Metal casting originated around 3200 BCE in Mesopotamia. Ancient civilizations used it to create tools, weapons, and art. During the Industrial Revolution, casting evolved with the introduction of sand casting and mechanized production. Modern casting uses advanced alloys, 3D modeling, and precision controls for mass manufacturing.
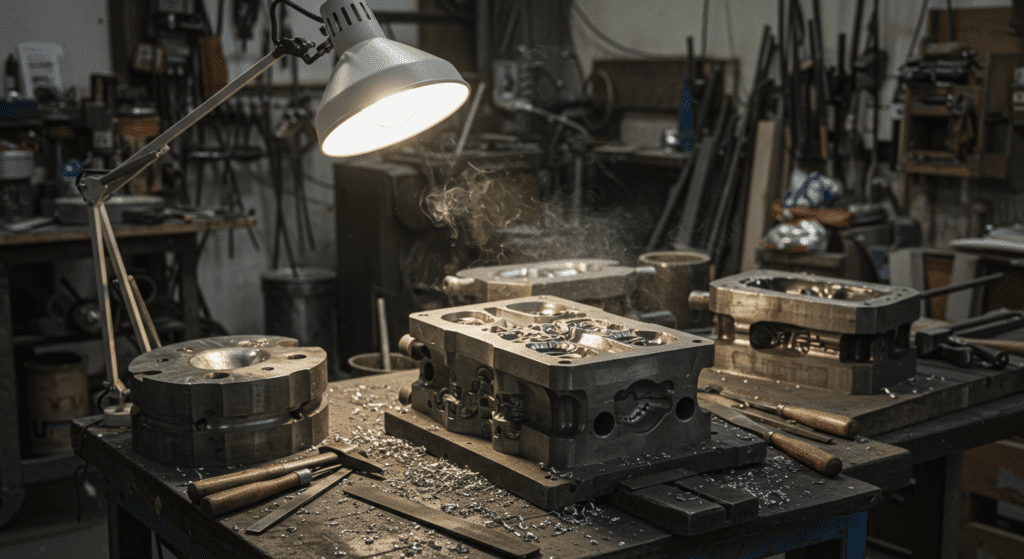
The Dawn of Metallurgy
Metal casting began around 3200 BCE when early humans discovered they could shape copper by melting and pouring it into stone molds. The first metal workers in Mesopotamia and the Balkans created simple tools and ornaments using open molds carved from stone. These pioneers laid the foundation for all modern metalworking techniques.
Copper was the first metal humans learned to cast because it melts at 1,984°F, a temperature achievable with charcoal fires. Early smiths noticed that molten copper took the shape of any container. This observation led them to create deliberate molds from clay and stone.
The Bronze Age: Alloying and the Rise of Complex Casting
Bronze casting emerged around 3300 BCE when metalworkers discovered that adding tin to copper created a stronger, more durable alloy. Bronze melts at a lower temperature than pure copper (950°C versus 1,083°C) and flows more easily into molds. These properties made bronze ideal for casting complex shapes with fine details.
The Bronze Age saw the development of sophisticated casting techniques across different civilizations. Metalworkers created multi-part molds from clay, stone, and bronze itself. They mastered the art of creating hollow castings to save material and reduce weight. By 2000 BCE, bronze casting had become a specialized craft with distinct regional traditions.
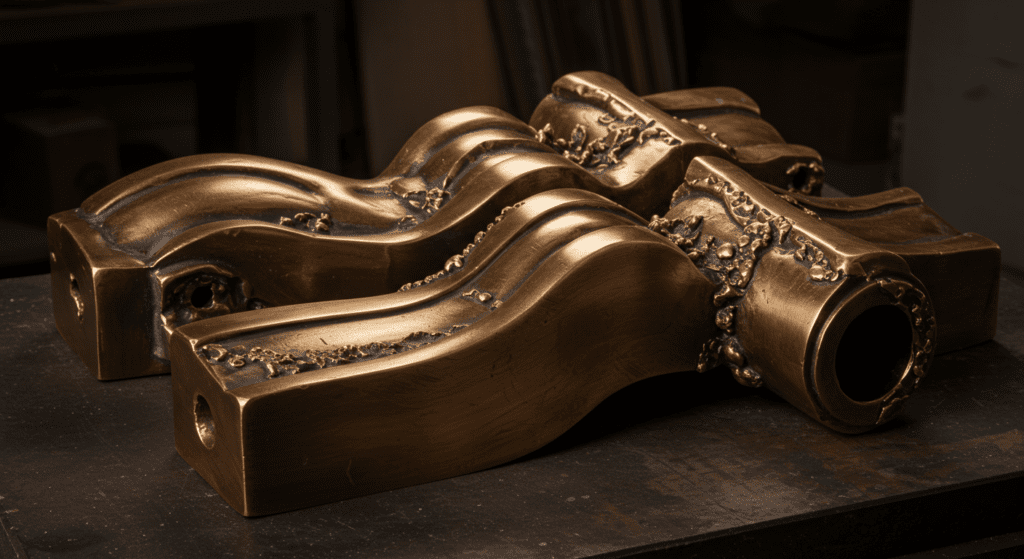
The Lost-Wax (Cire Perdue) Tradition of the Indus Valley
The Indus Valley civilization perfected lost-wax casting around 2,500 BCE, creating the famous “Dancing Girl” bronze statue. This process involves creating a wax model, covering it with clay, then melting out the wax to leave a cavity for molten metal.
The technique produces incredibly detailed castings with features impossible to achieve through other methods. Lost-wax casting spread from the Indus Valley to Egypt, Greece, and eventually throughout the ancient world.
The Piece-Mold Tradition of Ancient China
Chinese metalworkers developed piece-mold casting around 1,700 BCE as an alternative to lost-wax methods. This technique uses multiple ceramic mold sections that fit together like a puzzle. Workers carved designs directly into the mold pieces, allowing mass production of identical bronze vessels.
The Shang Dynasty (1,600-1,046 BCE) produced ritual bronze vessels weighing up to 1,900 pounds using piece-molds. These massive castings required precise temperature control and coordinated teams of workers. Chinese foundries operated like factories, with specialized workers for each production stage.
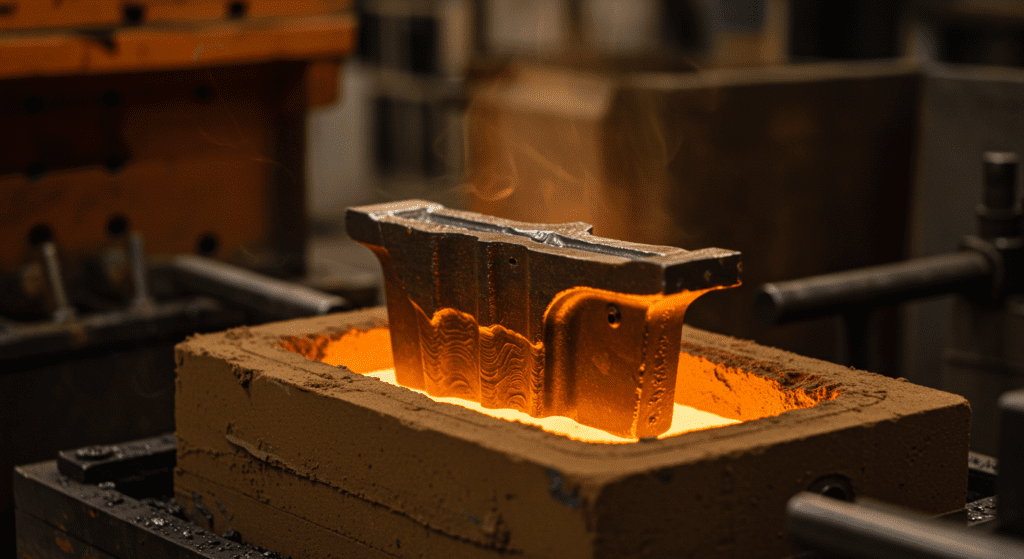
The Age of Iron and Medieval Refinements (c. 1200 BCE – 1500 CE)
Early Iron Production – The Bloomery
Iron casting presented new challenges because iron melts at 1,538°C, much higher than bronze. Early ironworkers couldn’t achieve these temperatures, so they developed the bloomery process around 1200 BCE. This method produced a spongy mass of iron mixed with slag that smiths hammered into shape rather than cast.
The bloomery dominated iron production for over 2,000 years across Europe, Africa, and Asia. Each region developed variations suited to local ores and fuel sources. African metalworkers in places like Nok and Meroe created sophisticated bloomery furnaces by 500 BCE. Their techniques produced high-quality iron for tools and weapons.
China’s Leap to Cast Iron
Chinese metalworkers achieved a breakthrough around 500 BCE by developing blast furnaces capable of reaching 1,600°C. These furnaces produced liquid iron that could be cast like bronze. Chinese cast iron appeared 1,800 years before Europe achieved similar capabilities.
Greco-Roman Bronze Mastery
Greek and Roman civilizations elevated bronze casting to an art form between 500 BCE and 500 CE. Greek workshops produced life-sized bronze statues using sophisticated lost-wax techniques. The few surviving examples, like the Riace Warriors, demonstrate mastery of anatomy, proportion, and surface detail.
Medieval European Developments
Medieval European casting advanced significantly between 800 and 1500 CE, driven by church bell production and military needs. Bell founding became a specialized craft requiring precise alloy compositions (typically 78% copper and 22% tin) and complex mold-making techniques. Master founders traveled between towns, casting bells weighing up to 20 tons.
The casting of cannons from the 14th century onward pushed metallurgical knowledge forward. Early bronze cannons required founders to solve problems of thermal stress, shrinkage, and bore accuracy. By 1450, European foundries could cast bronze cannons capable of breaching castle walls, fundamentally changing warfare.
Medieval craftsmen also refined decorative casting techniques. They produced intricate bronze doors for cathedrals, baptismal fonts, and tomb effigies. The Gloucester Candlestick, cast around 1110, exemplifies the period’s achievement in creating complex, detailed castings using lost-wax methods.
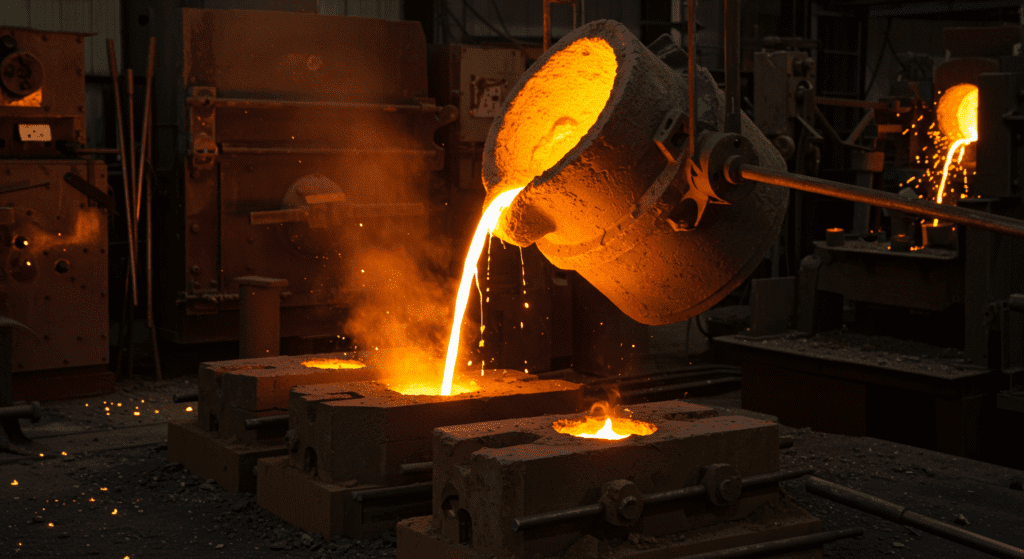
The Industrial Revolution and the Advent of Mass Production (c. 1500 – 1900 CE)
The British Iron Masters and the Fuel Revolution
The Industrial Revolution transformed metal casting from a craft to an industry between 1750 and 1850. British ironmasters like Abraham Darby I pioneered the use of coke (processed coal) instead of charcoal in blast furnaces around 1709. This change allowed for larger furnaces and continuous operation, dramatically increasing iron production.
Darby’s grandson, Abraham Darby III, demonstrated cast iron’s potential by building the world’s first iron bridge at Coalbrookdale in 1779.
Innovations in Furnaces and Processes
The 19th century brought rapid innovations in casting technology. The hot blast process, invented by James Beaumont Neilson in 1828, preheated air before injection into furnaces. This reduced fuel consumption by 30% and allowed the use of lower-grade coal. By 1860, most blast furnaces had adopted this technology.
The cupola furnace, developed for remelting iron, became the workhorse of foundries worldwide. John Wilkinson’s improvements in the 1790s created a design that remained largely unchanged for 150 years. These furnaces could melt 10 tons of iron per hour, enabling mass production of cast components.
Steam power revolutionized foundry operations. Steam-driven blowers provided consistent air blast for furnaces. Steam hammers and cranes moved heavy castings safely. By 1850, a large foundry could produce 100 tons of castings daily – work that would have taken months using traditional methods.
The development of steel casting by Henry Bessemer in 1856 opened new possibilities. Steel’s superior strength allowed for thinner, lighter castings. Railroad companies quickly adopted cast steel for wheels and couplings. By 1900, steel casting competed with iron casting in many applications.
The Scientific Age (c. 1900 – Present & Beyond)
The 20th century transformed casting from an art based on experience to a science grounded in metallurgical understanding. X-ray technology, introduced to foundries in the 1920s, allowed inspection of internal casting defects without destruction. This capability improved quality control and reduced failure rates in critical components.
Computer modeling revolutionized casting design starting in the 1980s. Finite element analysis predicts how molten metal flows and solidifies in complex molds. Modern software simulates thermal stresses, shrinkage patterns, and potential defects before any metal is poured. This reduces development time from months to days.
Modern casting incorporates technologies unimaginable to ancient founders. Vacuum casting eliminates gas defects in reactive metals like titanium. 3D printing creates complex sand molds directly from digital files. Electromagnetic stirring controls grain structure during solidification.
These advances push the boundaries of what’s possible in metal shaping. Each technique builds on thousands of years of accumulated knowledge while adding modern precision and scale.