Automotive die casting is a manufacturing process that injects molten metal into steel molds under high pressure to create precise, lightweight vehicle components. It is widely used to produce engine blocks, transmission cases, and structural parts from aluminum or magnesium alloys for strength, weight reduction, and cost efficiency.
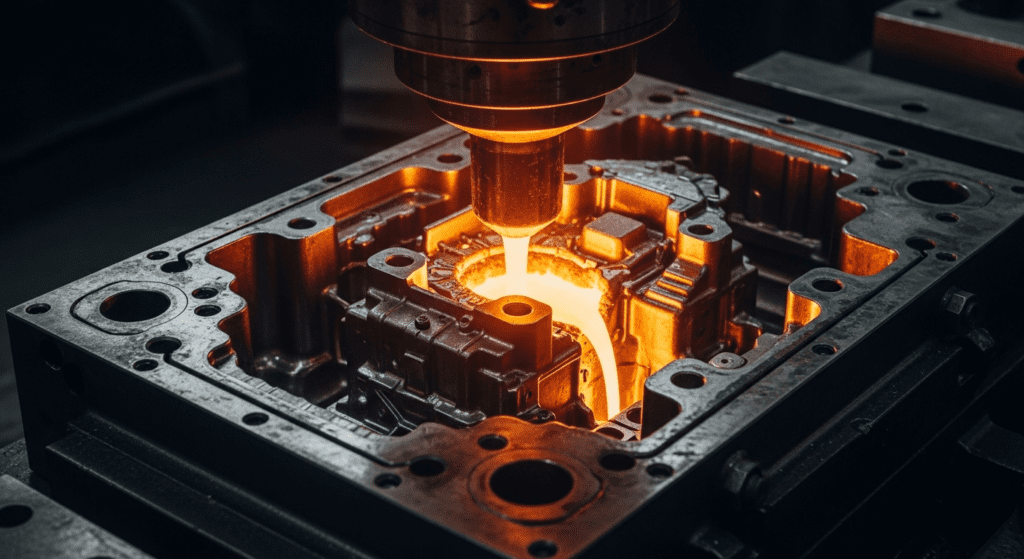
What is Automotive Die Casting
Automotive die casting is a manufacturing process that creates metal car parts by forcing molten metal into steel molds under high pressure. The process produces complex shapes with smooth surfaces and tight tolerances.
Car manufacturers use die casting to make engine blocks, transmission cases, wheels, and hundreds of other parts. The method works faster and costs less than traditional machining for high-volume production.
Automotive Die Casting Process
The die casting process starts with melting metal in a furnace until it becomes liquid. Workers then inject this molten metal into a two-part steel mold called a die.
The machine clamps the die halves together with forces ranging from 25 to 3,000 tons. This pressure keeps the mold closed while liquid metal fills the cavity.
After the metal solidifies, the machine opens the die and ejects the finished part. The whole cycle takes between 30 seconds and 2 minutes, depending on the part size.
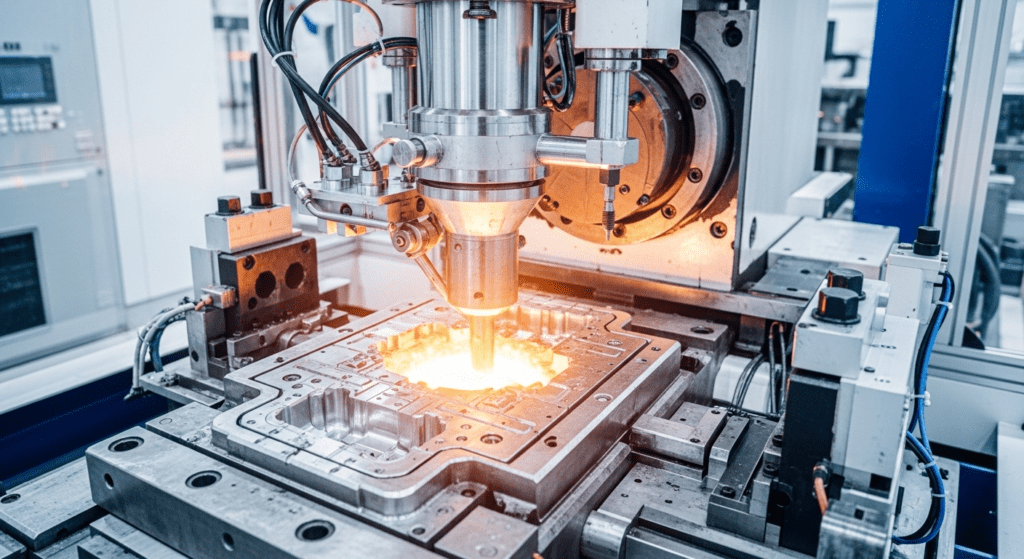
Types of Die Casting Process
There are two main types of die casting processes used in automotive manufacturing.
Cold Chamber Die Casting
Cold chamber die casting keeps the melting furnace separate from the injection system. Workers ladle molten metal into a shot chamber for each cycle.
A hydraulic piston pushes the metal from the shot chamber into the die at pressures up to 20,000 PSI. This high pressure fills thin sections and creates fine details.
The process works best for metals with high melting points like aluminum and magnesium. These metals would damage the injection system if kept constantly hot.
Cold chamber machines produce larger parts than hot chamber systems. They can make engine blocks weighing up to 100 pounds.
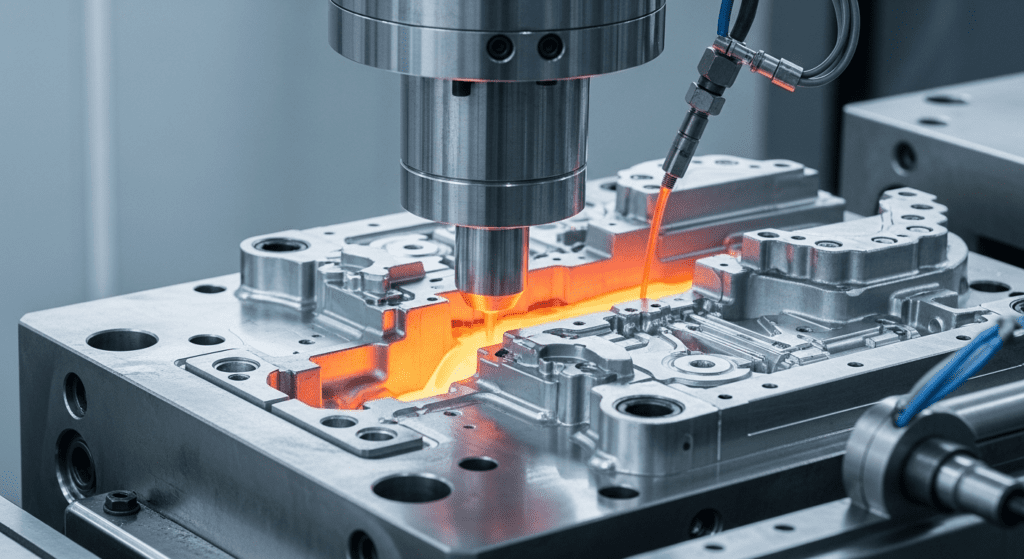
Hot Chamber Die Casting
Hot chamber die casting submerges the injection system directly in the molten metal bath. A gooseneck feeds liquid metal into the die with each cycle.
The process runs faster than cold chamber casting because metal stays ready in the system. Cycle times range from 15 to 30 seconds for small parts.
Hot chamber machines work only with metals that melt below 1,000°F. Higher temperatures would dissolve the steel injection components.
This method produces smaller, precise parts like door handles and dashboard components. The parts typically weigh less than 10 pounds.
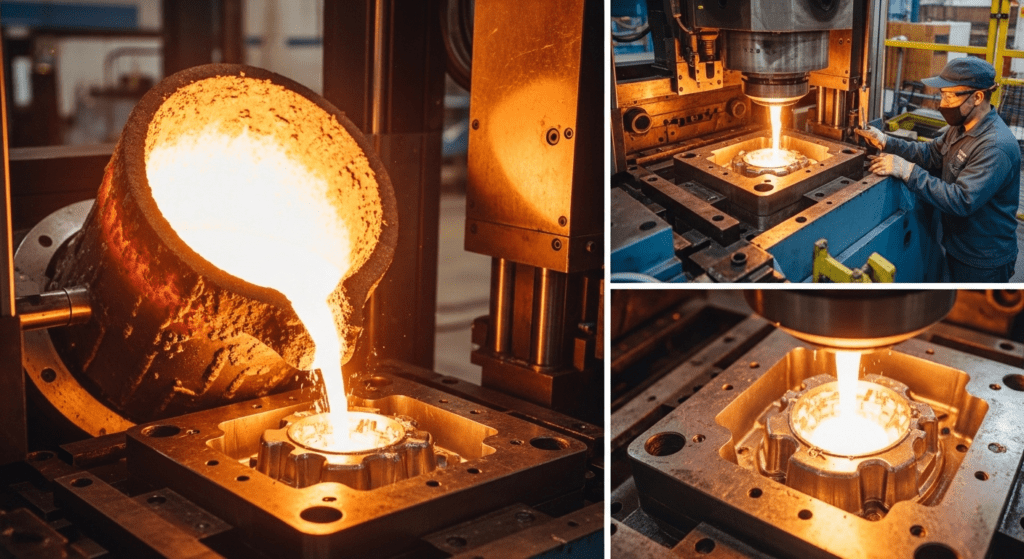
Die Casting Materials
The three main die casting metals for cars are zinc, aluminum, and magnesium. Each metal suits specific applications and performance requirements.
Zinc
Zinc melts at 787°F, the lowest temperature of common die casting metals. This low melting point saves energy and extends die life.
Zinc alloys offer the highest strength of all die casting materials. Parts can handle loads up to 60,000 PSI without breaking.
The metal flows easily into thin sections as small as 0.02 inches. This property lets manufacturers create intricate decorative trim and small mechanical parts.
Zinc costs more per pound than aluminum but requires less energy to process. The total manufacturing cost often equals or beats aluminum for small parts.
Aluminum
Aluminum makes up 80% of all automotive die castings by weight. The metal combines light weight with good strength and corrosion resistance.
Aluminum parts weigh 65% less than steel components of the same size. This weight savings improves fuel economy by 6-8% in modern vehicles.
The metal withstands temperatures up to 300°F in engine applications. Aluminum also conducts heat well, making it ideal for radiators and heat sinks.
Common aluminum car parts include engine blocks, transmission housings, wheels, and suspension components. A typical car contains 300-400 pounds of aluminum castings.
Magnesium
Magnesium is the lightest structural metal used in die casting. Parts weigh 33% less than aluminum and 75% less than steel.
Car makers use magnesium for instrument panels, steering wheels, and seat frames. These parts reduce vehicle weight without sacrificing safety.
The metal machines easily after casting, allowing precise final dimensions. Magnesium also dampens vibrations better than aluminum or steel.
Processing magnesium requires special safety equipment because the metal can burn. Despite this challenge, usage grows 15% annually as automakers pursue weight reduction goals.
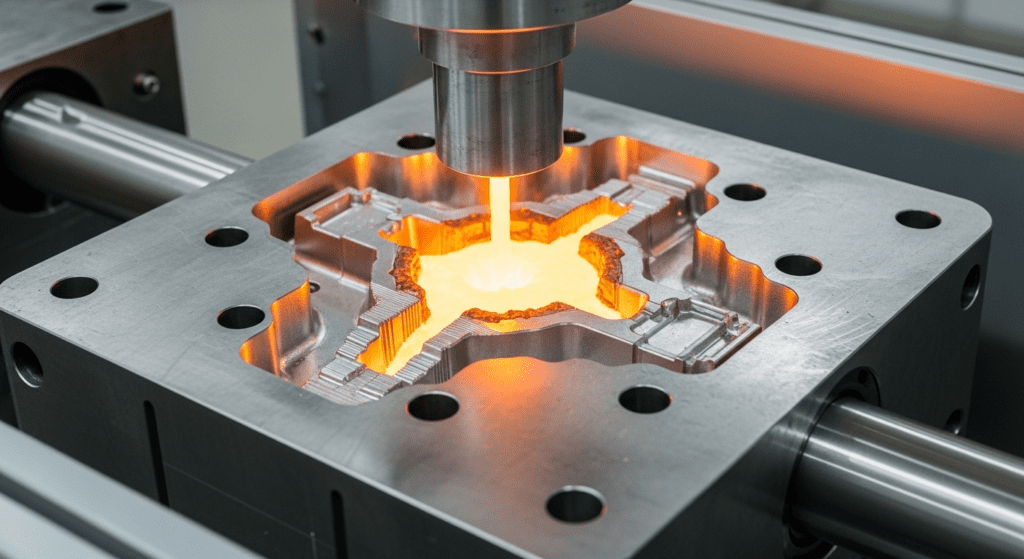
Advantages of Die Casting in Automotive
High Precision and Surface Quality
Die casting achieves tolerances as tight as ±0.002 inches without additional machining. Parts emerge from molds with smooth surfaces that often need no finishing beyond trimming.
Complex Geometry & Thin Walls
Modern die casting creates walls as thin as 0.5mm while maintaining structural integrity. Engineers can design parts with internal passages, undercuts, and complex curves impossible with other methods.
Lightweight, High-Strength Parts
Die-cast parts offer strength-to-weight ratios superior to many other manufacturing methods. An aluminum die-cast engine block weighs 50% less than cast iron while maintaining comparable strength.
High Production Rates and Consistency
Automated die casting systems produce 500-1,000 parts per hour with minimal variation. Each part matches specifications within thousandths of an inch.
Material Efficiency and Recycling
Die casting generates minimal waste, with material utilization rates exceeding 95%. Excess metal from gates and overflows returns directly to the melting furnace.
Dimensional Accuracy and Assembly Fit
Parts maintain their dimensions throughout temperature changes and mechanical stress. This stability ensures doors close properly and engines run smoothly over the vehicle’s lifetime.
Cost-Effectiveness for Complex Parts
While die casting molds cost $50,000-$500,000, they produce millions of parts before replacement. The per-part cost drops dramatically with volume.
Automotive Application Examples
Modern vehicles contain dozens of die-cast components throughout their systems. Here are the main applications:
- Engine and Powertrain – Engine blocks, cylinder heads, oil pans, and valve covers use aluminum die casting for weight reduction and heat dissipation
- Transmission and Drivetrain – Transmission housings, clutch housings, and differential cases require the strength and precision of die-cast aluminum
- Suspension and Structural Parts – Control arms, steering knuckles, and shock towers benefit from die casting’s ability to create complex, load-bearing shapes
- Body and Chassis Components – Door frames, lift gate inner panels, and instrument panel supports use die casting for dimensional stability
- Electrical/Electronic Housings – ECU housings, connector bodies, and motor housings protect sensitive electronics with die-cast aluminum’s EMI shielding properties
- HVAC and Brake Components – Compressor housings, brake calipers, and master cylinders require die casting’s pressure resistance and thermal management capabilities