The most common defects in investment casting include shrinkage, porosity, misruns, cold shuts, and inclusions. Shrinkage is caused by improper solidification; porosity results from trapped gas; misruns and cold shuts stem from low metal temperatures; inclusions occur due to ceramic shell breakdown or contamination.
Cavity-Type Defects
Gas Porosity
Gas porosity creates small holes or voids in castings when gases become trapped during solidification. These defects occur in Investment Casting when moisture in the ceramic shell releases steam, when metals react with mold materials, or when dissolved gases in the molten metal cannot escape quickly enough. The trapped gas forms spherical or elongated cavities that weaken the casting structure.
To prevent gas porosity, foundries dry ceramic shells thoroughly before pouring metal. They also degas molten metals using vacuum treatments or inert gas purging.
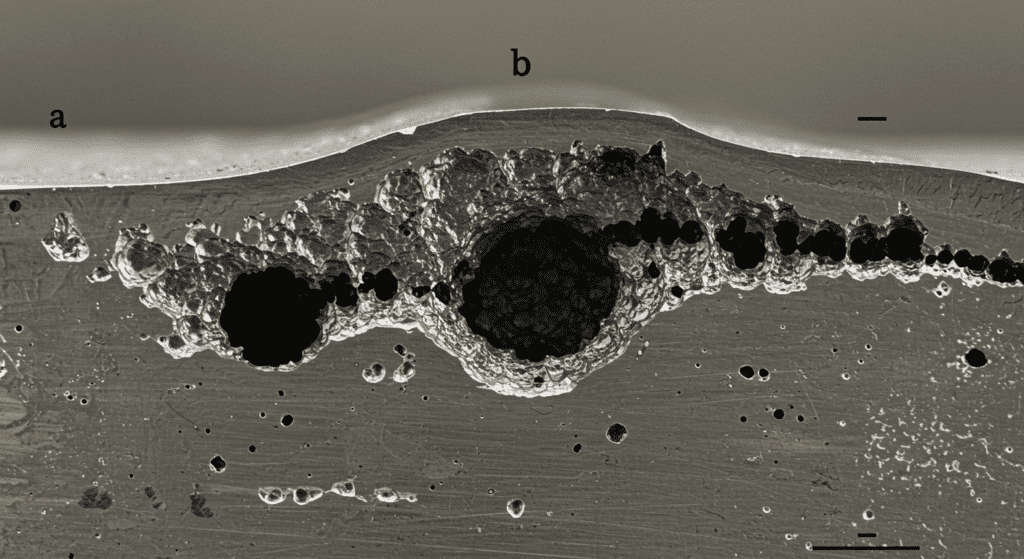
Shrinkage Porosity
Shrinkage porosity forms irregular, jagged cavities when metal contracts during cooling and solidification. This defect appears in thick sections of castings where metal solidifies last and cannot draw liquid metal from other areas. The resulting voids have rough, dendritic surfaces that distinguish them from smooth gas porosity.
Foundries eliminate shrinkage porosity by designing proper feeding systems with risers and gates. These channels supply liquid metal to compensating for volumetric shrinkage.
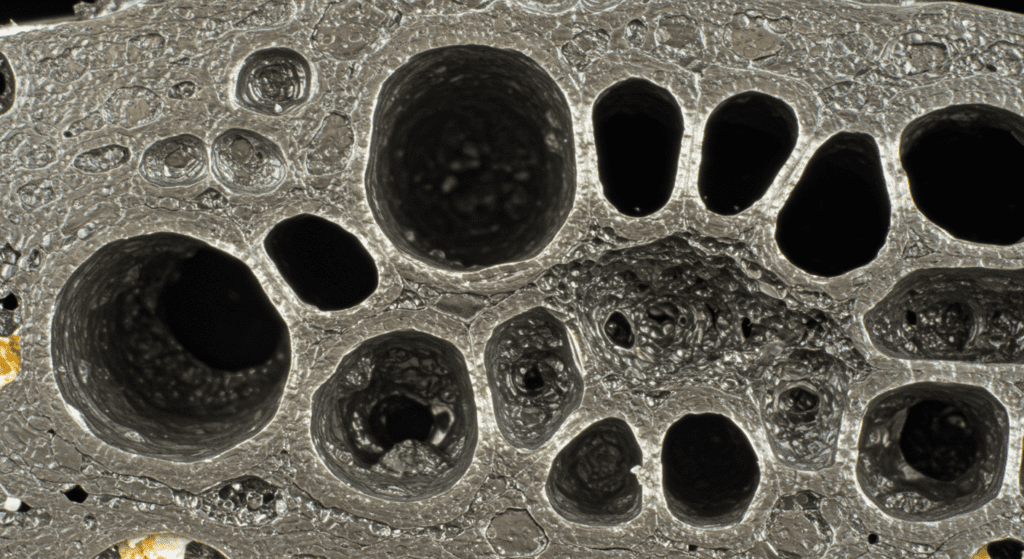
Discontinuity Defects
Hot Tears / Hot Cracks
Hot tears develop when casting sections experience tensile stress during solidification at temperatures just below the solidus point. These jagged, irregular cracks form along grain boundaries where the metal has low strength but high stress from differential cooling rates.
Prevention requires careful alloy selection and mold design that minimizes stress concentration. Increasing mold collapsibility reduces restraint on the contracting metal. Adding grain refiners to the alloy improves hot tear resistance by creating finer, more uniform grain structures.
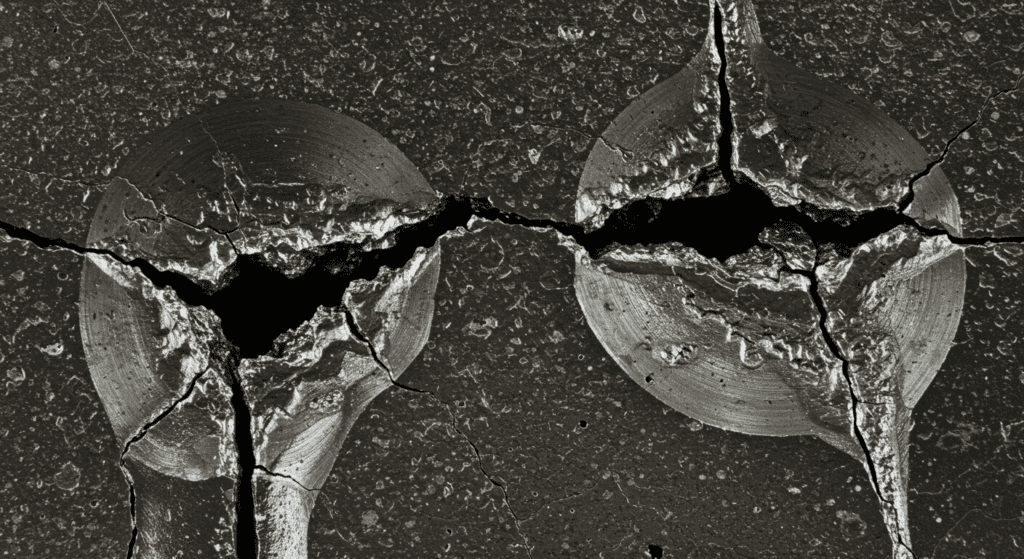
Cold Cracks
Cold cracks appear after complete solidification when residual stresses exceed the material’s strength at room temperature. These cracks have straighter paths than hot tears and often propagate through grains rather than along boundaries.
Stress relief heat treatments effectively prevent cold cracks by reducing residual stresses. Controlled cooling rates and proper handling procedures during shakeout also minimize crack formation. Design modifications that reduce sharp corners and stress concentrations help prevent these defects.
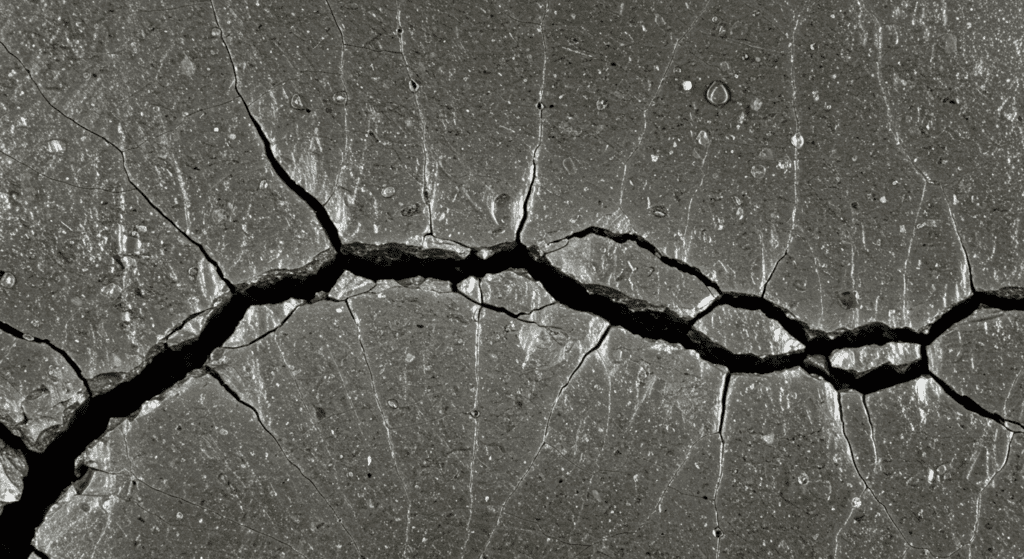
Cold Shuts / Laps
Cold shuts occur when two metal streams meet but fail to fuse completely due to premature solidification. This creates a visible seam or fold on the casting surface. Low pouring temperatures, slow filling rates, or interrupted pouring cause these defects. The unfused areas create weak points that compromise mechanical properties.
Maintaining proper pouring temperatures above 50-100°F of the liquidus temperature prevents cold shuts. Continuous, rapid pouring ensures metal streams fuse before surface oxidation occurs.
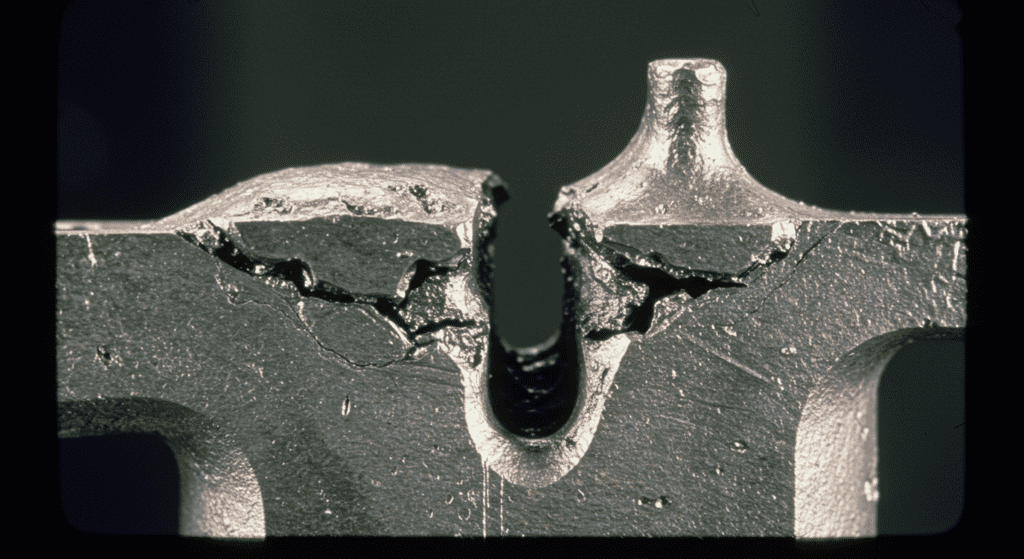
Surface and Shape Defects
Inclusions
Inclusions are foreign particles trapped within the solidified casting that create internal defects and surface blemishes.
- Ceramic Inclusions – Broken shell fragments enter the metal during pouring or from erosion of the ceramic mold. These hard particles create stress concentrations and machining difficulties.
- Slag and Dross – Oxidized metal and flux residues float on molten metal surfaces and become entrapped during pouring. These inclusions appear as dark spots or streaks in the finished casting.
Careful handling prevents shell damage that causes ceramic inclusions. Using ceramic filters in the gating system traps particles before they enter the mold cavity. Regular skimming of molten metal surfaces removes slag and dross before pouring.
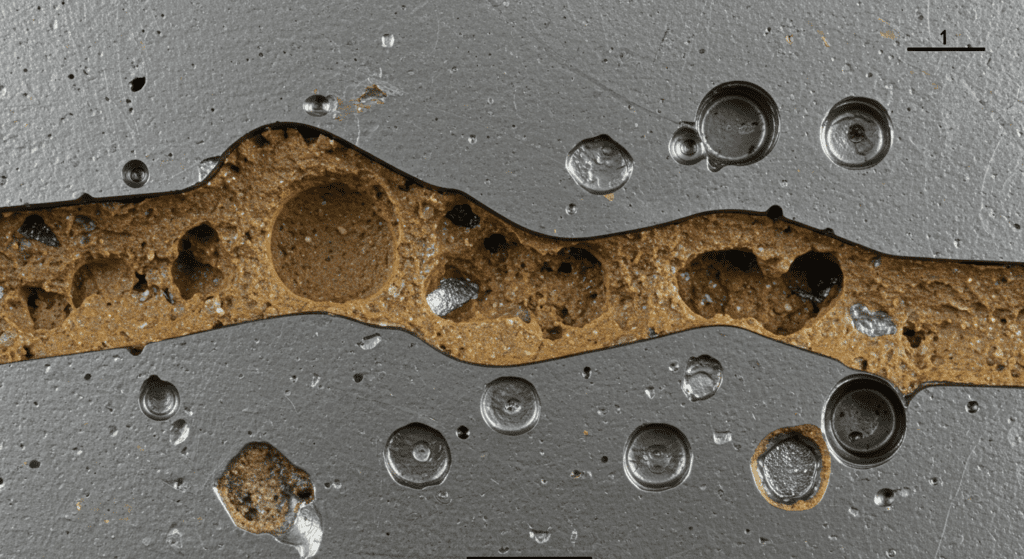
Filling-Related Defects: Misruns
Misruns occur when molten metal solidifies before completely filling the mold cavity. This creates incomplete castings missing features or entire sections. Low metal temperature, inadequate metallostatic pressure, or restricted flow paths cause misruns. Thin sections face higher misrun risk due to rapid heat loss.
Increasing pouring temperature by 50-150°F above normal improves fluidity and filling capability. Redesigning gating systems with larger cross-sections reduces flow resistance. Preheating molds to 200-400°F slows solidification in thin sections.
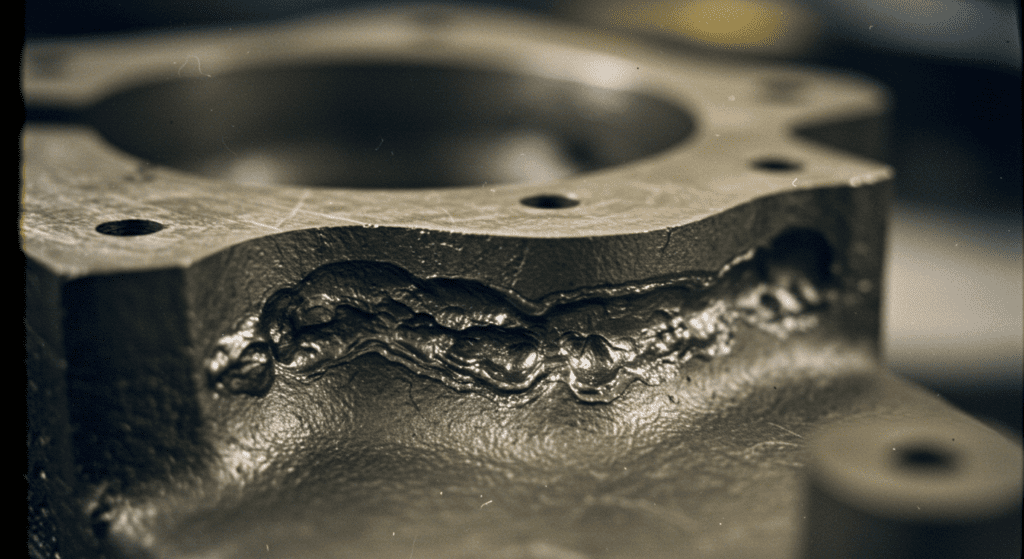
Mold-Metal Interaction Defects
These defects result from chemical or physical reactions between molten metal and the ceramic shell.
- Metal Penetration – Liquid metal infiltrates pores or cracks in the ceramic shell, creating rough surface textures and dimensional inaccuracies. High metallostatic pressure and coarse shell materials increase penetration risk.
- Fusion – Chemical reactions between metal and mold create bonded layers difficult to remove. This occurs with reactive alloys at high temperatures or when incompatible shell materials contact certain metals.
Using finer refractory materials and additional shell coats prevents metal penetration. Applying appropriate mold washes creates barrier layers between metal and ceramic. Selecting chemically compatible shell systems for specific alloys prevents fusion defects.
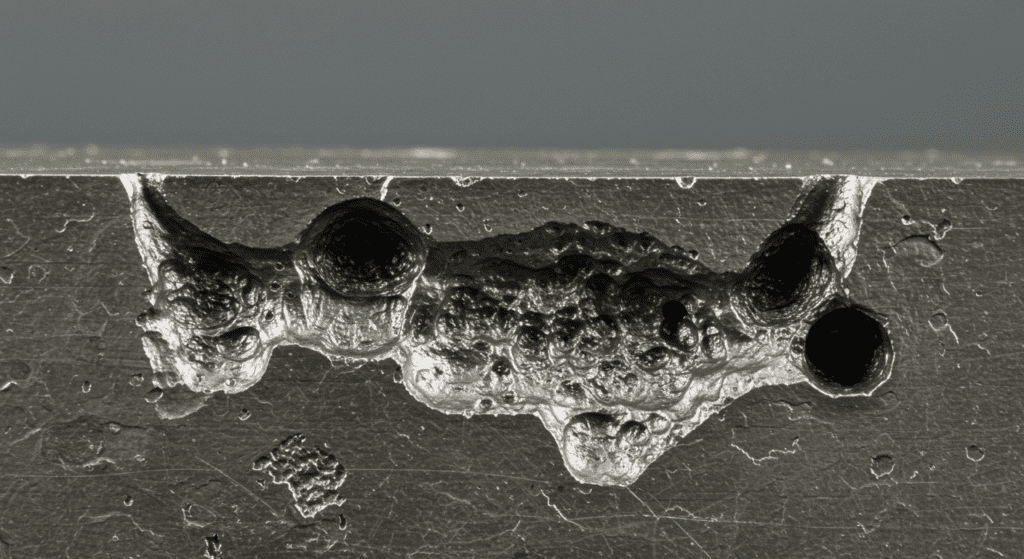
Shell and Mold Integrity Defects
Physical failure of the ceramic shell during casting creates various geometric defects.
- Flash / Fins – Metal leaks through cracks or parting lines in the shell, creating thin metal projections on the casting surface. These require grinding or machining for removal.
- Swells / Bulges – Ceramic shell deformation under metallostatic pressure creates localized thickness variations. Insufficient shell strength or excessive metal head pressure causes these defects.
Proper shell building with 6-8 coats provides adequate strength to resist cracking. Controlling drying between coats prevents stress buildup that causes shell failure. Reinforcing critical areas with additional stucco layers prevents localized deformation.
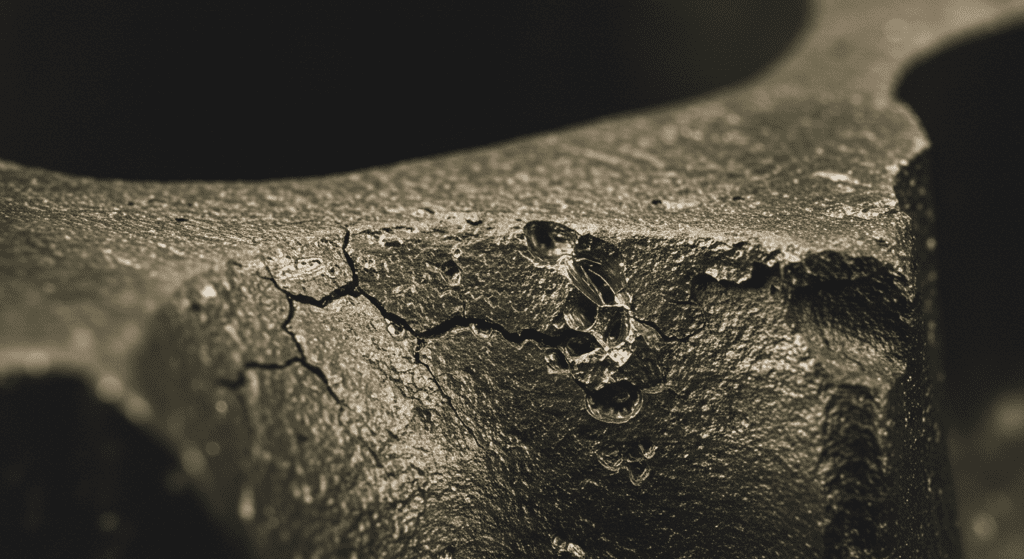
Dimensional and Shape Defects
These defects affect the geometric accuracy and dimensional tolerance of castings.
- Distortion / Warping – Non-uniform cooling rates create differential thermal contraction that bends or twists the casting. Long, thin sections and asymmetric designs face higher distortion risk.
- Mismatch – Assembly errors during pattern or shell production create stepped surfaces where mold sections meet. This produces castings with offset features that require extensive machining.
Fixture supports during cooling maintain proper geometry and prevent warping. Symmetrical gating designs promote uniform cooling rates. Quality control checks during pattern assembly and shell building prevent mismatch defects before metal pouring.
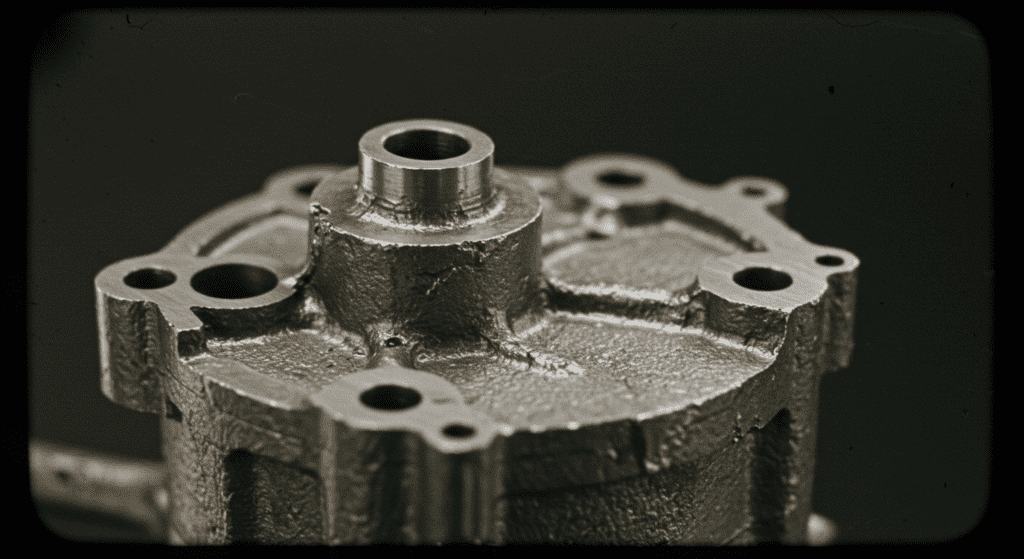