Shrinkage cavity and gas porosity are two distinct types of casting defects that occur during metal solidification. Shrinkage creates jagged voids when cooling metal contracts, while gas porosity forms smooth, round bubbles from trapped gases.
What is Shrinkage Defects
Shrinkage defects are cavities that form when molten metal contracts during cooling. Since liquid metal takes up more space than solid metal, insufficient feed material causes voids to develop.
These defects have jagged, angular surfaces that distinguish them from gas porosity. They typically appear in thick sections where the casting process cannot supply enough molten metal during solidification.
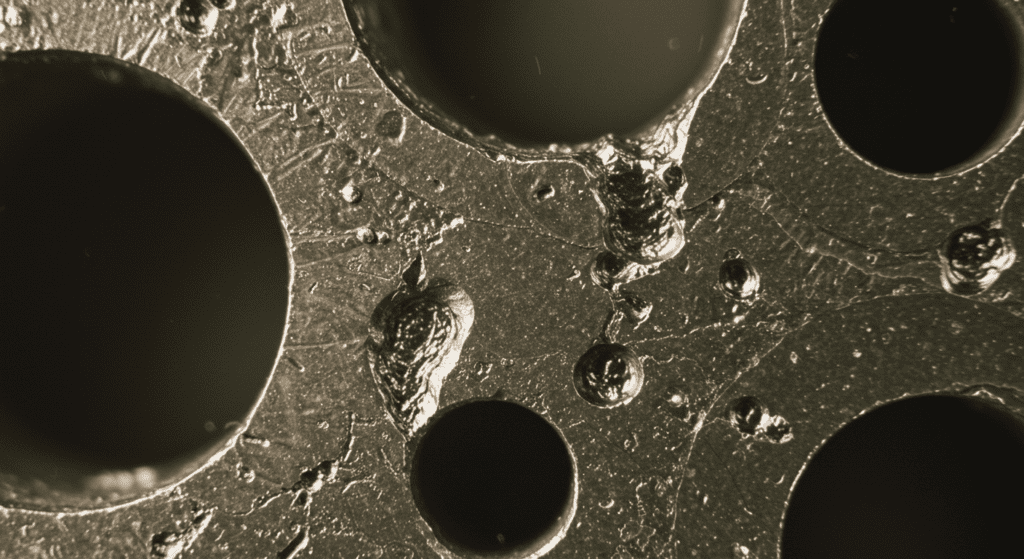
Types of Shrinkage Defects
Shrinkage defects fall into two main categories based on their location:
- Surface shrinkage creates visible depressions or holes on the casting surface. Pipes form as deep holes at the top of castings. Caved surfaces appear as shallow sinks when uneven cooling draws air into the mold.
- Internal shrinkage forms hidden cavities within the casting. Hot spots create isolated pockets where metal stays liquid longest. These internal voids can be large (macro) or microscopic (micro), depending on cooling conditions.
What Causes Shrinkage
- Casting shrinkage happens when molten metal cannot flow into solidifying areas. Thick sections without proper risers starve for liquid feed as they cool.
- Poor directional solidification worsens the problem. When thin sections freeze before thick ones, liquid metal gets trapped and cannot feed shrinking areas.
- Overheated pours create hot spots that stay molten longest. These isolated liquid pools form large cavities at their centers when they finally solidify.
How to Prevent Shrinkage Defects
- Effective shrinkage prevention requires continuous metal feeding during solidification. Risers and feeders supply liquid metal to compensate for volume reduction.
- Design your gating system for directional solidification. Thin sections should freeze first, pushing liquid metal toward thicker areas.
- Use chills or cooling fins in thick sections to speed heat extraction. This reduces cavity size by promoting uniform cooling throughout the casting.
- Maintain consistent wall thickness where possible. Add tapered transitions between thin and thick sections to improve metal flow.
- Lower pouring temperatures to minimize total shrinkage. Include proper shrinkage allowances in your pattern design.
What is Gas Porosity Defects
Gas porosity consists of smooth, round voids formed by gas bubbles in solidified metal. Molten metal dissolves more gas than solid metal can hold.
As temperature drops, dissolved gases escape and form bubbles. These trapped bubbles create weakening voids throughout the casting.
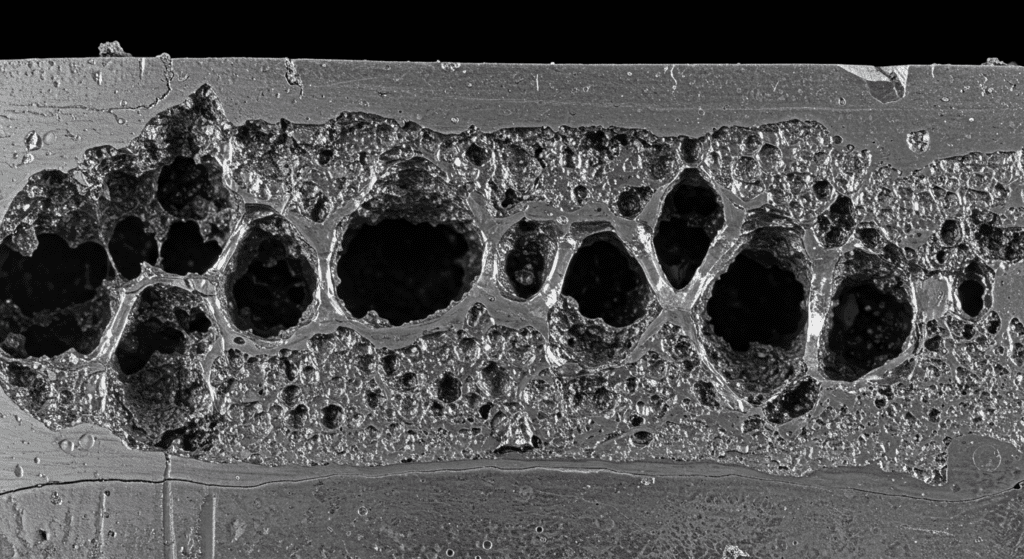
Types of Gas Porosity
Gas porosity appears in several distinct forms:
- Pinholes measure 0.5-2 mm and cluster near casting surfaces. These tiny pores often concentrate in the upper mold sections.
- Blowholes form larger subsurface cavities ranging from 2-10 mm. X-ray inspection reveals these hidden defects that weaken structural integrity.
- Surface scars occur when internal blowholes break through. These visible pits and blisters mar the casting surface.
What Causes Gas Porosity
- Gas porosity develops when gases cannot escape before solidification. Turbulent pouring traps air bubbles in the molten stream.
- Moisture presents the biggest challenge. Water vapor from damp molds or tools decomposes into hydrogen that dissolves in the melt.
- Volatile binders and coatings release gases on metal contact. Aluminum alloys particularly struggle with hydrogen absorption.
- Poor mold venting prevents gas escape. Low-permeability sand materials trap gases that should exit through proper vents.
How to Prevent Gas Porosity
- Successful gas control starts with degassing the melt. Vacuum treatment or inert gas purging removes dissolved gases before pouring.
- Flux treatments help gases float out of the metal. These refining agents bind impurities and promote gas separation.
- Keep all materials bone dry. Thoroughly dry molds, cores, and charge materials to eliminate moisture sources.
- Improve mold venting with adequate vent sizing. High-permeability sand allows trapped gases to escape during filling.
- Pour gently to minimize turbulence. Slower, controlled pouring reduces air entrainment and gas pickup.
The Difference Between Shrinkage and Gas Porosity
Aspect | Shrinkage Porosity | Gas Porosity |
---|---|---|
Origin | Metal solidification contraction: volume loss creates voids when feeders are insufficient. | Gas release: dissolved gases (H₂, N₂, O₂) come out of solution as metal cools. |
Void Shape | Irregular, angular cavities or pipes (jagged edges). Long dendritic or pipe-like shapes are common. | Typically round/oval bubbles or pockets (smooth-walled cavities). Blister/scar shapes appear when gas pockets reach the surface. |
Location | Often in thick sections or hot spots. Open shrinkage appears at the casting surface (pipes, caved surfaces); closed shrinkage (shrinkage porosity) is internal. | Can occur throughout casting. Pinholes are near-surface, blowholes are interior, and open holes are at or break through the surface. Gas pores often congregate near oxidized or turbulent regions. |
Detection | Open cavities visible on surface; internal shrinkage may require sectioning but often forms easily-detected pipes or sinks. | Surface pits and blistering are visible; subsurface blowholes require X-ray, ultrasonic or section analysis to detect. |
Key Causes | Inadequate feeding of molten metal; uneven cooling/directional solidification issues; thick-thin section mismatch. | Entrapped air/gas during pouring; hydrogen from moisture; volatile decomposition; poor mold venting. |
Prevention | Provide adequate risers/feeder metal; use directional solidification; add chills or heat sinks; design uniform sections. | Degas melt (vacuum/inert gas); use fluxes; dry molds/cores; improve mold venting/permeability; pour with low turbulence. |