Casting Draft Angle is the intentional taper built into mold surfaces to facilitate easy part removal after solidification. This critical design element prevents issues like surface damage, part distortion, and mold wear during the casting process. Draft angle requirements vary by casting method: sand casting typically needs 1-1.5°, die casting requires 0.5-3°, while investment casting can operate with minimal draft of just 0° due to its unique ceramic shell process.
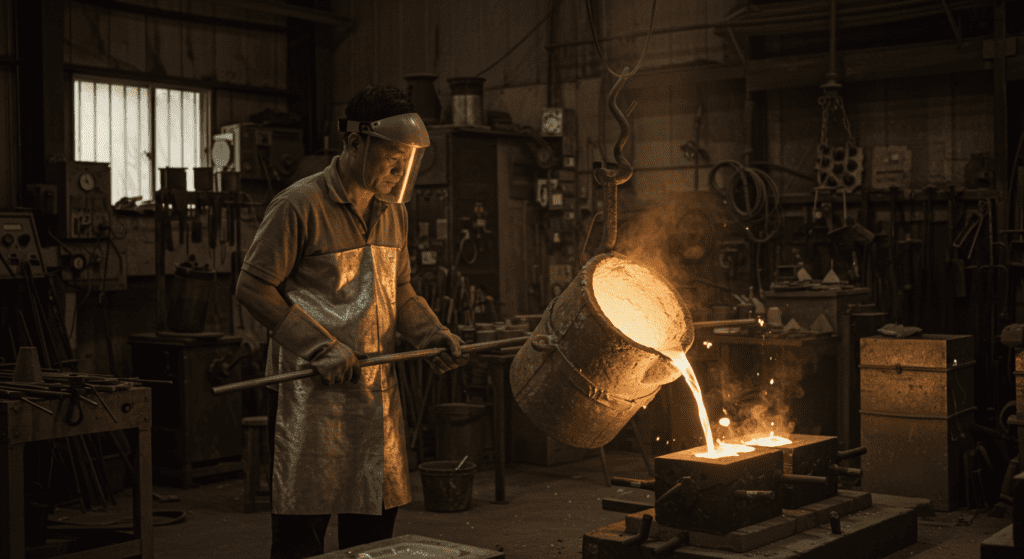
What Is Draft Angles
Casting Draft Angle refers to the taper or slope intentionally designed into the vertical surfaces of a mold cavity to facilitate the removal of the cast part without damage. This angular deviation from the vertical axis allows the casting to release more easily from the mold after solidification.
Draft angles are measured in degrees from the vertical axis of the mold. Typically ranging from 0.5° to 5°, these angles are incorporated on surfaces perpendicular to the parting line or direction of mold opening.
The Principle of Draft Angles
Draft angles function on the fundamental principle of reducing friction and preventing mechanical locking during the part ejection phase. As molten material solidifies, it typically contracts slightly, but this contraction alone is insufficient to ensure smooth removal.
The angled surfaces create a gradually increasing clearance between the mold and casting as the part moves in the direction of ejection. This progressive disengagement significantly reduces the contact area and the corresponding friction forces.
For internal features (holes, recesses), the draft angle faces inward, making the opening wider at the parting line. Conversely, for external features, the draft angle faces outward, making the feature narrower at the parting line.
Consequences of Inadequate or Zero Draft in Conventional Molds
Insufficient draft angles can lead to numerous production issues that affect both the casting quality and mold longevity.
Surface Damage
When inadequate draft is present, the tight clearance between the casting and mold surfaces creates significant frictional forces during ejection. This friction can cause galling, scoring, or surface tearing on the casting.
The problem becomes particularly severe with textured surfaces or when using materials with high surface roughness. The microscopic interlocking between the casting and mold surfaces can strip away surface details or create drag marks along the entire withdrawal path.
Part Distortion
Insufficient draft can cause parts to bind in the mold during ejection. The resulting extraction force may exceed the material’s strength while it’s still warm, leading to plastic deformation or warping.
This distortion is more pronounced in deep-draw features where the contact area between the casting and mold is extensive. The ejection stress concentrates at specific points rather than distributing evenly across the part.
Mold Damage
Zero or minimal draft places excessive wear on mold surfaces due to the scraping action during part removal. This accelerated wear reduces mold life and increases maintenance requirements.
Ejection pins may apply uneven pressure when forcing out a resistant casting, potentially damaging both the mold and the part. In extreme cases, catastrophic mold failure can occur if parts become completely seized.
Dimensional Inaccuracies
Parts ejected with difficulty often exhibit dimensional inconsistencies due to uneven stresses during removal. These stresses can cause localized stretching, compression, or other deformations.
Typical (Often Optional or Minimal) Draft Values and Tolerances
Draft requirements vary significantly across different casting processes due to their unique characteristics and limitations.
Sand Casting
Typical draft angles in sand casting range from 1∘ to 1.5∘, with some sources citing values like 1/8 inch per foot (approximately 0.6∘) as a common guideline, though more can be required depending on pattern depth and complexity.
Die Casting
While the draft angles in die casting can sometimes be smaller than those in sand casting, they are absolutely essential. Typical values can range from 0.5∘ for shallow features in favorable alloys to 2∘ or 3∘ or even more for deeper cavities, textured surfaces, or alloys prone to sticking.
Investment Casting
Investment casting requires minimal draft angles compared to other processes due to the collapsible, non-rigid nature of the ceramic shell mold. Draft angles as low as 0.5° are often sufficient for most features.
For straight walls up to 25mm in height, a draft angle of 0.5° is typically adequate. Deeper features may require incrementally larger draft angles, but rarely exceeding 1° even for the deepest sections.
Feature | Investment Casting | Sand Casting | Die Casting |
General Necessity | Often not required / Minimal for final part | Required | Critical |
Primary Reason | Breakable shell, wax shrinkage | Pattern removal from sand mold | Part ejection from permanent metal die |
Typical Draft Angle | Optional, 0° to 1° max (if applied to pattern tool) | ~1° to 1.5° or more (e.g., 1/8″ per ft -0.6°) | 0.5° to 3°+ (varies by alloy, depth, texture) |
Negative Draft | Permissible | Not typically permissible | Not typically permissible (requires complex mechanisms like side cores) |
Mold Type | Expendable ceramic shell | Expendable sand mold | Reusable metal die |
Tooling Cost Impact | Draft mainly impacts wax pattern tool if needed | Draft impacts pattern cost | Draft is critical for die life & cost-effectiveness |
Does Investment Casting Require Draft
For simple geometries without undInvestment casting does not require draft angles because the ceramic shell used in the process is broken away after casting. Unlike sand casting, where draft prevents pattern damage, investment casting allows complex shapes without tapering, making it ideal for intricate and precise components. However, a minimal draft of 0.5° is still commonly applied as a manufacturing best practice to facilitate pattern removal from the initial wax tooling.