The main difference between investment casting and permanent mold casting is the mold type and application. Investment casting uses disposable ceramic molds for high-detail parts and complex shapes. Permanent mold casting uses reusable metal molds for faster production and stronger, less intricate parts.
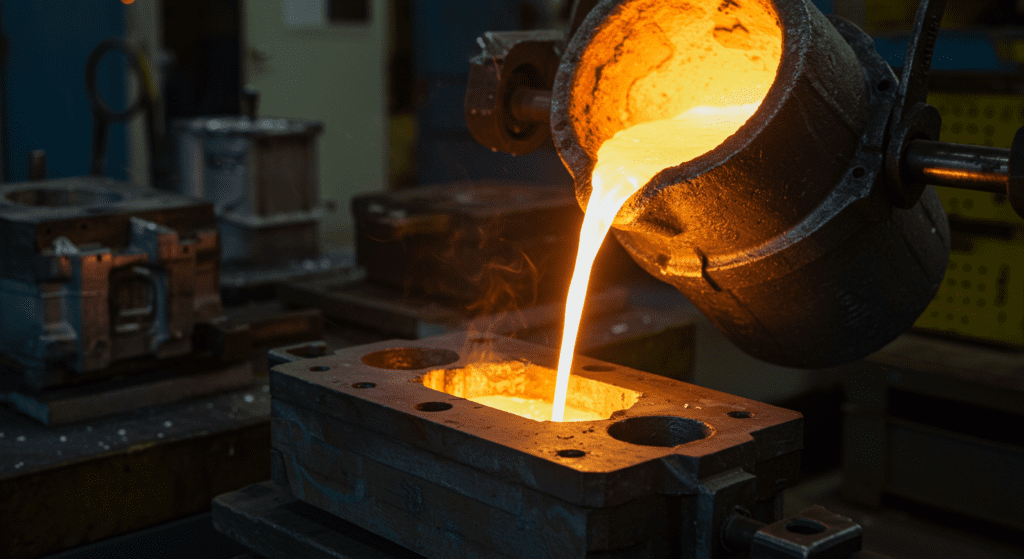
Investment Casting
Investment casting, also known historically as “lost-wax casting,” utilizes a disposable mold for each casting cycle. The process involves creating a shell, typically made of ceramic, around a sacrificial wax pattern that is an exact replica of the final part. After the molten metal is poured and solidifies, this ceramic shell is intentionally destroyed—broken away from the casting—to retrieve the finished component.
Because the mold is created anew for every part and is not required to be opened or preserved, it can be formed around geometries of almost limitless complexity.
Investment Casting Process
Step 1: Create the Wax Pattern
Workers inject liquid wax into aluminum dies to create exact replicas of the final part. Each wax pattern represents one finished casting. The dies maintain dimensional accuracy within 0.002 inches.
Step 2: Assemble the Wax Tree
Technicians attach multiple wax patterns to a central wax runner system called a tree. A single tree holds between 10 to 100 patterns.
Step 3: Build the Ceramic Shell
The wax tree gets dipped into ceramic slurry, then coated with fine sand particles. This dipping and coating process repeats 5 to 10 times. Each layer needs 2 to 4 hours to dry completely.
Step 4: Remove the Wax
The ceramic shell enters an autoclave heated to 200°F to 375°F. Steam pressure melts out all the wax in 10 to 30 minutes.
Step 5: Pour the Metal
Foundry workers heat the ceramic mold to 1,000°F to 2,000°F before pouring. Molten metal flows into every cavity detail.
Step 6: Break Out the Castings
After cooling for 30 minutes to 3 hours, workers break away the ceramic shell. Individual castings get cut from the tree using saws or cutting torches. Final cleaning removes any remaining ceramic material.
Permanent Mold Casting
Permanent mold casting uses reusable metal molds to produce aluminum, magnesium, and copper alloy parts. The steel or iron molds last for 10,000 to 120,000 castings before replacement. This process creates parts with wall thicknesses from 0.1 to 0.5 inches. In each cycle, the mold is closed, filled with molten metal, opened to eject the solidified part, and then prepared for the next pour.
Permanent Mold Casting Process
Step 1: Prepare the Mold
Operators preheat the steel mold to 300°F to 700°F using gas burners or electric heaters. They spray the cavity surfaces with graphite or ceramic coating.
Step 2: Close the Mold
Hydraulic or mechanical systems clamp the mold halves together with 10 to 50 tons of force. Proper alignment ensures parting line accuracy within 0.002 inches. Any cores get positioned before final closure.
Step 3: Pour the Metal
Molten metal enters the mold through gravity or low-pressure systems. Gravity pouring fills the mold in 3 to 30 seconds. Low-pressure systems use 2 to 15 psi of air pressure for better control.
Step 4: Cool the Casting
The casting solidifies in 30 seconds to 5 minutes. Water cooling channels in the mold accelerate this process.
Step 5: Open the Mold
After complete solidification, the mold opens automatically. Ejector pins push the casting out of the cavity. The cycle time ranges from 1 to 10 minutes total.
Step 6: Trim the Casting
Workers remove gates, risers, and flash using trim presses or band saws. Most permanent mold castings need minimal finishing. The dimensional tolerance stays within ±0.015 inches without machining.
The Difference Between Investment Casting and Permanent Mold Casting
Feature | Investment Casting | Permanent Mold Casting |
---|---|---|
Mold Type | Single-use ceramic shell | Reusable metal mold (10,000-120,000 uses) |
Surface Finish | 63-125 RMS | 150-350 RMS |
Dimensional Tolerance | ±0.003 inches | ±0.015 inches |
Wall Thickness | 0.025-5.0 inches | 0.1-0.5 inches |
Part Weight | 0.1 oz to 200 lbs | 1 oz to 70 lbs |
Production Rate | 20-200 parts per day | 50-250 parts per hour |
Tooling Cost | $1,000-$25,000 | $15,000-$150,000 |
Part Complexity | Very complex with undercuts | Moderate complexity, limited undercuts |
Suitable Alloys | 100+ alloys including steel, titanium | Mainly aluminum, magnesium, copper alloys |
Typical Applications | Turbine blades, medical implants, valves | Pistons, cylinder heads, housings |
Cost Per Part | Higher ($5-$500) | Lower ($2-$50) |
Lead Time | 2-8 weeks | 4-12 weeks for tooling, then rapid production |