The main difference between investment casting and shell casting is the mold formation. Investment casting uses a wax pattern coated with ceramic, which is melted away before metal pouring. Shell casting builds a thin shell around the pattern using sand and resin, offering faster production but less intricate detail.
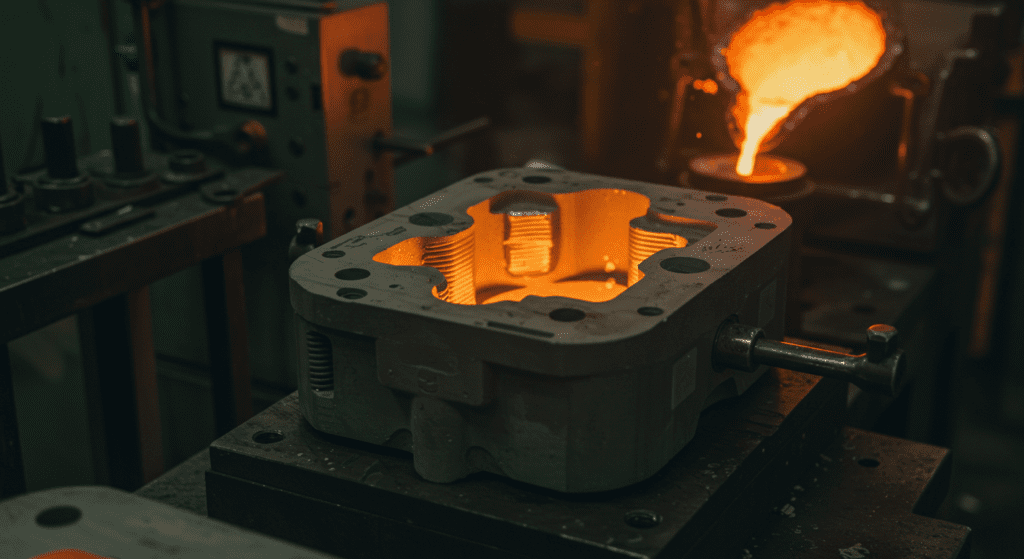
Investment Casting
Investment casting creates metal parts by pouring molten metal into a ceramic mold. This process produces complex shapes with excellent surface finishes and tight tolerances.
The process is fundamentally defined by its use of a sacrificial, or expendable, pattern that is an exact replica of the desired final part. This pattern, typically made of wax, is “invested,” or completely surrounded by, a refractory ceramic slurry. After the ceramic material hardens, the original wax pattern is melted out, leaving behind a hollow, one-piece ceramic mold with a precise negative cavity of the part’s geometry.
Investment Casting Process
Step 1: Create the Wax Pattern
The process starts by injecting wax into a metal die. This creates an exact replica of the final part. Multiple wax patterns can be attached to a central wax sprue, forming a tree-like assembly.
Step 2: Build the Ceramic Shell
Workers dip the wax assembly into a ceramic slurry. They then coat it with fine sand or stucco. This coating process repeats 5 to 15 times until the shell reaches the desired thickness.
Step 3: Remove the Wax
The ceramic shell goes into an autoclave or furnace heated to 200-375°F. The wax melts and drains out, leaving a hollow ceramic mold.
Step 4: Pour the Metal
The empty ceramic mold is preheated to 1,000-2,000°F. Molten metal fills the cavity through gravity or vacuum assistance.
Step 5: Break the Shell
After cooling, workers break away the ceramic shell using vibration or water blasting. The metal parts are cut from the sprue. Final finishing operations include grinding, machining, and heat treatment.
Shell Casting
Shell casting forms hollow parts by rotating liquid material inside a mold. The material spreads evenly across the mold’s inner surface through centrifugal force. This technique primarily works with plastics, resins, and some metals.
The core principle of this process is the use of a reusable, permanent metal pattern to create a disposable, thin-walled mold, or “shell”. This shell is not made of loose sand but is formed from a mixture of fine-grained sand and a thermosetting resin binder. When this mixture is applied to the hot metal pattern, the resin cures, bonding the sand grains into a rigid, strong, and smooth-surfaced shell.
Shell Casting Process
Step 1: Prepare the Mold
The process begins with a hollow mold made from metal or composite materials. The mold splits into two or more sections for easy part removal. Release agents coat the inner surface to prevent sticking.
Step 2: Add the Material
Operators pour a measured amount of liquid material into the mold. The quantity determines the final wall thickness. For thermoplastics, the material is heated to 350-450°F before pouring.
Step 3: Rotate the Mold
The mold rotates around two perpendicular axes simultaneously. Speeds typically range from 4 to 20 RPM. This rotation distributes the material evenly across all interior surfaces.
Step 4: Cool and Solidify
The mold continues rotating while the material cools and hardens. Cooling methods include air circulation, water spray, or cold chambers. This stage takes 10 minutes to several hours.
Step 5: Remove the Part
Once solidified, rotation stops and the mold opens. The hollow part releases easily due to minimal shrinkage stress. Any flash or excess material is trimmed away.
The Difference Between Investment Casting and Shell Casting
Aspect | Investment Casting | Shell Casting |
---|---|---|
Part Type | Solid metal parts with complex geometries | Hollow parts with uniform wall thickness |
Materials | Metals (steel, aluminum, titanium, bronze) | Plastics, resins, some metals |
Mold Type | Expendable ceramic shell | Reusable metal or composite mold |
Process Method | Molten metal poured into stationary mold | Material distributed by mold rotation |
Wall Thickness | Varies from 0.060 to 5 inches | Consistent thickness from 0.125 to 1 inch |
Surface Finish | 60-200 RMS | 100-300 RMS |
Tolerances | ±0.003 to ±0.005 inches per inch | ±0.010 to ±0.030 inches per inch |
Production Volume | Low to medium (1-10,000 parts) | Medium to high (100-100,000 parts) |
Tooling Cost | High ($5,000-$50,000) | Low ($1,000-$10,000) |
Lead Time | 4-8 weeks | 2-4 weeks |
Part Size | 0.1 ounces to 200 pounds | 1 pound to 2,000 pounds |
Design Limitations | Requires draft angles for wax removal | Limited to hollow shapes |