The main difference between cast aluminum and cast iron is density; cast aluminum is light (≈ 2.7 g/cm³) while cast iron is heavy (≈ 7.2 g/cm³). Aluminum cools fast, dissipates heat, resists corrosion, and machines easily. Iron handles higher compressive loads, retains heat, costs less per kilogram, and melts at 1 150 °C versus aluminum’s 660 °C.
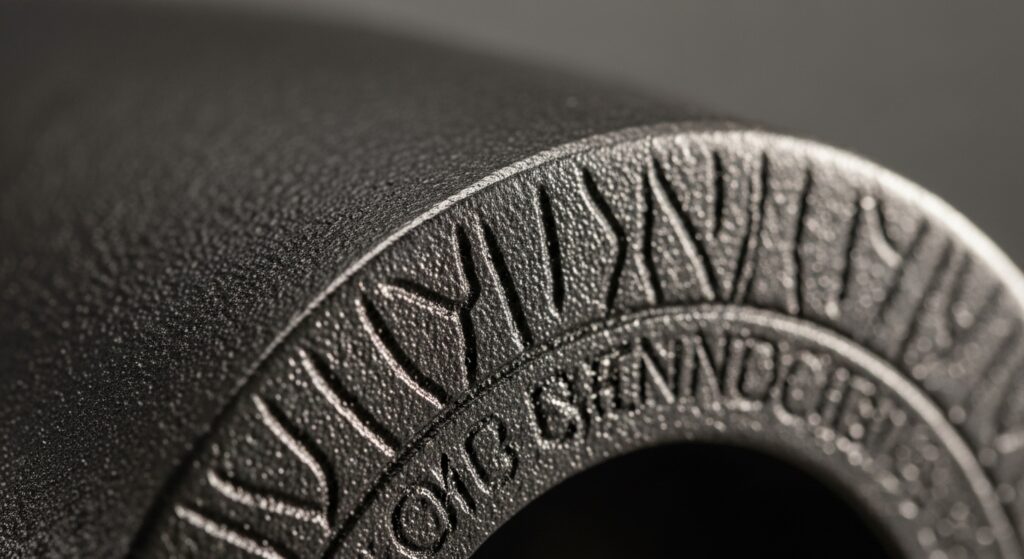
Cast Iron
Cast iron is fundamentally an iron-carbon alloy, distinguished from steel by its significantly higher carbon content, which typically ranges from 2% to 4% by weight. This high carbon concentration is the primary driver of its characteristic properties. Another critical element is silicon (Si), present at 1-3 wt%, which does not primarily act as a strengthener but as a crucial facilitator of the casting process by promoting graphite formation and improving the fluidity of the molten metal.
Types of Cast Iron
Grey Cast Iron
In the most common form, grey cast iron, the excess carbon precipitates out of the iron solution to form flakes of graphite distributed throughout the metallic structure.
White Cast Iron
When molten iron is cooled very rapidly, the carbon does not have time to precipitate as graphite. Instead, it combines chemically with the iron to form iron carbide (Fe3C), a compound known as cementite.
Ductile (Nodular) Iron
A major innovation in ferrous metallurgy was the discovery that adding a small amount of a nodulizing agent, typically magnesium (Mg), to the molten iron before casting dramatically alters the graphite’s morphology. Instead of forming sharp flakes, the graphite precipitates as discrete spheroids or nodules.
Malleable Iron
This type is produced by subjecting white cast iron to a prolonged heat treatment (annealing). This process breaks down the hard, brittle cementite structure and causes the carbon to re-form as irregular, rounded aggregates of graphite.
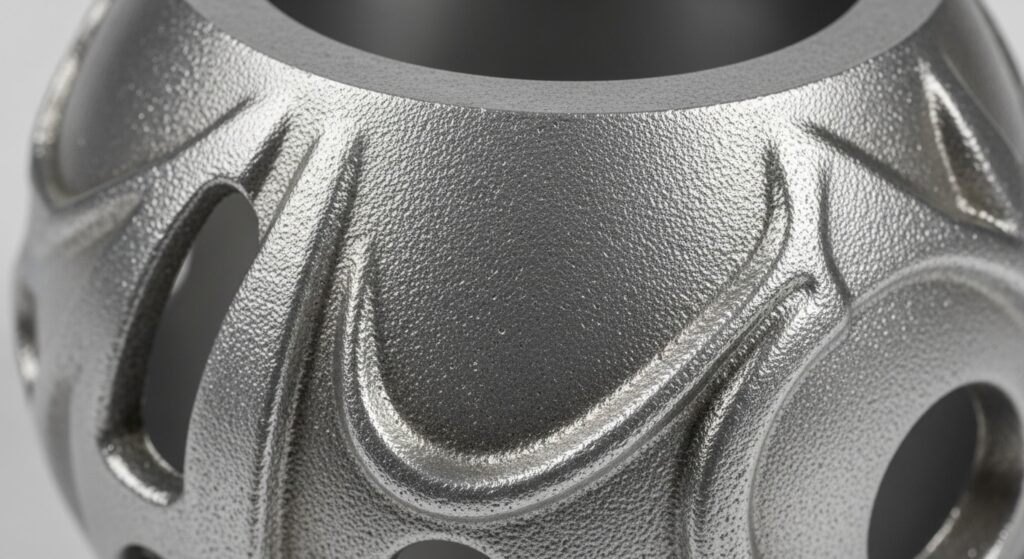
Cast Aluminum
Unlike cast iron, where carbon is the single dominant alloying element, cast aluminum is a complex system where a suite of elements works synergistically to achieve desired properties. The base metal, aluminum (Al), typically constitutes 80% to 95% of the alloy, with its inherent low density and corrosion resistance being augmented by carefully controlled additions.
Elemental Composition of Common Cast Alloys (wt%)
Element | Grey Cast Iron | Ductile Cast Iron | A380 Aluminum | A356 Aluminum |
---|---|---|---|---|
Iron (Fe) | ~93.7 – 95.5 | ~93.7 – 95.5 | ≤ 1.3 | ≤ 0.2 |
Aluminum (Al) | – | – | 80.25 – 83.25 | 91.1 – 93.3 |
Carbon (C) | 2.5 – 4.0 | 3.0 – 3.5 | – | – |
Silicon (Si) | 1.0 – 3.0 | 2.0 – 2.8 | 7.5 – 9.5 | 6.5 – 7.5 |
Copper (Cu) | – | < 0.1 | 3.0 – 4.0 | ≤ 0.2 |
Magnesium (Mg) | – | 0.03 – 0.06 | ≤ 0.1 | 0.25 – 0.45 |
Manganese (Mn) | 0.2 – 1.0 | 0.1 – 1.0 | ≤ 0.5 | ≤ 0.1 |
Phosphorus (P) | 0.02 – 1.0 | 0.01 – 0.1 | – | – |
Sulfur (S) | 0.01 – 0.12 | < 0.02 | – | – |
The Differences between Cast Aluminum and Cast Iron
Property | Cast Aluminum | Cast Iron |
---|---|---|
Weight | 169 pounds per cubic foot | 450 pounds per cubic foot |
Corrosion Resistance | Naturally rust-resistant | Rusts without protective coating |
Heat Retention | Heats and cools quickly | Retains heat for hours |
Maintenance | Minimal maintenance needed | Requires seasoning and oiling |
Strength | Lower tensile strength (19,000-48,000 PSI) | Higher tensile strength (20,000-60,000 PSI) |
Cost | Generally more expensive | Less expensive |
Melting Point | 1,220°F | 2,100°F |
Thermal Conductivity | 96-205 W/m·K | 46-55 W/m·K |
Brittleness | More ductile, less likely to crack | Brittle, can crack under impact |
Color | Silver-gray | Dark gray to black |
Magnetism | Non-magnetic | Magnetic |
Machinability | Easier to machine and shape | Harder to machine |