The main difference between sand casting and centrifugal casting is how the mold and metal interact. Sand casting uses static sand molds and gravity to form parts, while centrifugal casting spins a mold rapidly to force molten metal outward. Centrifugal casting produces denser, more precise parts with fewer impurities.
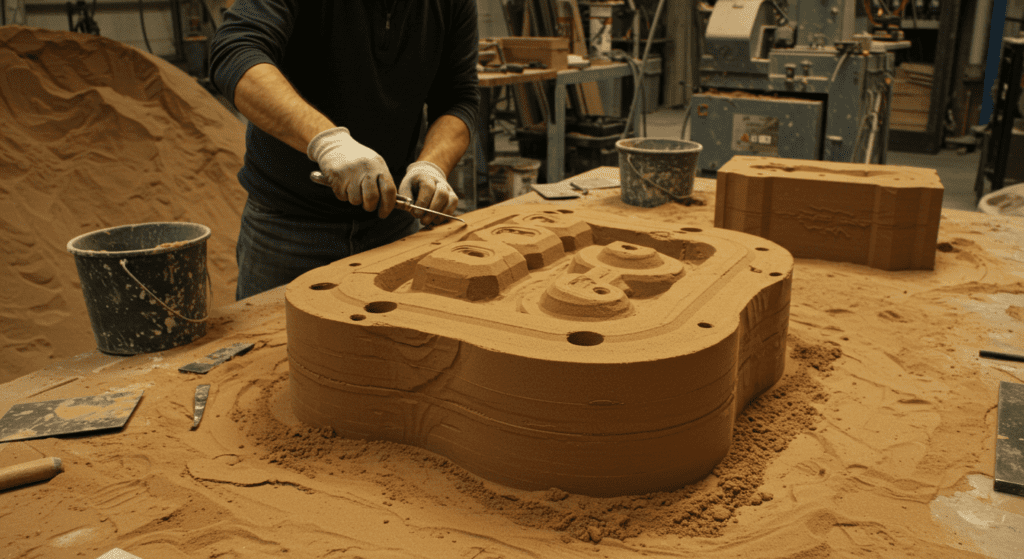
What Is Sand Casting
Sand casting is a metal casting process that uses a mold made of sand to form metal parts. The process involves packing sand around a pattern, removing the pattern, and pouring molten metal into the cavity. After cooling, the sand mold is broken to retrieve the cast object.
Sand Casting Process
- Pattern Making: Create a replica of the final part using wood, plastic, or metal.
- Mold Preparation: Pack special molding sand around the pattern in a two-part mold box called a flask. The sand mixture contains silica sand, clay, and water or chemical binders.
- Pattern Removal: Carefully remove the pattern to leave a cavity in the sand. Add channels called runners and gates to guide molten metal into the cavity.
- Core Placement: Insert sand cores if the part requires internal cavities or hollow sections. Cores are made separately and positioned before closing the mold.
- Mold Assembly: Close the two halves of the flask and secure them together. The parting line where the halves meet becomes visible on the final casting.
- Metal Pouring: Heat metal to its melting point (1,200°F for aluminum, 2,100°F for iron) and pour it into the mold through the sprue opening.
- Cooling and Solidification: Allow the metal to cool naturally.
- Shakeout: Break apart the sand mold to remove the solidified casting. The sand can be reclaimed and reused for future molds.
- Finishing: Remove excess material from gates and runners. Clean the casting surface through grinding, sandblasting, or machining.
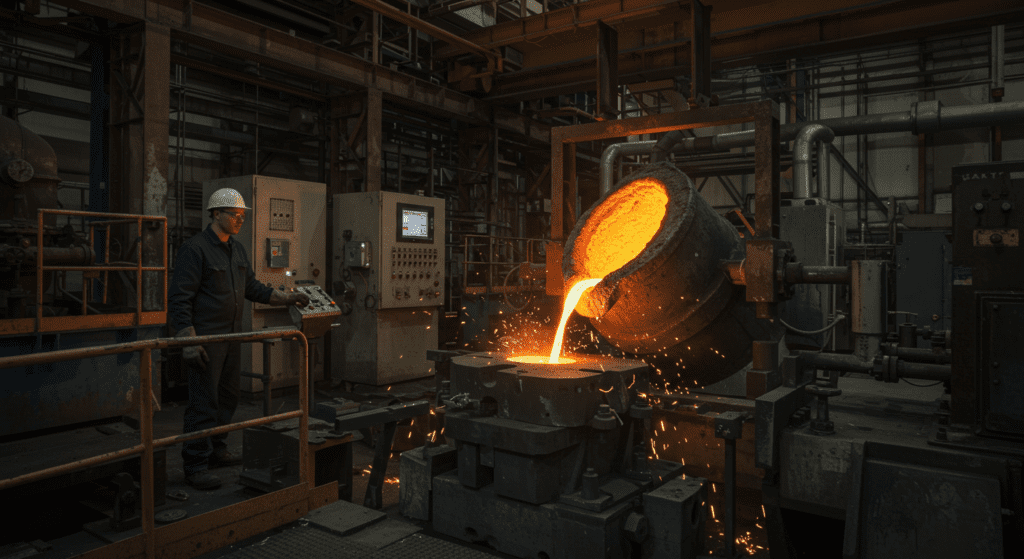
What Is Centrifugal Casting
Centrifugal casting is a metal casting process that uses high-speed rotation to distribute molten metal inside a mold. The centrifugal force pushes impurities to the center, allowing denser metal to form a strong, defect-free outer shell. It is commonly used to manufacture cylindrical components like pipes and bearings.
Centrifugal Casting Process
- Mold Preparation: Clean and coat the permanent mold with a refractory wash.
- Mold Heating: Preheat the mold to 300-500°F to prevent thermal shock and improve metal flow.
- Mold Mounting: Secure the mold on the spinning machine.
- Rotation Start: Begin rotating the mold at the calculated speed.
- Metal Pouring: Pour molten metal into the spinning mold through a trough or ladle. The metal immediately spreads along the mold walls due to centrifugal force.
- Continued Rotation: Maintain rotation during solidification.
- Cooling: Allow the part to cool while spinning. Some setups use water cooling on the mold exterior to speed solidification.
- Part Removal: Stop rotation after complete solidification. Extract the casting using mechanical pullers or hydraulic systems.
- Machining: Machine the inner and outer surfaces to final dimensions.
The Difference Between Sand Casting and Centrifugal Casting
Aspect | Sand Casting | Centrifugal Casting |
---|---|---|
Mold Preparation | Create expendable sand molds for each part. Process takes 30-60 minutes per mold | Use permanent metal or graphite molds. Initial setup takes days but molds last for thousands of parts |
Mechanical Properties | Lower overall strength and ductility. Porosity of 2-5% is common | Uniform properties throughout. Porosity under 1% due to centrifugal force |
Types of Metals | Works with iron, steel, aluminum, copper alloys, magnesium, and zinc | Best for aluminum, copper, steel, and stainless steel. Limited success with reactive metals |
Costs | Low tooling cost ($500-$5,000). High labor cost per part | High tooling cost ($10,000-$100,000). Low labor cost per part after setup |
Typical Applications | Engine blocks, valve bodies, pump housings, decorative items, prototypes | Pipes (6 inches to 10 feet diameter), cylinder liners, bearing housings, brake drums |
Production Volume | Economical for 1-1,000 parts. Suitable for prototypes and small batches | Requires minimum 100 parts for cost efficiency. Ideal for 1,000-100,000 parts annually |
Dimensional Accuracy | Tolerances of ±0.030 inches typical. Surface finish of 250-500 microinches | Tolerances of ±0.010 inches achievable. Surface finish of 60-125 microinches |
Part Complexity | Handles complex geometries, undercuts, and irregular shapes | Limited to cylindrical and symmetrical shapes. Cannot produce complex internal features |
Wall Thickness | Minimum 0.125 inches for aluminum, 0.1875 inches for iron | Uniform walls from 0.25 to 5 inches. Thickness controlled by rotation speed |
Lead Time | Parts ready in 2-4 weeks including pattern making | First parts in 6-8 weeks due to mold fabrication. Subsequent parts in days |