Investment casting, also known as “lost wax casting,” is a precision manufacturing process that creates complex, high-quality metal components by forming a ceramic shell around a wax pattern and then melting away the wax. The nine-step process includes creating patterns, building ceramic shells, removing the wax, pouring molten metal, and finishing the solidified parts. This ancient technique has evolved into a sophisticated modern method that delivers exceptional dimensional accuracy, superior surface finish, and the ability to cast complex geometries in a wide variety of metals and alloys.
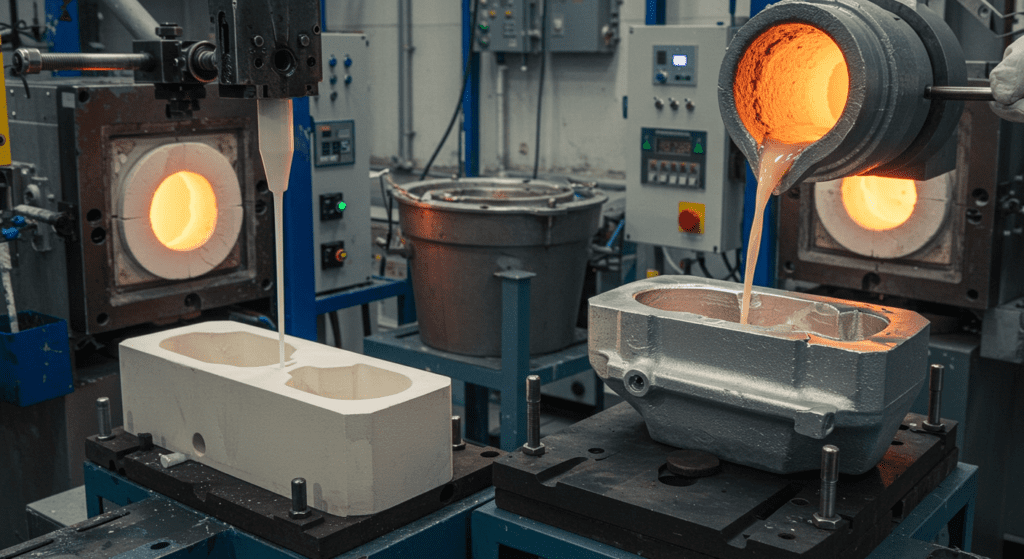
What Is Investment Casting
Investment casting stands as a sophisticated industrial manufacturing process engineered to produce metal components characterized by intricate geometries, high dimensional accuracy, and superior surface finishes. Often referred to as “precision casting” or by its historical antecedent, “lost-wax casting,” the technique derives its modern name from a critical step in the procedure. Specifically, a disposable pattern, typically fabricated from specialized wax or sometimes plastic, is “invested”—meaning clothed or surrounded—by a refractory ceramic slurry. This slurry hardens to form a monolithic mold shell.
The fundamental principle underpinning investment casting involves the creation of this ceramic mold around the sacrificial pattern. Once the shell achieves sufficient strength, the pattern material is removed, usually through melting or burnout, leaving behind a precisely shaped cavity within the mold. Molten metal is subsequently introduced into this cavity. After solidification and cooling, the ceramic mold is broken away, revealing the final metal casting.
Learn more about Investment Casting Purchasing Guidelines: Step by Step
The Investment Casting Process
1. Produce a Master Pattern
The journey often commences with a collaborative Design for Manufacturing (DFM) review between the casting provider and the customer.
Following design finalization, a precision mold, often referred to as a “tool” or “die,” is engineered and constructed. Typically machined from high-grade aluminum or steel using methods like CNC machining, this tool serves as the master mold for producing the expendable patterns.
2. Produce an Expendable Mold
The expendable patterns, which are dimensionally precise replicas of the final desired part (incorporating necessary allowances for thermal contraction), are most commonly produced by injecting molten casting wax into the metal tool.
3. Assemble Wax Patterns
Molten wax is injected into the production mold under pressure. After cooling and solidification, the wax pattern is removed from the mold. Multiple wax patterns are attached to a central wax sprue, creating what’s known as a “tree” or “cluster.”
4. Ceramic Shell Building
The complete wax tree assembly undergoes a process of shell building. This involves repeatedly dipping the assembly into a ceramic slurry, draining the excess, and then coating it (“stuccoing”) with refractory sand.
The initial slurry coats (primary coats) typically contain very fine refractory materials. After the primary coat(s), subsequent dip-and-stucco cycles employ progressively coarser ceramic materials to build up the shell’s thickness and strength.
Each layer must be thoroughly dried under controlled environmental conditions before the next layer is applied; this iterative process creates a strong, laminated ceramic shell around the entire pattern assembly. The total number of layers (e.g., 6 to 8) and the overall shell thickness are determined based on the size, weight, and configuration of the parts being cast.
5. Dewaxing (The “Lost Wax” Step)
After the ceramic shell has been built to the required thickness and fully cured (a process that can take 24 to 36 hours using traditional drying methods ), the embedded wax pattern must be removed. This critical step is typically accomplished using a steam autoclave. Inside the autoclave, high-temperature steam under pressure rapidly melts the wax pattern material, allowing it to flow out of the shell through the gating system. This leaves behind a hollow ceramic mold containing cavities that are precise negative replicas of the original wax pattern assembly. It is this removal of the pattern material that gives the “lost wax” process its name.
Alternative dewaxing techniques may be employed depending on the specific shell system used; for instance, the water glass process might use high-temperature water, while some silica sol processes utilize a flash fire approach.
6. Shell Preheating and Metal Pouring
The now-empty ceramic shell undergoes a high-temperature firing process in a furnace, typically reaching temperatures around 1000°C (1832°F).
Immediately after removal from the preheat furnace, the hot, cured ceramic mold is ready for casting. Molten metal, carefully prepared to the specified alloy composition and temperature, is poured into the mold’s pouring cup, flowing through the gating system to completely fill the mold cavity.
7. Cooling and Solidification
The filled mold assembly is then allowed to cool in a controlled manner. During this stage, the molten metal solidifies within the ceramic cavity, faithfully assuming the shape of the original pattern.
8. Shell Removal
Once the metal casting has cooled sufficiently (e.g., to be handled safely ), the ceramic shell must be removed. Because the shell is designed to be brittle after firing and casting, it can typically be broken away using mechanical methods such as vibration, impact (knockout operations), or high-pressure water blasting. Chemical dissolution methods, such as hot caustic baths, may also be employed to remove residual shell material, particularly from internal passages.
After the bulk of the ceramic is removed, the individual metal castings are separated from the central tree or sprue system. This is usually accomplished by cutting them off using abrasive saws, band saws, or sometimes cryogenic breaking or vibration techniques.
9. Finishing
Finally, the castings undergo various finishing operations as required to meet final specifications. This typically involves grinding or machining to remove the gate witness marks (the small stub left where the metal entered the part cavity).
Additional finishing steps may include sandblasting or shot blasting to clean the surface and achieve a desired texture, heat treatment (such as annealing for improved machinability, or hardening and tempering to achieve specific mechanical properties), surface treatments (like plating or painting).
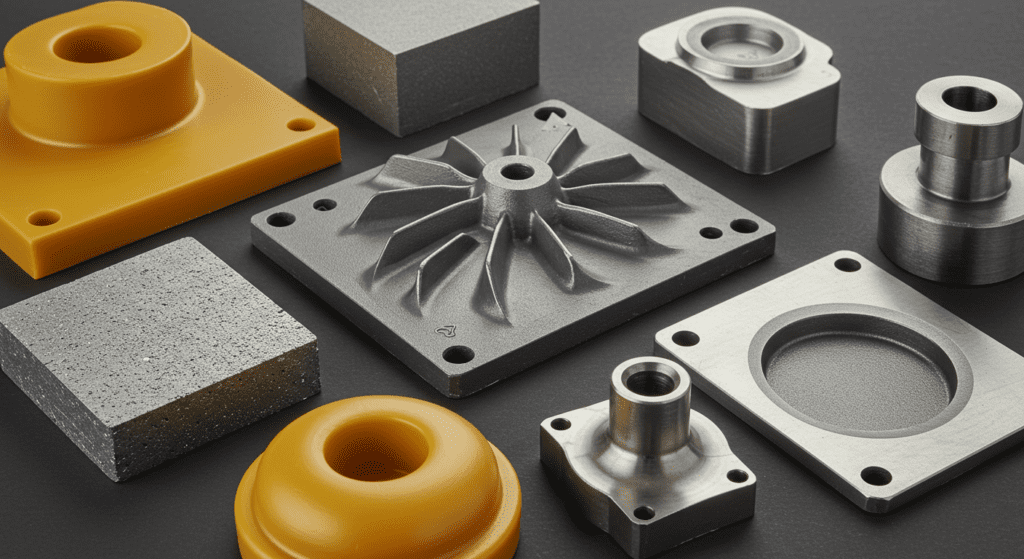
Materials Utilized in Investment Casting
Pattern Materials
The selection of pattern materials significantly impacts casting quality and process efficiency. Common options include:
- Waxes: The most prevalent pattern materials are specially formulated casting waxes. These waxes are engineered to offer desirable characteristics such as good flow properties for injection, dimensional stability upon cooling, fine surface detail replication, and clean melt-out during the dewaxing stage.
- Plastics: Certain types of plastics can also serve as pattern materials. Similar to waxes, these are typically formed by injection molding into the pattern tool.
- 3D Printed Materials: Modern additive manufacturing technologies enable direct production of sacrificial patterns using photopolymers or other printable materials. This approach reduces tooling costs and accelerates prototyping.
Ceramic Shell Materials
The ceramic shell system determines mold integrity and casting surface quality:
- Refractory Aggregates: Refractory materials like fused silica, zircon, and alumina provide the thermal resistance and dimensional stability needed to withstand molten metal temperatures.
- Binders: Colloidal silica and ethyl silicate form the matrix that holds ceramic particles together. The binder is the “glue” that holds the refractory particles together, providing green strength (before firing) and fired strength.
Process Variants
Different foundries may employ specialized approaches to shell building:
- Water Glass: The Water Glass process offers lower costs and faster shell production cycles but yields parts with rougher surfaces and lower dimensional precision, making it suitable for applications where these factors are less critical.
- Silica Sol: This process variant uses stabilized colloidal silica suspensions for enhanced shell strength and thermal stability, particularly beneficial for higher-temperature alloys.
Learn more about Types of Investment Casting
Castable Metals and Alloys
Investment casting accommodates an extensive range of metals:
- Stainless Steels: Austenitic, ferritic, martensitic, and precipitation-hardening grades for corrosion resistance and specific mechanical property requirements.
- Carbon Steels: Various carbon contents for different strength and hardness combinations in structural applications.
- Low Alloy Steels: Enhanced with chromium, nickel, molybdenum, or other elements for improved properties in demanding environments.
- Aluminum Alloys: Lightweight options offering excellent castability and good strength-to-weight ratios for aerospace and automotive applications.
- Copper-Based Alloys: Brasses, bronzes, and specialized copper alloys providing electrical conductivity, corrosion resistance, or antimicrobial properties.
- Superalloys: High-performance nickel, cobalt, or iron-based alloys designed for extreme temperature and stress applications.
- Cast Irons: Gray, ductile, and white iron variants offering cost-effective solutions for various industrial applications.
- Nickel-Based Alloys: Specialized compositions developed for high-temperature strength, oxidation resistance, and corrosion performance.
- Cobalt-Based Alloys: Known for exceptional wear resistance and biocompatibility in medical implants and industrial wear components.
- Titanium Alloys: Offering excellent strength-to-weight ratio and biocompatibility for aerospace and medical applications, despite challenging castability.
Advantages of Investment Casting
Investment casting offers numerous benefits that make it an attractive manufacturing option:
- High Dimensional Accuracy: Capable of tolerances as tight as ±0.075mm for small features, significantly reducing or eliminating secondary machining operations.
- Superior Surface Finish: Typically achieves 1.6-3.2 μm Ra (63-125 μin) surface roughness values, among the smoothest of any casting process.
- Broad Material Compatibility: Accommodates virtually any metal that can be melted, including difficult-to-machine alloys and exotic materials.
- Near-Net Shape Capability: Produces components with minimal dimensional variation from design specifications, reducing material waste and processing time.
- Reduced Material Waste: Forms parts with precise dimensions and excellent surface finish, minimizing the need for extensive machining and material removal.
- Absence of Parting Lines: Creates seamless components without the flash or parting lines inherent in multi-piece mold processes.
- Good Repeatability: Maintains consistent dimensions and properties across production runs, essential for quality-critical applications.
Disadvantages of Investment Casting
Despite its advantages, investment casting has several limitations:
- Higher Process Cost: Requires significant investment in tooling, equipment, and multiple process steps, making it less economical for simple geometries or low production volumes.
- Longer Production Cycle Time: Involves numerous sequential operations including pattern creation, shell building, and firing, resulting in extended lead times.
- Size Constraints: Practical limitations typically restrict parts to under 75 cm (30 inches) in maximum dimension and 115 kg (250 pounds) in weight.
- Design Limitations: Requires consideration of factors like draft angles, minimum wall thickness (typically 0.6mm), and adequate fillets and radii.
- Pattern Handling: Wax patterns can deform under improper handling or storage conditions, leading to dimensional inaccuracies.
- Risk of Shell Defects: Potential for cracking, bubbles, or incomplete firing can compromise casting quality and yield.
Applications of Investment Casting
The unique capabilities of investment casting make it ideal for numerous industries:
- Aerospace: Produces turbine blades, structural components, and fluid system parts with complex internal cooling passages and precise airfoil profiles.
- Automotive: Creates fuel system components, turbocharger wheels, exhaust parts, and decorative trim requiring excellent surface finish.
- Medical: Manufactures orthopedic implants, surgical instruments, and dental prosthetics with biocompatible materials and complex anatomical geometries.
- Energy and Power Generation: Supplies critical components for gas turbines, steam systems, nuclear applications, and renewable energy infrastructure.
Do you need a kiln for investment casting
A kiln is required for investment casting to burn out the wax pattern and cure the ceramic shell. The burnout process typically reaches 1350°F (732°C) to ensure complete wax removal and shell hardening. Without a kiln, the mold will not be ready for pouring molten metal.
Does Lost PLA/Investment Casting Leave Impurities
Lost PLA/investment casting can leave impurities from ash, residual binder, or ceramic shell materials. These impurities often come from incomplete burnout of the PLA or contamination during mold processing. Post-casting cleaning and finishing are required to remove them and ensure the final product meets quality standards.
is investment casting reusable
Investment casting uses wax patterns that are not reusable, as they are melted out during the process. However, the metal molds used to make the wax patterns can be reused many times. This makes investment casting a partially reusable process, with only specific components reused.
is investment casting expendable
Investment casting is an expendable mold process. It uses a wax pattern that melts away during the casting, creating detailed metal parts. Each wax mold is used once, making the process precise but not reusable.
Is investment casting environmentally friendly
Investment casting is not fully environmentally friendly due to high energy use and ceramic waste. However, it reduces material waste by producing near-net-shape parts and allows for metal recycling. Newer processes aim to lower emissions, but traditional methods still carry environmental drawbacks.