The main difference between gravity casting and centrifugal casting is how molten metal fills the mold. Gravity casting relies on gravity to fill the mold, making it ideal for simpler parts. Centrifugal casting uses high-speed rotation to force metal outward, which improves density and is suited for cylindrical parts.
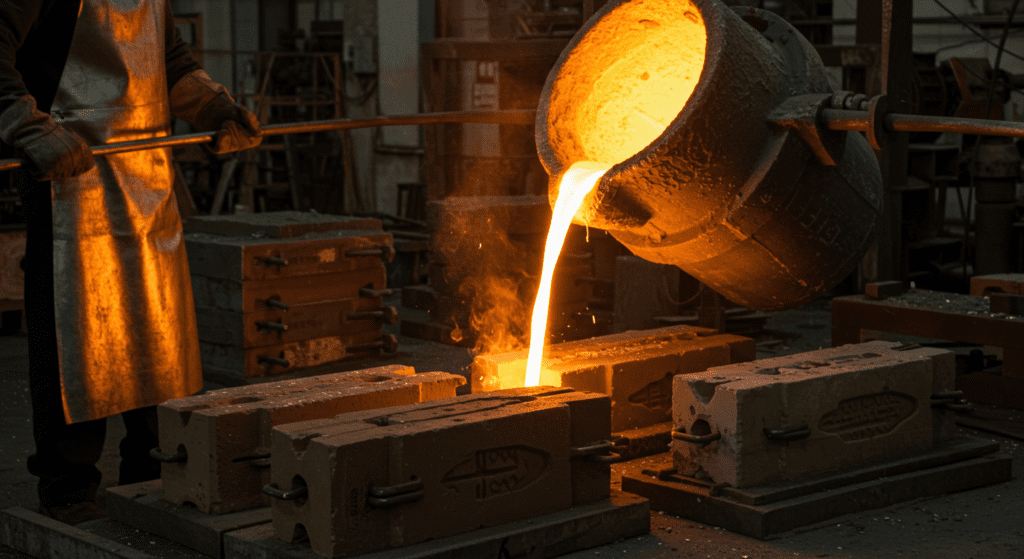
What Is Gravity Casting
Gravity casting is a metal forming process that uses the earth’s natural gravitational force to fill a mold with molten metal. The process involves pouring liquid metal from above into a permanent mold or die, where gravity pulls the material down to fill every cavity and detail.
Gravity Casting Process
- Prepare the mold – Clean the permanent steel or iron mold thoroughly and apply a release coating to prevent sticking.
- Heat the mold – Preheat the mold to 150-350°C.
- Melt the metal – Heat the chosen alloy in a furnace until it reaches the correct pouring temperature, typically 50-100°C above its melting point.
- Pour the metal – Carefully pour the molten metal into the mold opening, allowing gravity to pull it down through the gating system.
- Cool and solidify – Let the metal cool naturally in the mold for 2-10 minutes.
- Remove the part – Open the mold and extract the solidified casting using ejector pins or manual tools.
- Finish the casting – Trim excess material from gates and risers, then perform any required machining or surface treatments.
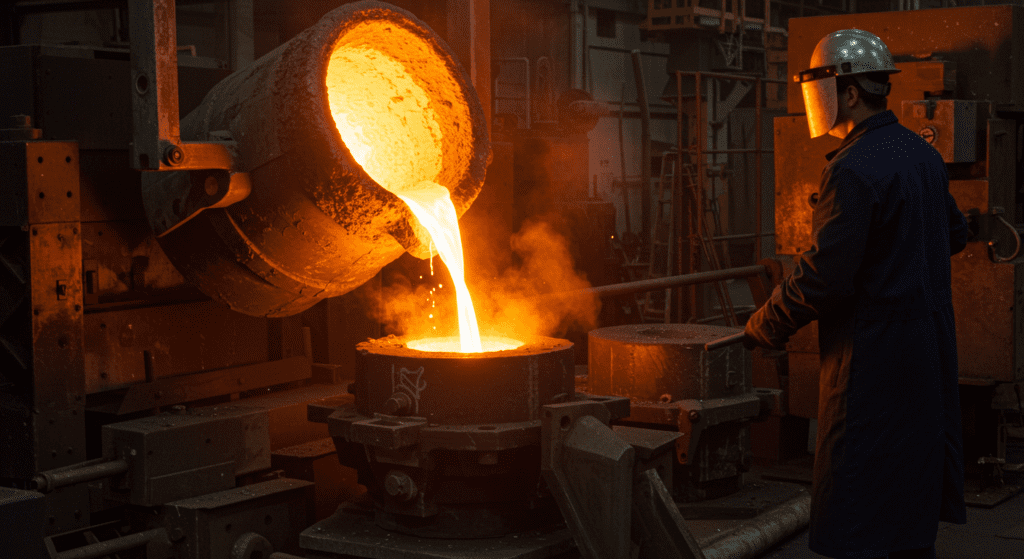
What Is Centrifugal Casting
Centrifugal casting uses spinning force to distribute molten metal into a rotating mold. The mold spins at speeds between 300-3000 RPM, creating centrifugal force that pushes the liquid metal outward against the mold walls. This force is much stronger than gravity alone, typically 50-100 times greater.
Centrifugal Casting Process
- Mold Setup: Mount the cylindrical mold on a spinning machine. Apply a refractory coating to protect the mold surface.
- Mold Rotation: Start spinning the mold at 300-3000 RPM.
- Metal Pouring: Pour molten metal into the center of the spinning mold.
- Distribution: Centrifugal force spreads the metal evenly along the mold walls. The metal forms a hollow cylinder as it spins.
- Cooling: Continue rotation while the metal solidifies. Add water cooling to the mold exterior for faster solidification.
- Extraction: Stop the rotation and remove the finished part. The casting typically requires minimal finishing work.
The Difference Between Gravity Casting and Centrifugal Casting
Aspect | Gravity Casting | Centrifugal Casting |
---|---|---|
Mechanical Properties | Tensile strength: 150-250 MPa for aluminum alloys. Moderate density with some porosity possible | Tensile strength: 200-350 MPa for aluminum alloys. Superior density with minimal porosity |
Types of Metals | Aluminum alloys, zinc alloys, copper alloys, cast iron, magnesium alloys | Steel, stainless steel, cast iron, aluminum bronze, copper alloys, titanium |
Production Costs | Lower tooling costs ($5,000-50,000 per mold). Higher labor costs due to manual pouring | Higher equipment costs ($100,000-500,000 for machines). Lower labor costs with automation |
Part Geometry | Complex shapes with internal cores possible. Wall thickness from 3-50 mm | Limited to cylindrical or symmetrical shapes. Uniform wall thickness from 5-150 mm |
Production Rate | 20-60 parts per hour. Suitable for medium volume production | 5-30 parts per hour. Best for small to medium batches |
Typical Applications | Engine blocks, transmission cases, pump housings, decorative hardware, cookware | Pipes, tubes, cylinder liners, bearing bushings, brake drums, flywheels |
Surface Finish | 3.2-6.3 μm Ra surface roughness. Good detail reproduction | 1.6-3.2 μm Ra surface roughness. Excellent outer surface quality |
Defect Types | Shrinkage porosity, cold shuts, misruns, inclusions | Segregation at inner surface, hot tears in thick sections |
Tooling Life | 50,000-100,000 cycles | 10,000-50,000 cycles |