The main difference between die casting and investment casting is the mold material and process. Die casting uses reusable metal molds and injects molten metal under high pressure. Investment casting uses wax patterns and ceramic molds, producing more intricate parts but at higher cost and longer cycle times.
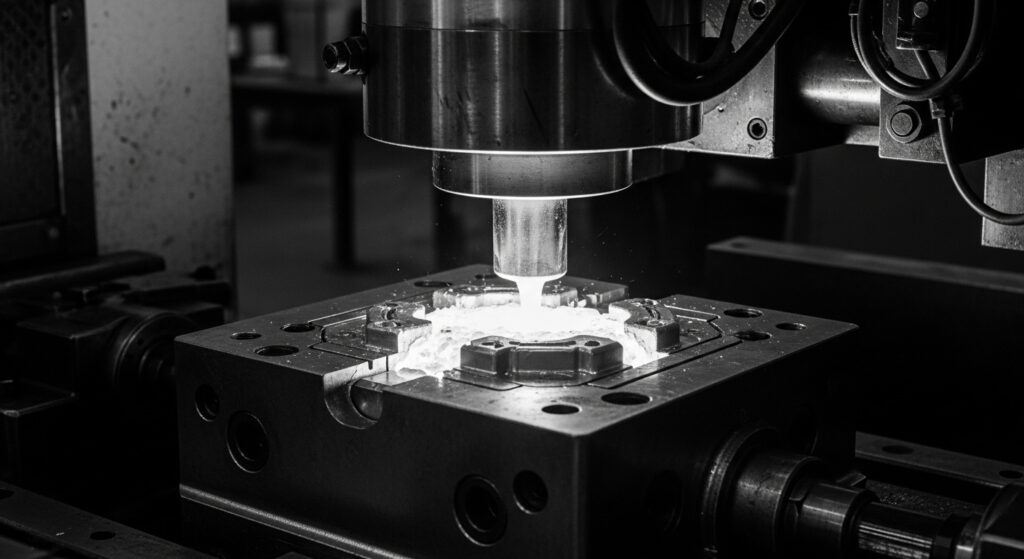
Die Casting
Die casting forces molten metal into hardened steel molds under extreme pressure. The metal solidifies quickly inside these permanent molds, creating parts with excellent dimensional accuracy and smooth surfaces.
This process works best with non-ferrous metals like aluminum, zinc, and magnesium. These metals have lower melting points that work well with steel dies. The dies themselves cost thousands of dollars to machine, but they can produce hundreds of thousands of parts before wearing out.
Die Casting Process
1. Mold Preparation
Workers clean the die halves and spray them with lubricant. The die then clamps shut under tremendous force – often several hundred tons.
2. Metal Melting and Preparation
The chosen metal melts in a furnace. The molten metal transfers to a holding furnace that maintains the exact temperature needed for casting.
3. Injection
The machine shoots molten metal into the die at speeds up to 60 miles per hour. Pressure ranges from 1,500 to 25,000 PSI.
4. Cooling and Solidification
The metal cools rapidly inside the water-cooled die. The die stays clamped during this entire cooling phase.
5. Ejection
Once solid, the die opens. Ejector pins push the part out of the mold. The part often comes out with excess metal called flash, which forms where the die halves meet.
6. Trimming
Workers remove the flash and any excess material from gates and runners.
Investment Casting
Investment casting creates metal parts through a completely different approach. Instead of permanent molds, this process uses disposable ceramic shells formed around wax patterns. It excels at producing parts with intricate details that would be impossible to machine.
Investment casting trades speed for versatility and precision. While die casting cranks out parts by the thousands, investment casting focuses on smaller batches of complex components.
Investment Casting Process
1. Pattern Creation
Everything starts with a wax pattern. Manufacturers inject molten wax into aluminum dies to create exact replicas of the desired part.
2. Pattern Assembly
Multiple wax patterns attach to a central wax rod called a sprue. This creates a “tree” structure.
3. Shell Building
The wax tree gets dipped into ceramic slurry, then coated with fine sand. This process repeats 5-10 times over several days. Each layer must dry completely before adding the next. The result is a ceramic shell about 1/4 to 1/2 inch thick.
4. Wax Removal
The ceramic-coated assembly goes into a steam autoclave. High-pressure steam melts the wax in minutes, leaving a hollow ceramic mold.
5. Mold Firing
The empty ceramic shell needs strengthening before it can hold molten metal. Furnaces heat the shells to 1800-2000°F. This process burns out any remaining wax residue and transforms the ceramic into a strong, stable mold.
6. Metal Pouring
Molten metal flows into the hot ceramic mold through gravity. The mold might sit in a bed of sand for support during pouring.
7. Cooling
The filled molds cool slowly at room temperature.
8. Shell Removal
Once cool, the ceramic shell breaks away easily. Methods include vibration, water jets, or simple hammering.
9. Finishing
Individual parts are cut from the tree using saws or cutting wheels. Gates and attachment points need grinding to final dimensions.
The Difference Between Die Casting and Investment Casting
Attribute | Die Casting | Investment Casting |
---|---|---|
Mold Type & Life | Reusable hardened steel dies; 100,000 to millions of shots | Expendable ceramic shell (new mold per cast); master pattern die for wax patterns is reusable |
Material Compatibility | Primarily non-ferrous (Al, Zn, Mg, Cu alloys) ; Ferrous metals generally unsuitable | Ferrous (steels, stainless, Co alloys) & non-ferrous (Al, Ni alloys, Ti alloys, Cu alloys); high-temp/exotic alloys |
Design Complexity | Good for intricate shapes, thin walls; undercuts require complex dies (slides/cores) | Excellent for highly complex/intricate geometries, undercuts, internal passages; greater design freedom |
Dimensional Accuracy | Excellent; ISO CT4-CT6 ; Tolerances down to ±0.005 in. | Excellent; ISO CT5-CT7 ; Tolerances ±0.010in. (1st inch)}, ±0.004 in. (succ. inch) |
Surface Finish (Ra) | Good to excellent; 0.8−3.2 µm (125 µin) ; Parting lines present | Excellent; 1.6−6.3 µm (63−250 µin) ; No parting lines or flash |
Tooling Cost | High initial cost for steel dies | Lower initial cost for master pattern die; ongoing cost for ceramic shell materials |
Production Volume | Ideal for high volume (tens of thousands to millions) | Ideal for low to medium volume |
Per-Part Cost | Very low at high volumes | Higher, especially at high volumes; can be offset by reduced machining |
Production Speed/Cycle Time | Very fast (seconds to minutes per shot) | Slower (multiple steps; 50-100 castings/hr) |
Overall Lead Time | Long for initial tooling; fast for part production | Longer for part production (4-6+ weeks) due to multi-step process |
Max Part Size/Weight | Small to medium parts; limited by machine/die size | Ounces up to 100s of lbs (specialized >1000 lbs); optimal 0.01-20kg |
Common Defects | Gas porosity, misruns, cold shuts | Shrinkage, porosity, inclusions, misruns, deformation |
Post-Processing Needs | Flash/gate removal; may need machining for tightest specs or finish | Gate removal; often minimal to no machining needed due to near-net shape and finish |
Wall Thickness | Capable of very thin walls | Capable of thin walls, but very thin (<0.5mm) can be challenging for wax pattern |