The key difference between continuous casting and centrifugal casting lies in how they shape molten metal. Continuous casting creates long, uniform products by pouring metal through a mold continuously. Centrifugal casting spins a mold at high speed to force metal against the walls, creating hollow cylindrical parts.
Each method serves distinct manufacturing needs—continuous casting excels at mass-producing simple shapes like steel beams, while centrifugal casting produces high-quality pipes and tubes with superior density.
What Is Continuous Casting
Continuous casting transforms molten metal into solid shapes through a non-stop pouring process. The metal flows from a furnace into a water-cooled mold that shapes it into specific cross-sections.
As the metal moves through the mold, it gradually solidifies from the outside in. The partially solidified metal strand exits the mold bottom and passes through cooling sprays.
Rollers guide and support the strand as it completes solidification. The process runs continuously, producing lengths limited only by handling equipment.
Most importantly, this method creates consistent products with minimal waste. Steel mills use it to make slabs, billets, and blooms—the building blocks for construction beams, railroad tracks, and automotive parts.
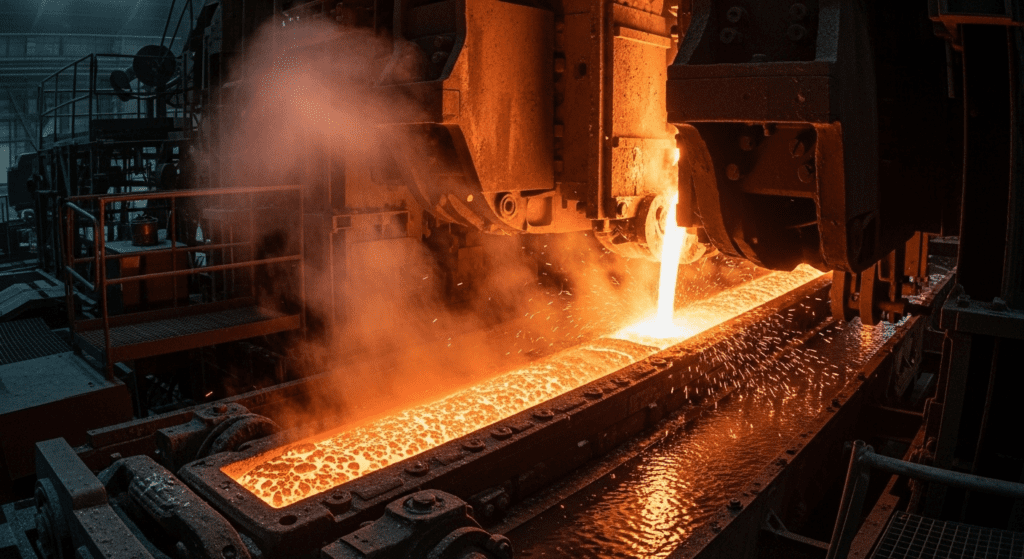
What Is Centrifugal Casting
Centrifugal casting uses rotational force to create hollow metal parts with exceptional strength. The process begins by spinning a mold at speeds between 300 to 3,000 RPM.
Molten metal pours into the center of the spinning mold. Centrifugal force drives the metal outward against the mold walls.
The rotation continues as the metal cools and solidifies. Heavier impurities migrate to the inner surface, where they can be machined away later.
This method produces parts with fine grain structure and high density. The outer surface achieves excellent detail and smoothness.
Manufacturers use centrifugal casting for pipes, cylinder liners, and bearing bushings. The process works with various metals including steel, iron, aluminum, and bronze.
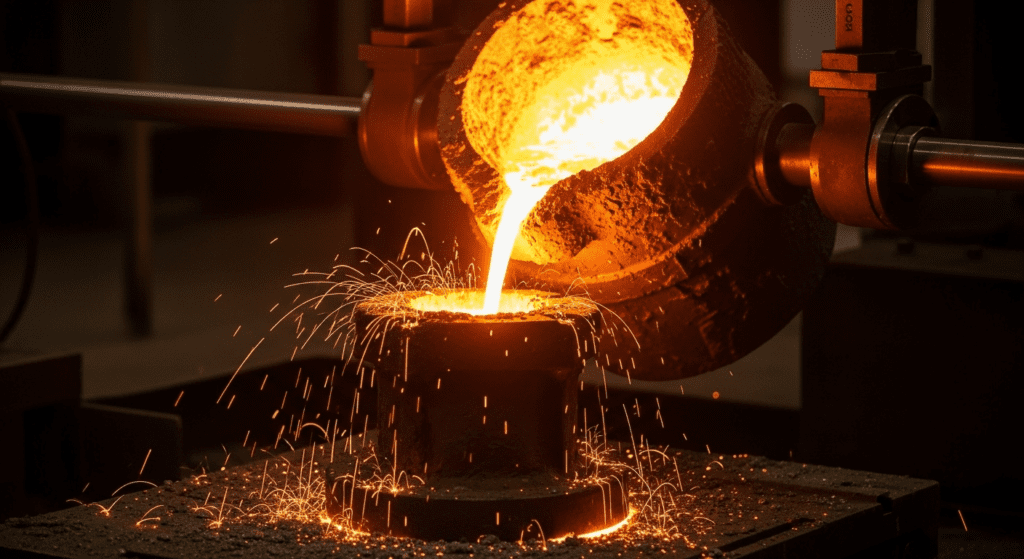
The Difference Between Continuous Casting and Centrifugal Casting
Principle
Continuous casting relies on gravity and controlled cooling to form products. Molten metal flows downward through a mold while solidifying gradually.
Centrifugal casting uses rotational force as its primary shaping mechanism. The spinning action distributes metal evenly and compacts it against mold walls.
Product Types
Continuous casting produces long, straight products with uniform cross-sections. These include rectangular slabs, square billets, and round blooms.
Centrifugal casting creates hollow cylindrical parts exclusively. Common products include pipes, tubes, bushings, and rings. The process cannot produce solid shapes or non-cylindrical geometries effectively.
Surface Quality
Continuous casting typically produces rougher surfaces that require additional processing. Scale formation and mold marks are common issues.
Centrifugal casting achieves superior surface quality. The high forces create smooth, dense surfaces with minimal defects. Many centrifugally cast parts need little to no machining on their outer surfaces.
Production Speed
Continuous casting operates at steady speeds ranging from 0.5 to 6 meters per minute. A single strand can run continuously for weeks.
Centrifugal casting works in batches. Each part requires separate pouring, spinning, and cooling cycles. Cycle times range from minutes to hours depending on part size and thickness.
Material
Continuous casting primarily handles steel and aluminum alloys. The process suits materials with good fluidity and controlled solidification characteristics.
Centrifugal casting accommodates a broader range of materials. It successfully casts iron, steel, aluminum, copper, and even exotic alloys. The rotational force helps distribute difficult-to-cast materials evenly.
Cost
Continuous casting requires massive initial investments in equipment and infrastructure. However, operating costs per ton are low due to high production volumes.
Centrifugal casting equipment costs less initially. The process suits smaller production runs economically. However, per-part costs exceed continuous casting for high-volume production. Labor costs are higher due to the batch nature of production.
Energy Consumption
Continuous casting uses energy efficiently through its continuous operation.
Centrifugal casting requires repeated heating cycles and motor power for rotation.