The main difference between investment casting and CNC machining is how the material is shaped. Investment casting creates parts by pouring molten metal into wax-based molds, ideal for complex geometries. CNC machining cuts material from a solid block, offering higher precision, faster turnaround, and better suitability for tight tolerances.
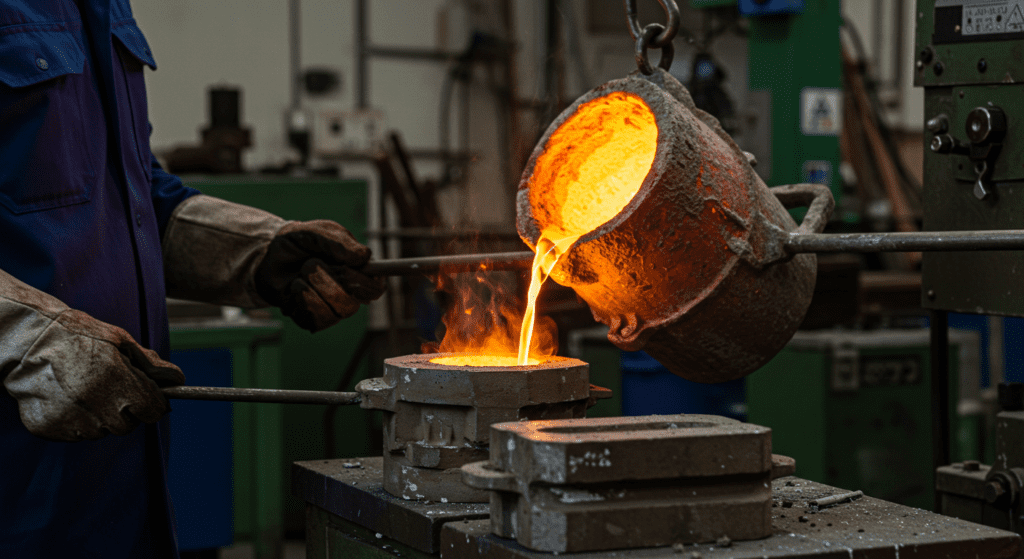
What Are These Processes
Investment Casting creates metal parts by pouring molten metal into ceramic molds. You start with a wax model of your part. You coat this wax in ceramic material to form a hard shell. Then you melt out the wax and pour in liquid metal. Once the metal cools, you break away the ceramic to reveal your finished part.
CNC Machining cuts away material from a solid block to create your part. It’s like carving a sculpture, but with computer-controlled precision. A computer guides cutting tools to remove material bit by bit. These machines work with almost anything – metals, plastics, wood, even glass.
When Should You Use Each Process?
Choose investment casting when your part has complex internal shapes, thin walls, or tricky geometries. It’s perfect for aerospace turbine blades, car turbocharger housings, surgical tools, and marine propellers.
The process handles intricate designs that would be impossible or expensive to machine.
Choose CNC machining when you need extreme precision or you’re working with various materials. It’s ideal for prototypes, electronic housings, gears, medical implants, and custom brackets.
CNC works best for parts that need tight tolerances or when you’re making just a few pieces.
What Materials Can You Use?
Investment casting works only with metals that can be melted and poured. You can cast steel, stainless steel, aluminum, titanium, bronze, and special high-temperature alloys. The material must flow well when melted and handle the high heat of the process.
CNC machining handles almost any solid material. Beyond all types of metals, it cuts plastics like nylon and PEEK, composites, wood, certain ceramics, and even foam.
How Much Will It Cost?
Tooling costs differ dramatically between the two methods.
Investment casting needs custom wax patterns and ceramic molds. This setup typically costs thousands of dollars. CNC machining uses standard cutting tools and basic fixtures, costing just hundreds of dollars to start.
Per-part costs flip as quantities increase.
For 1-10 parts, CNC costs less because there’s no mold expense. Each CNC part might cost $50-500 depending on complexity. Investment casting the same parts could cost $200-1000 each due to mold setup.
But make 1,000 parts, and casting drops to $10-50 per part while CNC stays nearly the same price.
The break-even point usually hits around 50-200 parts, depending on size and complexity.
How Precise Are They?
Investment casting achieves tolerances of ±0.004 to ±0.020 inches (±0.1 to ±0.5 mm). That’s good for most applications, but not ultra-precise work.
CNC machining hits much tighter tolerances of ±0.001 to ±0.005 inches (±0.025 to ±0.127 mm). High-end machines can reach ±0.0002 inches on critical features.
What About Surface Finish?
Investment casting produces surfaces measuring 60-200 microinches Ra (1.5-5.1 μm Ra). Most parts come out at about 125 microinches – as smooth as a typical machined surface.
You’ll rarely need additional finishing except on sealing surfaces.
CNC machining starts at the same 125 microinches but can go much smoother. With extra passes, you can reach 63 microinches easily. Special techniques achieve mirror finishes below 8 microinches.
Both give you smooth parts, but CNC offers more control over the final finish.
How Complex Can Your Design Be?
Investment casting loves complexity. You can create hollow interiors, undercuts, and paper-thin walls all in one shot.
Since you’re forming around a wax pattern, there are no tool access limitations. If you can make it in wax, you can cast it in metal.
CNC machining faces tool access challenges. The cutting tool must physically reach every surface you want to cut.
Deep pockets, internal features, and severe undercuts need special tools or multiple setups. Simple to moderately complex shapes work best.
How Fast Can You Get Parts?
CNC machining delivers prototypes in 2-5 days. There’s no tooling wait – just program and cut.
Making design changes takes hours, not weeks. But each part takes the same time to make, whether it’s your first or your hundredth.
Investment casting needs 3-6 weeks for the first part. You must create patterns and perfect the mold process.
Once set up, though, you can cast dozens of parts at once. High-volume production runs much faster than CNC.
What Production Volumes Work Best?
For 1-50 parts, CNC machining usually wins. There’s no minimum order and no tooling to pay off.
Design changes are easy and fast.
For 500+ parts, investment casting becomes more economical. The mold cost spreads across many parts, dropping the unit price significantly.
What’s the Environmental Impact?
CNC machining turns 15-30% of your raw material into waste chips. Most shops recycle these metal chips, but it’s still wasteful.
The process also uses cutting fluids and consumes significant electricity running motors and pumps.
Investment casting uses lots of energy melting metal and making ceramic shells. The ceramic becomes waste after each use, though some gets recycled.
However, nearly all the metal ends up in finished parts with minimal waste.
Making Your Decision
Choose investment casting when you need:
- Complex internal geometries
- Production runs over 200 parts
- Multiple materials in exotic alloys
- Near-net shapes with minimal machining
Choose CNC machining when you need:
- Extremely tight tolerances (under ±0.005″)
- Quick prototypes or design iterations
- Small quantities (under 50 parts)
- Various materials including plastics
Many projects use both processes. Cast the complex base shape, then machine critical surfaces for precision.
The best choice depends on your specific needs for quantity, complexity, precision, and timeline.