The main difference between investment casting and gravity die casting is how the mold is formed and how metal fills it. Investment casting uses a wax model and ceramic mold, ideal for complex shapes. Gravity die casting uses reusable metal molds and gravity to fill them, offering faster production but less detail.
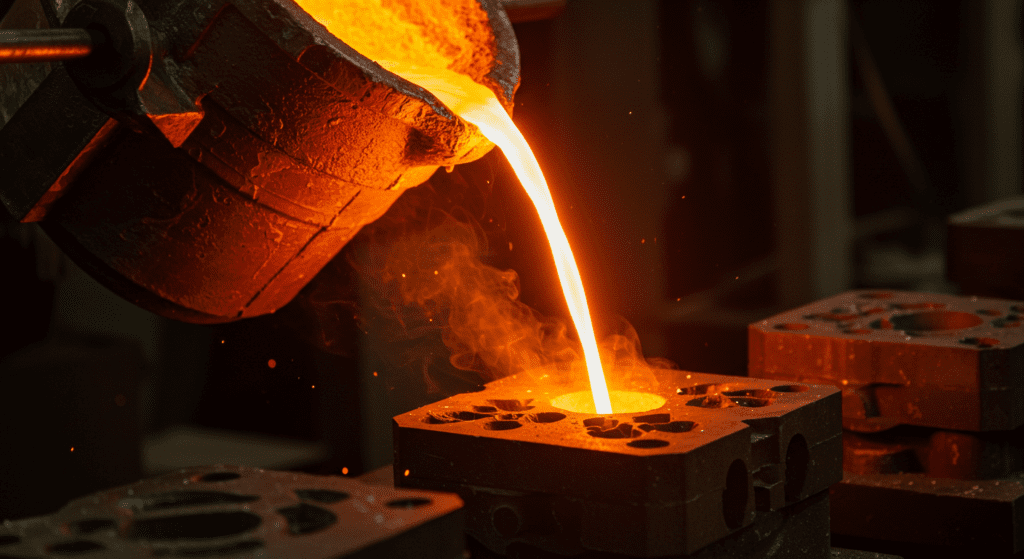
Investment Casting
Investment casting is a metal forming process that uses wax patterns to create detailed metal parts. You make a wax model of your part, coat it with ceramic material, then melt out the wax and pour molten metal into the hollow ceramic shell.
Investment casting produces parts with excellent surface finishes of 125-250 RMS. The process maintains tight tolerances of ±0.005 inches per inch. Parts can weigh from less than 1 ounce to over 200 pounds.
Gravity Die Casting
Gravity die casting uses permanent metal molds to produce metal parts by pouring molten metal directly into the cavity. The metal flows into the mold using only gravity – no external pressure is applied.
Manufacturers typically use steel or cast iron to make these reusable molds. Each mold can produce 50,000 to 100,000 parts before replacement.
Gravity die casting creates parts with good dimensional accuracy of ±0.010 inches. Surface finish ranges from 250-350 RMS. The process suits medium to high production volumes of 1,000 to 50,000 parts annually.
The Difference Between Investment Casting and Gravity Die Casting
Decision Criterion | Investment Casting | Gravity Die Casting |
---|---|---|
Material Selection | Excellent: Can cast almost any alloy, including ferrous (steels), non-ferrous, and high-temperature superalloys. The only choice for steel or nickel/cobalt alloys. | Limited: Restricted to non-ferrous alloys with melting points lower than the steel die, primarily aluminum, zinc, and copper alloys. |
Geometric Complexity | Excellent: Unmatched capability for intricate shapes, internal passages, undercuts, and features requiring zero draft. | Good: Suitable for moderately complex parts but limited by the need for die separation and draft angles. Less capable of producing complex internal features. |
Dimensional Accuracy | Excellent: A precision process delivering very tight tolerances (near-net-shape), minimizing the need for machining. | Good: Offers good, repeatable accuracy superior to sand casting, but generally with looser tolerances than investment casting. |
Surface Finish | Excellent: Produces the best as-cast surface finish, often eliminating the need for secondary polishing or finishing operations. No parting lines. | Good: Provides a smooth surface finish superior to sand casting but typically requires some post-processing to match investment casting. Will have a parting line. |
As-Cast Mechanical Properties | Good: Properties are dependent on the alloy. Slower cooling can lead to a coarser grain structure compared to gravity die casting for the same non-ferrous alloy. | Excellent: Rapid cooling in the metal die produces a fine-grained, dense structure, resulting in superior as-cast strength and hardness. Ideal for heat treatment. |
Tooling Cost | Low: Lower upfront cost for the wax pattern die. | Moderate-High: Higher upfront cost for the durable, reusable steel die. |
Per-Unit Cost (High Volume) | High: Labor-intensive process leads to higher unit costs that do not decrease as significantly with volume. | Low: High automation potential and amortization of tooling costs lead to very low unit costs at high volumes. |
Optimal Production Volume | Low-to-Medium: Ideal for prototypes, short runs, and quantities typically under a few thousand parts. | Medium-to-High: Most economical for production runs from several hundred into the tens of thousands of parts. |
Cycle Time | Slow: The multi-day process of shell building and drying results in a long cycle time per batch. | Fast: Once the tool is ready, the casting cycle is measured in minutes, allowing for high daily output. |