The main difference between gravity die casting and high-pressure die casting is the force used to fill molds. Gravity die casting uses gravity to fill the mold slowly, while high-pressure die casting forces molten metal into the mold at high pressure for faster, more detailed production.
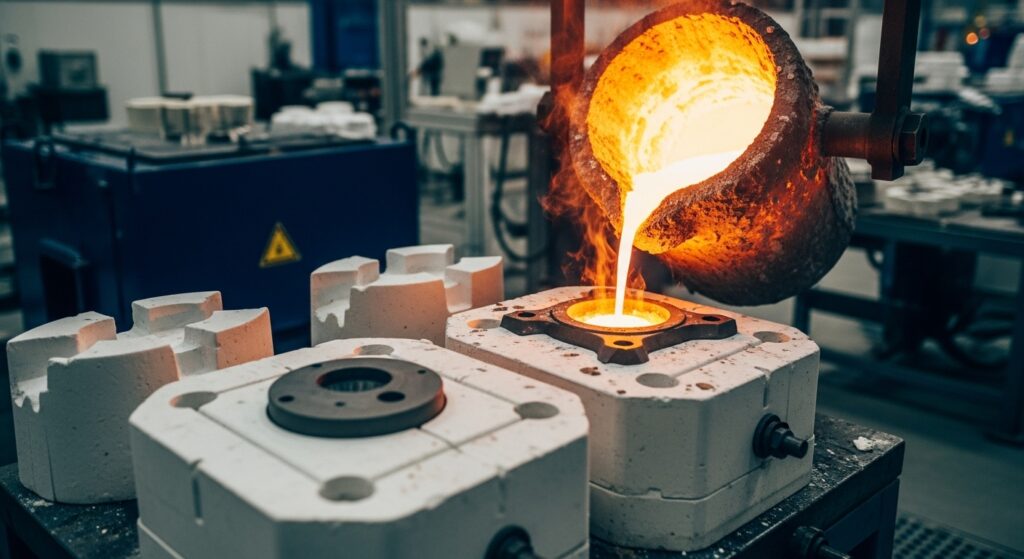
High-Pressure Die Casting
High-pressure die casting forces molten metal into a steel mold cavity under extreme pressure, typically between 1,500 and 25,000 psi. This manufacturing process creates complex metal parts with excellent surface finish and tight dimensional tolerances.
The process works best with non-ferrous metals like aluminum, zinc, and magnesium. These metals have lower melting points that make them ideal for rapid production cycles.
High-Pressure Die Casting Process
- Mold preparation: The process begins with a die made of two halves of hardened tool steel, which are mounted onto the platens of a die casting machine. The internal surfaces are sprayed with a lubricant or release agent to aid in part ejection and manage die temperature. The machine then closes the die, clamping it shut with immense hydraulic or mechanical force, which is necessary to counteract the subsequent injection pressure.
- Metal injection: A precisely metered quantity of molten metal, known as a “shot,” is transferred from a furnace into the machine’s shot chamber. From there, a powerful hydraulic piston forces the metal into the die cavity. This injection occurs at exceptionally high speeds and under pressures that can range from 1,500 psi to over 25,000 psi. The entire filling phase is incredibly swift, often completed in 10 to 100 milliseconds.
- Solidification: The metal cools and hardens inside the water-cooled mold. This cooling phase typically lasts 2 to 20 seconds.
- Ejection: As soon as the casting is solid, the die halves open, and a system of ejector pins pushes the casting, or “shot,” out of the die cavity. A single shot may contain multiple identical parts if a multi-cavity die is used.
- Finishing: Parts receive final touches like drilling, tapping, or surface treatments.
Gravity Die Casting
Gravity die casting uses the natural force of gravity to fill a permanent metal mold with molten metal. The process operates at much lower pressures than high-pressure die casting, relying only on the weight of the liquid metal.
This method works particularly well for aluminum and copper-based alloys. The slower filling speed allows better control over the metal flow and reduces turbulence.
Gravity die casting excels at producing parts with superior mechanical properties. The controlled cooling and minimal turbulence create stronger, more ductile components than high-pressure methods.
Gravity Die Casting Process
- Mold Preparation: The die is preheated to a specific temperature, often above 150°C. Following preheating, a refractory coating or a specialized release agent is applied to the internal surfaces of the die cavity.
- Pouring (Mold Filling): With the die securely clamped, molten metal—typically a non-ferrous alloy of aluminum, zinc, or copper—is gently poured from a crucible or ladle into a pouring basin integrated into the die design.
- Solidification: Once the cavity is filled, the molten metal begins to cool and solidify, transferring its heat to the surrounding metal die.
- Ejection: After the casting has fully solidified, the two halves of the die are opened, and the finished part is removed, often with the assistance of mechanical ejector pins.
- *Post-Processing: The final step involves trimming the excess material from the gates, runners, and risers.
The Difference Between Gravity Die Casting and High-Pressure Die Casting
Feature | Gravity Die Casting | High-Pressure Die Casting (HPDC) |
---|---|---|
Process Principle | Molten metal is poured and fills the die under the force of gravity. | Molten metal is injected into the die under high pressure and velocity. |
Pressure | Atmospheric pressure (gravity-fed). | 10 to 200 MPa (1,500 to 29,000 psi). |
Tooling Cost | Lower; dies are simpler and subject to less stress. | Higher; dies must be robust to withstand high pressures and injection forces. |
Production Rate | Slower; typically 15-30 cycles per hour. | Very fast; 50-90 cycles per hour, can be significantly higher for smaller parts. |
Part Size & Weight | Suitable for a wide range of sizes, including larger and heavier parts (up to 40 kg or more). | Best suited for small to medium-sized parts, typically up to 5 kg. |
Wall Thickness | Thicker walls are generally required, typically a minimum of 3-5 mm. | Capable of producing very thin walls, as low as 1.5 mm. |
Achievable Tolerances | Good, but generally less precise than HPDC. | Excellent; tighter tolerances can be achieved and maintained. |
Surface Finish (Ra) | Good; typically in the range of 4-10 μm. | Excellent; smoother surface finishes, often 1-4 μm. |
Porosity | Lower levels of porosity due to less turbulence during filling. | Higher potential for porosity due to entrapped air from high-speed injection. |
Mechanical Properties | Generally superior due to lower porosity and a more uniform grain structure. Parts can be heat-treated. | Mechanical properties can be compromised by porosity. Heat treatment is often not possible. |
Common Alloys | Aluminum, Zinc, Copper, and some cast irons. | Primarily non-ferrous alloys with lower melting points like Aluminum, Zinc, and Magnesium. |