Investment casting leaves only trace impurities. The most common impurities include ceramic particles from the mold shell, residual wax compounds, and various metal oxides that form during the melting process.
These impurities typically account for less than 0.5% of the final cast part in well-controlled processes.
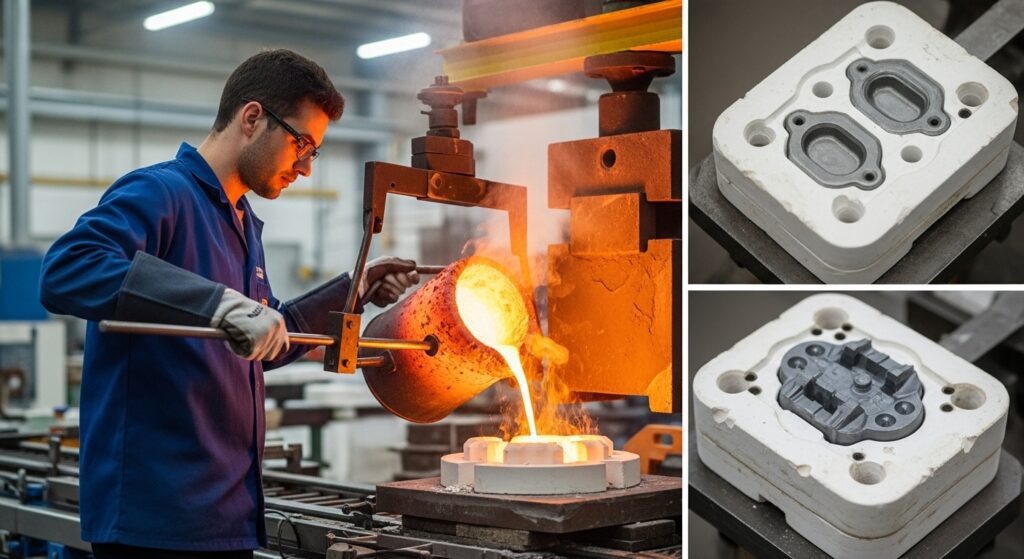
Source of Impurities
Process Stage | Wax/Ash Residue | Ceramic Inclusions | Slag/Dross | Oxides/Nitrides | Dissolved Gas | Shrinkage | Surface/Shape Defects |
---|---|---|---|---|---|---|---|
Pattern Making | X | X | |||||
Wax Assembly | X | X | |||||
Shell Building | X | X | |||||
Dewaxing/Burnout | X | X | X | X | |||
Alloy Melting | X | X | X | ||||
Pouring & Solidification | X | X | X | X | X | X | |
Finishing | X |
Types of Impurities in Investment Casting

Non-metallic Inclusions
Non-metallic inclusions are solid particles trapped within the metal during casting. These particles don’t mix with the base metal and create weak spots in the final part.
- Ceramic Inclusions: Ceramic inclusions come from the investment mold shell breaking down during metal pouring. These particles range from 10 to 500 micrometers in size and consist mainly of silica, alumina, and zirconia.
- Slag, Dross, And Oxide Inclusions: This category includes a range of non-metallic particles that are the byproducts of chemical reactions occurring within the molten metal or at its interface with the surrounding environment.
- Exogenous Inclusions: These are contaminants that enter the melt from an external source. Examples include particles from the refractory lining of the furnace or ladle, or impurities present in the initial charge material.
- Endogenous Inclusions: These are formed by chemical reactions within the melt itself, most commonly between the molten metal and dissolved gases like oxygen, sulfur, or nitrogen.
Residual Wax and Ash
Residual wax remains when the burnout process doesn’t completely remove the wax pattern. Standard burnout cycles reach 1,800°F, but incomplete heating leaves carbon deposits that contaminate the metal.
These carbon residues typically measure less than 0.1% by weight in properly processed parts. However, rushed burnout cycles or thick wax sections can leave up to 0.5% carbon contamination.
Ash forms from incomplete wax combustion and contains carbon particles mixed with wax additives. This gray-black residue sticks to mold surfaces and mixes with poured metal.
Contaminants from Raw Metal Stock
The purity of the final casting can be no better than the purity of the initial charge material. Raw metal ingots and scrap introduce their own impurities into investment castings. Common contaminants include sulfur (0.01-0.05%), phosphorus (0.01-0.03%), and trace elements like lead or bismuth.
How to Minimize Impurities
- Control melt temperature precisely – Keep temperatures within 50°F of recommended ranges to prevent excess gas absorption and oxide formation
- Use high-quality virgin metals – Limit recycled content to 20-30% and verify incoming material composition with spectrographic analysis
- Optimize shell building – Apply 6-8 ceramic coats with proper drying between layers to prevent shell breakdown
- Implement proper wax removal – Use flash fire dewaxing at 1,800°F minimum with 2-hour hold times for complete carbon elimination
- Design effective gating systems – Size runners and gates to maintain laminar flow at 2-3 feet per second, preventing turbulence
- Degas molten metal thoroughly – Bubble inert gas through aluminum for 10-15 minutes or use rotary degassing to reduce hydrogen below 0.15 ml/100g
- Add grain refiners and modifiers – Use 0.1-0.2% titanium-boron in aluminum or 0.02-0.04% magnesium in cast iron to improve structure
- Control pouring temperature and speed – Pour at the lowest temperature allowing complete fill, typically 100-150°F above liquidus
- Apply proper feeding techniques – Design risers 1.5 times the section thickness and position them to solidify last
- Maintain clean working conditions – Filter melt shop air to 5 microns and keep humidity below 50% to minimize contamination
- Inspect and test regularly – Perform dye penetrant testing on 10% of production and X-ray critical components to catch defects early