The pattern for investment casting is typically made of wax, which is coated with a ceramic shell. For vacuum casting, the pattern is usually a master model created with stereolithography or CNC, used to make silicone molds for resin parts. Both processes rely on precision patterns to ensure accurate final components.
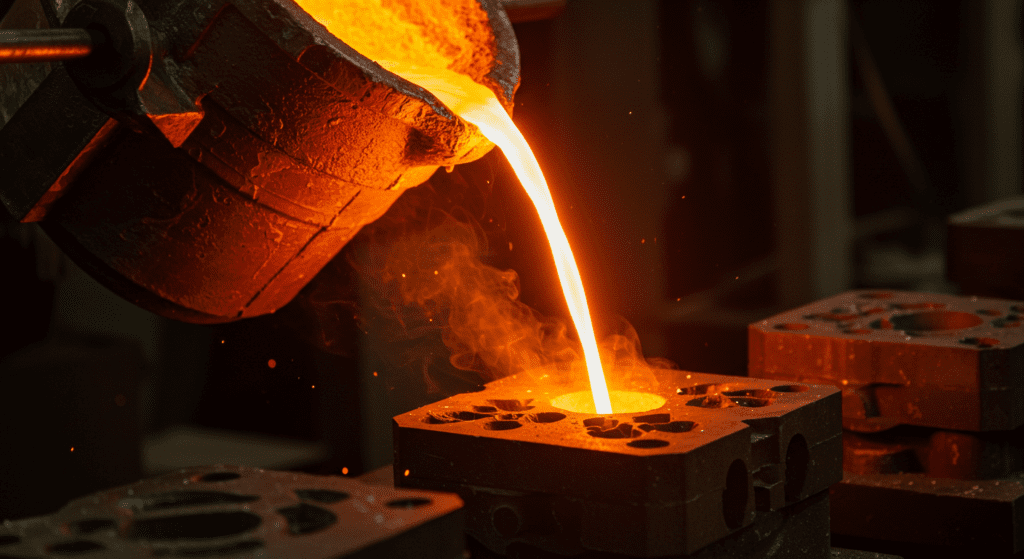
The Pattern in Investment Casting
The pattern in investment casting is an exact, positive replica of the part to be manufactured. Its defining characteristic is its sacrificial nature; the pattern is consumed or “lost” during the mold-making process. The primary purpose of this pattern is to create a precisely shaped cavity within a ceramic mold. This is achieved by coating the pattern with a refractory ceramic material. Once this ceramic coating has dried and hardened to form a robust shell, the pattern material is melted or burned out, leaving behind an internal cavity that mirrors the original pattern’s geometry.
The Pattern in Vacuum Casting
In the context of vacuum casting (also commonly referred to as urethane casting or polyurethane casting), the term “pattern” signifies a “master pattern.” This master pattern is a highly accurate, durable, and typically positive replica of the desired part. Unlike the sacrificial patterns used in investment casting, the master pattern in vacuum casting is not consumed during the process. Its primary purpose is to serve as the template or model for creating a flexible silicone rubber mold.
Liquid silicone rubber is poured around this master pattern and allowed to cure. Once the silicone has solidified, it is carefully cut and removed from the master pattern, yielding a flexible mold with a cavity that is a negative impression of the master. This silicone mold is then used for casting the final parts, typically from polyurethane resins. The master pattern itself is preserved and can be reused to create multiple silicone molds if the initial mold wears out or if additional molds are needed to increase production throughput.
Comparative Analysis: Patterns in Investment Casting vs. Master Patterns in Vacuum Casting
Feature | Investment Casting Pattern | Vacuum Casting Master Pattern |
---|---|---|
Primary Role in Process | Exact replica of the part; is consumed to create a ceramic mold cavity. | Durable replica of the part; used to create multiple flexible silicone molds. |
Typical Pattern Materials | Wax, castable plastics (e.g., SLA resins, polystyrene). | CNC machined plastics (ABS, PMMA), metals (aluminum), high-resolution 3D prints (SLA). |
Common Pattern Creation Methods | Injection molding (high vol.), 3D printing (low vol./prototypes), hand-carving. | CNC machining, 3D printing (SLA, PolyJet) followed by finishing. |
Pattern Lifecycle/Disposability | Sacrificial; one pattern per mold (which makes one casting/tree). | Reusable; one master pattern can create many silicone molds. |
Importance of Pattern’s Own Surface Finish | Important for good cast surface, but ceramic shell process can smooth some minor flaws. | Critically important; silicone replicates master surface with extreme fidelity. |
Tooling for Pattern Creation | Metal dies for injection molding (expensive); none for 3D printing or hand-carving. | None for 3D printing; CNC programming/machine setup for machining. |
Subsequent Mold Material Created | Refractory ceramic shell. | Flexible silicone rubber. |
Typical End-Product Materials Cast | Metals and alloys (steel, aluminum, superalloys, copper alloys, etc.). | Polyurethane resins (simulating thermoplastics and rubbers). |
Suitability for Geometric Complexity | Excellent for highly complex internal/external features in metals. | Very good for complex external features, undercuts in plastics. |
Cost Implications (Pattern & Related Tooling) | High tooling for injection molded patterns; low for 3D printed patterns. | Moderate for master pattern (CNC/3D print + finishing); low for silicone molds. |
Typical Production Volume Suitability (for the pattern’s use) | Low (3D print) to high (injection molding) for metal parts. | Prototypes to small/medium series (5-100 parts) for plastic parts. |
Primary Output of Pattern | Forms cavity in a single-use ceramic mold. | Used to create multiple reusable (short-life) silicone molds. |