Vacuum investment casting is a metal casting process that takes place in a vacuum chamber rather than in normal atmospheric conditions. This specialized technique combines traditional investment casting methods with vacuum technology to create metal parts with superior quality and fewer defects. The process removes air and gases from the casting environment, which leads to cleaner, stronger metal components.
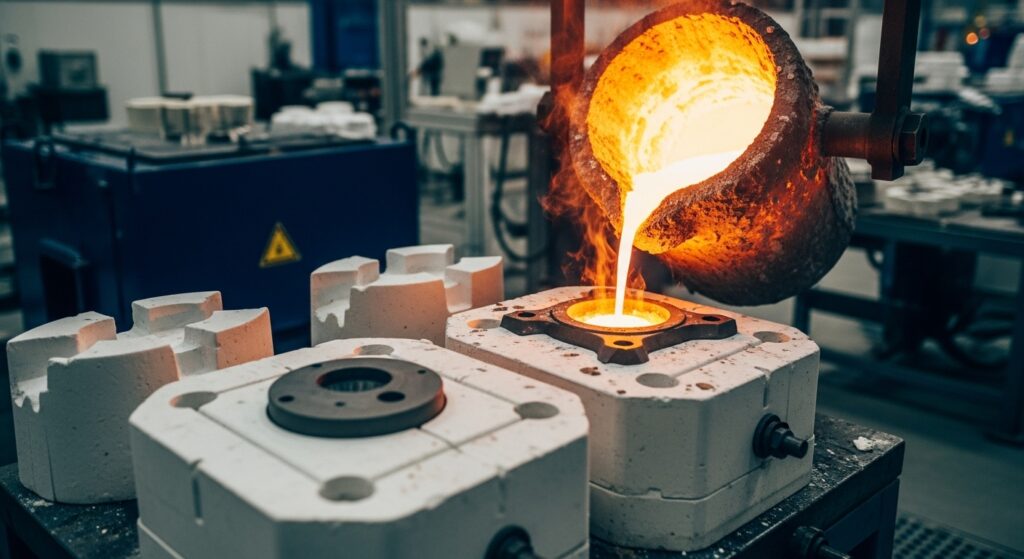
Advantages of Vacuum Investment Casting
Prevention of Oxidation
By removing oxygen from the casting chamber, the vacuum environment prevents the chemical reaction between the hot metal and atmospheric oxygen. When metals are heated to their melting point in normal air, they readily combine with oxygen to form oxides. These oxide particles weaken the final product and create surface defects.
In vacuum casting, the oxygen level drops to less than 0.001% of normal atmospheric concentration. This near-complete absence of oxygen means the molten metal stays pure throughout the entire casting process. The result is a finished part with a clean surface and consistent material properties from surface to core.
Reduction of Gas Porosity
Molten metals can dissolve significant amounts of gases, particularly hydrogen and nitrogen, which are present in the atmosphere. The vacuum environment facilitates the removal of these dissolved gases from the melt prior to and during pouring. When metal solidifies under normal pressure, these dissolved gases form bubbles that create tiny holes called porosity.
Vacuum casting reduces the pressure to approximately 0.1 to 10 millibars, compared to normal atmospheric pressure of 1013 millibars. At this low pressure, dissolved gases escape from the molten metal before it solidifies. Parts produced through vacuum casting show 80-90% less porosity than those made through conventional casting methods.
Improved Mold Filling
The vacuum can play an active role in enhancing the flow of molten metal into the mold cavity. By evacuating air from the mold, back-pressure that could impede metal flow is eliminated.
In a vacuum environment, molten metal flows 30-40% more easily into tight spaces and narrow channels. The pressure difference between the vacuum chamber and the molten metal actually pulls the metal into every corner of the mold. This pulling action ensures complete filling of even the most challenging geometries, reducing the risk of incomplete castings.
Enhanced Cleanliness and Purity
The overall effect of the vacuum environment is the production of cleaner metal with a significantly lower content of non-metallic inclusions and dissolved gases. Without exposure to atmospheric contaminants, the metal maintains its chemical composition throughout the casting process.
This enhanced purity translates directly into improved mechanical properties. Vacuum-cast parts demonstrate 15-20% higher tensile strength and 25% better fatigue resistance compared to standard castings. The absence of inclusions also creates a more uniform microstructure, which improves the part’s response to heat treatment and surface finishing operations.
The Vacuum Investment Casting Process
Step 1: Pattern Creation
A precise wax or plastic pattern is created that represents the exact shape of the desired final metal part. This pattern is typically made by injecting wax into a metal die or mold. For complex parts, multiple wax patterns may be assembled together on a central wax “tree” or sprue system.
Step 2: Ceramic Shell Building
The wax pattern assembly is repeatedly dipped into a ceramic slurry (usually containing silica, zircon, or alumina) and then coated with refractory sand or stucco. This process is repeated 5-15 times, allowing each layer to dry between coats, until a ceramic shell of sufficient thickness (typically 6-10mm) is built around the wax pattern.
Step 3: Dewaxing
The ceramic shell with the wax pattern inside is placed in an autoclave or flash fire oven at temperatures around 90-175°C (200-350°F). The heat melts and removes the wax, leaving a hollow ceramic mold in the exact shape of the desired part. Any remaining wax residue is burned out.
Step 4: Mold Preparation and Preheating
The empty ceramic shell is inspected for cracks or defects, then preheated to temperatures between 800-1100°C (1470-2010°F). This preheating serves to further cure the ceramic, remove any moisture, and minimize thermal shock when molten metal is poured.
Step 5: Vacuum Chamber Preparation
The preheated ceramic mold is placed inside a vacuum casting chamber. The chamber is sealed and the air is evacuated to create a vacuum environment, typically achieving pressures of 10^-2 to 10^-4 torr. This vacuum environment prevents oxidation and gas porosity in the final casting.
Step 6: Metal Melting
The casting metal (such as titanium, aluminum, steel, or superalloys) is melted in a separate crucible within the vacuum chamber using induction heating or electron beam melting. The metal is heated to the appropriate pouring temperature, which varies by alloy but is typically 50-150°C above the melting point.
Step 7: Vacuum Pouring
While maintaining the vacuum environment, the molten metal is poured into the ceramic mold. The vacuum ensures complete filling of even thin sections and intricate details, while preventing air entrapment and oxidation. Some systems use additional vacuum or pressure differential to assist metal flow.
Step 8: Solidification and Cooling
The filled mold remains in the vacuum chamber during initial solidification to ensure proper metallurgical properties. Once solidified, the vacuum is released and the casting is allowed to cool to handling temperature, either in controlled atmosphere or air.
Step 9: Shell Removal
The ceramic shell is removed from the solidified metal casting through mechanical vibration, high-pressure water blasting, or chemical dissolution. For some applications, the shell may be removed while the casting is still warm to take advantage of differential thermal contraction.
Step 10: Finishing Operations
The individual castings are cut from the sprue system using saws, cutting wheels, or torches. Gates and risers are removed, and the casting surfaces are cleaned through grinding, sand blasting, or chemical treatments. Final operations may include heat treatment, machining, surface treatments, and quality inspection including dimensional checks and non-destructive testing.