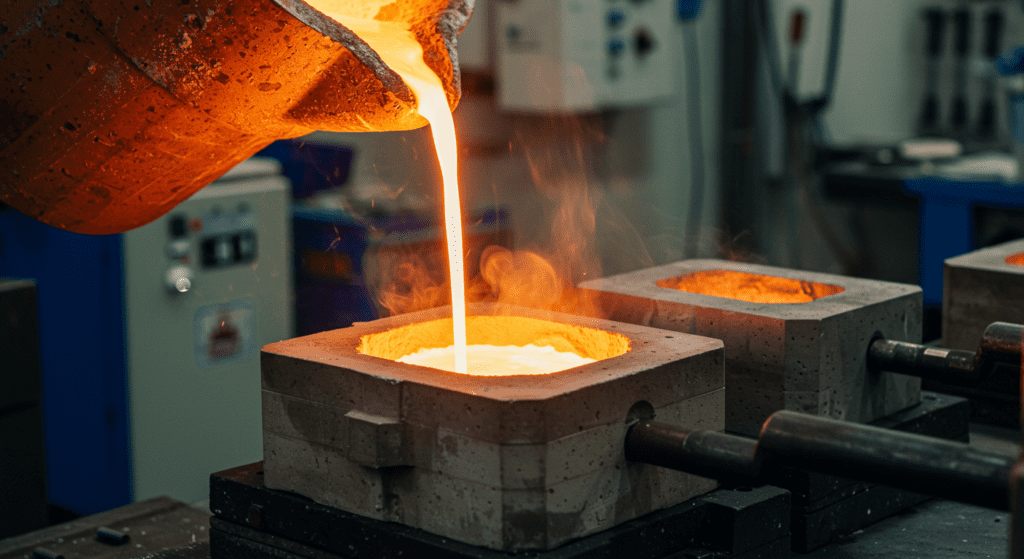
Casting
Metal casting is a manufacturing process where metal or alloy is heated above its melting point until completely liquefied, then poured into a mold with a cavity that corresponds to the negative geometric shape of the target part. The molten metal fills the cavity, cools and solidifies, forming the shape defined by the mold. After solidification, the metal object (called a casting) is removed from the mold. Subsequent machining operations are typically required to remove excess material and achieve final specifications.
The casting process allows for the creation of complex geometries, including internal cavities and channels that would be difficult to produce using other manufacturing methods. Common casting techniques include sand casting, die casting, investment casting, and permanent mold casting.
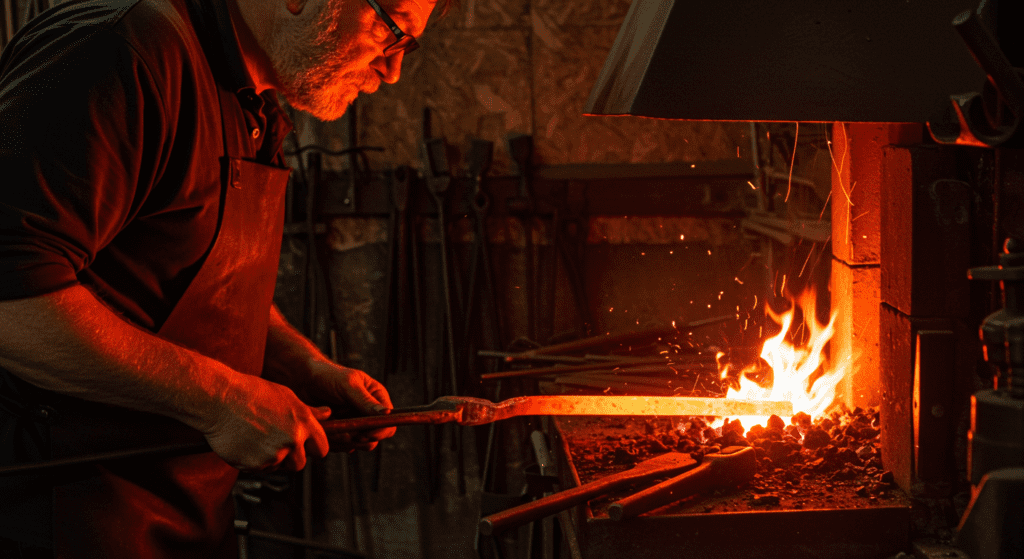
Forging
Forging is a manufacturing process fundamentally different from casting, utilizing localized compressive forces to shape solid metal. These forces are typically applied through hammering (using manual or powered hammers), pressing (using hydraulic or mechanical presses), or rolling. While the metal is often heated to high temperatures (hot forging or warm forging) to increase its plasticity and reduce the required deformation forces, it must be noted that forging never melts and pours the metal like casting does. The core principle of forging is the plastic deformation of solid material.
Forging can be classified into several types based on the equipment and technique used: open-die forging, closed-die forging, roll forging, and precision forging. The forging process typically begins with a simple starting shape (like a billet, bar, or ingot) that is progressively worked into the desired final form.
Difference between casting and forging
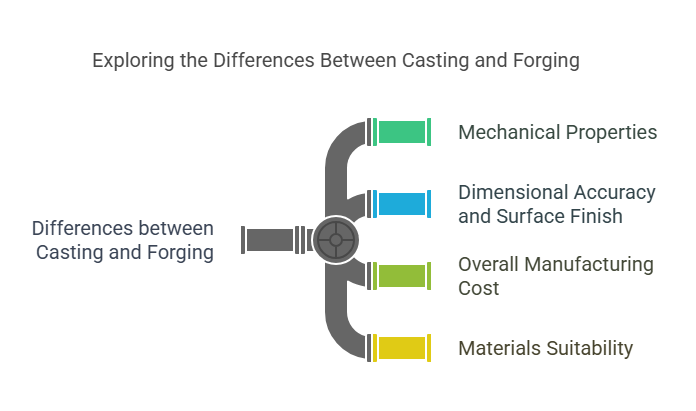
Mechanical Properties
Grain Structure
- Casting: During solidification, metal forms a dendritic grain structure as crystals grow from multiple nucleation points. This creates relatively coarse, equiaxed grains (similar dimensions in all directions) that provide consistent but moderate strength.
- Forging: The plastic deformation inherent in the forging process fundamentally alters the grain structure. It breaks down the initial cast structure of the starting material, resulting in refined, significantly finer grain structures. Forging imparts a distinctive directional grain flow or fibrous structure to the material, where grains are elongated and aligned parallel to the direction of major deformation or metal flow. This results in anisotropic (direction-dependent) properties that can be engineered for specific performance requirements.
Strength
- Casting: Due to potentially coarser grain structures and the possibility of internal defects acting as stress concentrators, cast components typically exhibit lower tensile and yield strength compared to forged components of the same material. Their strength is usually uniform in all directions (isotropic). Cast parts are more prone to failure under impact loading, especially when they have inherent brittleness or contain defects.
- Forging: Forging significantly enhances strength properties. Forged parts demonstrate substantially improved tensile strength (reported to be 26% higher than castings), yield strength (also 26% higher), and excellent impact strength or toughness. These strength improvements are attributed to fine grain structures and elimination of internal defects. However, strength is anisotropic, being highest in directions parallel to grain flow.
Ductility and Toughness
- Casting: Cast materials have lower ductility (ability to plastically deform before fracture) and toughness (ability to absorb energy and resist fracture) compared to forged materials. They are more susceptible to brittle fracture, especially when defects like porosity or inclusions are present, which can serve as initiation points for cracks.
- Forging: The structures produced by forging typically exhibit excellent ductility and toughness. Forged parts may undergo significant deformation before failure. When tested, forged parts reduce in area by approximately 58% when pulled to failure, compared to only 6% for castings. This dramatic difference demonstrates the superior ability of forged components to absorb energy before fracturing.
Fatigue Resistance
- Castings: Castings generally have lower fatigue strength (ability to resist failure under cyclic loading) compared to forgings. This reduced performance is attributed to coarser grain structures and potentially present internal defects such as porosity and inclusions, which can serve as stress concentrators and crack initiation sites under cyclic loading conditions.
- Forgings: Forgings demonstrate excellent fatigue resistance. The fine, uniform grain structure, favorable alignment of grain flow (which can block crack propagation through grains), and absence of internal defects significantly enhance the ability of forged components to withstand repeated stress cycles. Under similar conditions, forged parts can withstand up to 50% more fatigue cycles than cast parts, making them ideal for critical applications subject to dynamic loading.
Wear Resistance
- Castings: The wear resistance of castings largely depends on the specific alloy used. Some specialized casting alloys can offer good wear resistance for certain applications. However, variations in microstructure and the potential presence of defects can compromise performance.
- Forgings: The dense, uniform structure and fine, well-aligned grain flow typically confer excellent wear resistance to forged components. The compression during forging eliminates porosity, creating a fully dense material that can better withstand abrasive and adhesive wear mechanisms. The improved hardness resulting from work hardening during forging also contributes to superior wear performance.
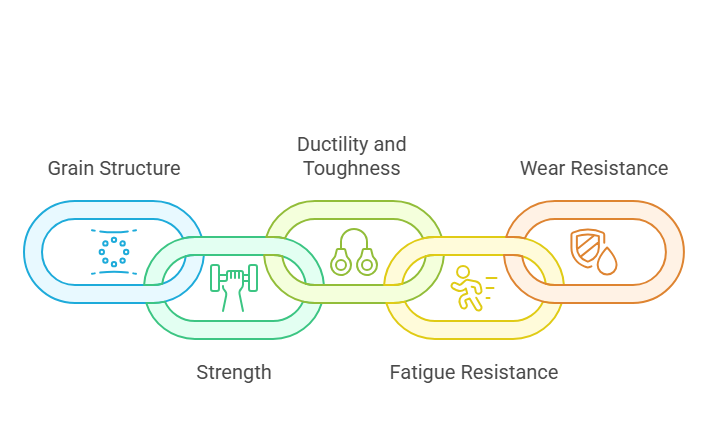
Dimensional Accuracy and Surface Finish
- Casting: The precision and surface finish achievable varies greatly among different casting methods. Die casting and investment casting are known for producing parts with excellent dimensional tolerances and surface finish, typically requiring minimal post-processing. Permanent mold casting also offers good precision and finish, superior to sand casting. Among common methods, sand casting typically results in the lowest dimensional precision and roughest surface finish, usually requiring significant machining allowances. Shell molding and plaster casting can provide moderate levels of precision and finish.
- Forging: Typically provides good to excellent dimensional precision and surface finish, often superior to sand casting. Cold forging produces the best results in terms of tight tolerances and smooth surfaces. Precision forging techniques are designed to produce near-net shapes requiring little or no machining. However, even forged parts may require final machining to meet very tight tolerances or achieve specific surface characteristics.
Overall Manufacturing Cost
- Casting: Total cost largely depends on the casting method, material, complexity, and production volume. Sand casting is very cost-effective for prototypes or small production runs due to low mold costs. Die casting, despite high initial tooling costs, is highly cost-effective for mass production of complex parts due to high speed and minimal finishing. Investment casting, due to its complexity and labor intensity, is typically one of the more expensive casting processes.
- Forging: Generally considered to have higher initial costs due to expensive dies, especially for closed-die processes. However, it can become cost-effective for medium to large production runs as tool costs are amortized. Material costs can be higher due to the need for forging-quality starting stock.
Materials Suitability
- Casting: Casting processes offer high flexibility in material selection, capable of handling various ferrous (iron-based) and non-ferrous metal alloys. The primary requirement is that the material can be effectively melted and poured. This makes casting particularly suitable for materials with high melting points, low ductility, or complex compositions. Casting can effectively process alloys that might be difficult to forge, such as high-silicon aluminum alloys, cast irons, and certain high-temperature superalloys.
- Forging: While technically most metals can be forged under proper conditions, the process is most commonly used for materials that exhibit good plasticity (ductility and malleability) when heated, allowing them to deform under compressive forces without fracturing. Common forged materials include carbon and alloy steels, stainless steels, aluminum alloys, copper alloys, nickel alloys, and titanium alloys.