise temp control | Requires agitation when molten; slower burnout possible | Requires strict temperature control (below 80-85°C) |
Typical Applications | Small/medium parts, intricate details, high finish needs | Large/complex parts, high accuracy needs, thin walls | Smooth finish needs, moderate cavitation control |
Relative Initial Cost | Generally Lower | Generally Higher | Intermediate |
Runner Waxes (Gating Waxes)
Runner waxes, also known as gating or sprue waxes, are used to construct the complex assemblies commonly referred to as “trees,” which consist of a central downsprue (main vertical channel), runners (horizontal channels branching from the sprue), and gates (small connectors that attach individual patterns to the runners).
The color of runner waxes is often distinctly different from pattern waxes. Most runner waxes are designed to have slightly lower melting points than pattern waxes, which facilitates a controlled dewaxing sequence where the runner system begins to soften and melt first.
Soluble Waxes
Soluble waxes enable the production of parts with highly complex internal geometries. These waxes can be used to create temporary “cores” for defining internal cavities, channels, undercuts, or blind holes in the final metal component—features that would be difficult or impossible to form using the rigid metal tooling used for molding the main pattern wax.
The soluble wax core serves as a precise shape placeholder for desired voids within the casting. After molding the main pattern wax around the soluble core, the soluble core is selectively removed, leaving the desired internal cavities in the pattern, which are then replicated in the final metal component.
Fiber-Filled Soluble Waxes
Contain fibrous materials that enhance the mechanical strength and toughness of soluble cores. The fibers help maintain core integrity, especially in geometries with varying thick and thin sections.
Fiber-filled soluble waxes generally require specialized equipment for melting and injection due to the fibrous content. Conventional tank melters with agitation capability are typically used to maintain uniform fiber distribution throughout the molten material.
Fiber-Free Soluble Waxes
Represent a newer generation of materials, these formulations achieve sufficient strength and dimensional stability without fiber additives. The elimination of fibers simplifies the handling of leaching bath waters since there are no solid fibers to filter out. Fiber-free waxes can typically be melted using convenient tilting furnaces, while fiber-filled waxes often require traditional stirred tank melting.
Accessory Waxes
Beyond the primary pattern, runner, and soluble waxes, a range of accessory and specialty waxes play important supporting roles in the investment casting process, contributing to assembly, repair, and surface treatments.
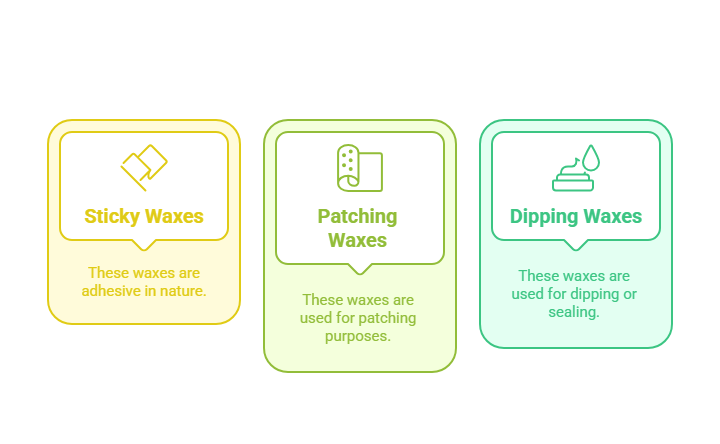
Sticky Waxes (Adhesive Waxes)
The primary function of sticky waxes is to act as a strong adhesive or bonding agent. Their most common application is during the “tree building” phase, where they are used to firmly attach individual wax patterns to the wax runner system. They may also be used for minor repairs to broken or damaged wax patterns or assemblies.
Sticky waxes possess high tackiness and strong adhesive properties, providing both adhesion (sticking to surfaces) and cohesive (internal strength) bonding. They typically have relatively low melting points, making them easy to melt for use and quick to solidify upon cooling.
Patching/Utility Waxes
Patching waxes are specifically used to repair surface defects on wax patterns, assemblies, or even soluble cores before the shell building process begins. These waxes can be used to fill and smooth out defects such as scratches, voids, sink marks, or minor damage, ensuring defect-free surfaces for higher quality final castings. Utility waxes serve similar repair functions but may also be used for other miscellaneous tasks in the wax room, such as assembling pattern segments.
These waxes are typically soft and pliable at room temperature or close to it, allowing them to be easily manipulated by hand or tools to fill defects. They can often be further softened or completely melted with gentle heating for application.
Dipping/Sealing Waxes
Dipping or sealing waxes are applied as a very thin, uniform outer coating over the entire wax pattern assembly after assembly construction and cleaning, but before the first (primary) dip in ceramic slurry.
The primary purpose of dipping waxes is to seal the pattern surface, filling microscopic pores, surface imperfections, or parting lines that might otherwise trap air or cause defects in the ceramic shell. By creating a smooth, continuous surface, these waxes help prevent air bubbles in the primary slurry coat and improve surface quality of the final casting.
What temperature should wax be for investment casting
Heat wax to 62–65°C (143–149°F) for investment casting. This range allows the wax to remain fluid enough for injection while maintaining detail accuracy. Temperatures above 70°C can degrade surface quality, while lower temperatures may cause poor mold filling.